An overview of techniques and programs to evaluate and improve your manufacturing.
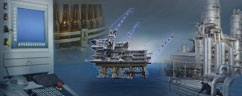
These days everyone has a continuous improvement program of some kind. Six Sigma is used quite extensively as is Lean Manufacturing. Some companies stick to one approach while others tailor their own programs using the best ideas from a wide variety of different sources.
Regardless of whichever particular flavor of continuous improvement program you use, it seems there’s always more to do. There are always more problems to tackle.
Once you solved one problem, another problem seems to pop up to take its place. But, after all, it’s a continuous improvement program so there’s always going to be more to do.
But, there are some things that can help and some tools that work really well that are geared specifically for continuous improvement programs. These tools can make a significant impact in a program and can help people working in the programs do a lot more and solve a lot more problems.
Data collection
One category of tools is data collection. The idea here is that to analyze a problem, you need lots of hard data about the problem. Guesses just won’t do. You have to know what’s actually going on. There are a lot of different ways that you can implement data collection, but the key is to get all the data you need and store it in a way that people can use.
DCS and PLC systems are great sources of data and are usually part of any data collection system. Networking is required to get the data from one place to another. And, some type of storage solution such as a data historian or general purpose database is also necessary.
Dashboards and reports
Once you have the data collected, you really need to get the data to the right people so that they can do something with it. There are lots of ways to do this and lots of ways that this can work, but the objective is just to get the data out to the people who need it.
Some people hate the word dashboards and some people love the word, but the analogy is so straightforward that it needs no explanation. There are lots of dashboard and reporting solutions out there, but the key is that they tie back to the data historian and the database and allow all the right people access to the data that they need, when they need it, and in the way that they need it.
Analytics
The idea of analytics is pretty simple. The first steps are always getting the data and then just having access to the data. Analytics takes it all a big step further by providing tools to analyze the data, slice and dice the data, look at large volumes of data, and otherwise mine the data to get the real information and the real understanding out of it all that you need.
Analytics can be a lot more than just looking at data or even developing complex reports. Analytics is all about taking the data apart and putting it back together to see trends and relationships that you never knew about before and gaining a much deeper understanding of what’s actually going on in the real world.
Metrics
The idea of metrics takes a slightly different approach to things. The idea here is to define the key data that indicates the true performance of the manufacturing operation or process. Based on this idea, many people refer to metrics as key performance indicators. The idea is not merely to look at the data or even just analyze the data, but to identify and monitor the data elements that tell you how well the operation or process is actually running.
The important point here is that you have to get beyond the data to the specific measures of the operation or process. And, the measures need to indicate how well the operation or process is actually running, which is a lot more complicated that just how fast the machine is running or how many units are being produced per hour.
OEE
OEE, or overall equipment effectiveness, is one specific metric that has become a staple in a lot of continuous improvement programs around the world. OEE attempts to measure not merely how fast a line or piece of equipment is running but its true manufacturing performance.
OEE does this by combining three metrics which are typically calculated using a lot of underlying data. Availability is calculated based on runtime and downtime. Performance is calculated based on actual versus theoretical rates. Quality is calculated based on actual first-pass quality. Together, availability, performance, and quality make up OEE and provide a very good standard approach to measuring the true performance of a manufacturing line or process.
Statistics
A specialized version of general analytics is statistical analysis. Statistical analysis in manufacturing usually takes the form of SPC (statistical process control) or SQC (statistical quality control). The short definition of SPC/SQC is the application of statistical methods to control manufacturing process or control manufacturing quality.
SPC/SQC is very valuable in manufacturing because the various statistical analyses can help you anticipate problems and avoid them before they really become problems. The statistical methods allow you to analyze trends in real-time and take corrective actions to prevent situations from becoming problems.
Conclusion
We’ve gone through a lot of ideas pretty quickly. But, you should be able to see that there are a lot of tools out there to help you with your continuous improvement program. These tools work really well and are geared specifically for continuous improvement programs. And, they can make a significant impact in a continuous improvement program. They can help the people working in the programs do a lot more and solve more problems. When you get a chance, take a close look at these tools and see if you don’t think that they can help your continuous improvement program.
This post was written by John Clemons, PE. John is the director of manufacturing IT at MAVERICK Technologies, a leading system integrator providing industrial automation, operational support, and control systems engineering services in the manufacturing and process industries. MAVERICK delivers expertise and consulting in a wide variety of areas including industrial automation controls, distributed control systems, manufacturing execution systems, operational strategy, and business process optimization. The company provides a full range of automation and controls services – ranging from PID controller tuning and HMI programming to serving as a main automation contractor. Additionally MAVERICK offers industrial and technical staffing services, placing on-site automation, instrumentation and controls engineers.