Industrial equipment manufacturers (IEMs) are companies that build a specific type of industrial equipment over and over again without much customization, which can be problematic because their focus is more on mechanical issues rather than on the electrical side of things.
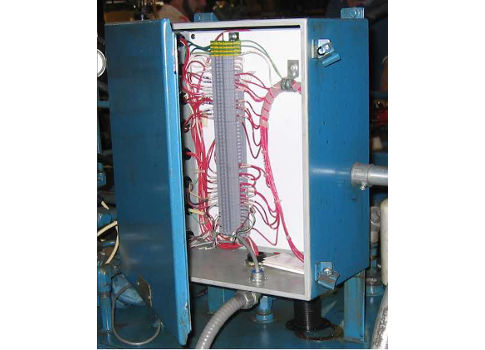
Industrial equipment manufacturers (IEMs) are companies that build a specific type of industrial equipment over and over again without much customization, such as packaging machinery, metal and plastic forming equipment (presses, injection molding machines and the like), testing machines, and other equipment controlled by programmable logic controllers (PLCs).
The dilemma is that while often very technical, these machines and systems are often designed once and with few modifications afterwards. Unlike custom machine designers, IEMs do not generally need a staff of mechanical and controls engineers.
People who start these kinds of companies often have a wealth of knowledge in their field of expertise, which is why they create and develop innovative equipment in the first place. This is how a lot of companies get started. In general, inventors and innovators who start these IEM companies are mechanical whizzes rather than controls experts. They have a good understanding of electrical and control design, which is crucial. Inside the panel of IEM equipment, the controls look like an afterthought. The panel shown is a junction box on a press that costs a half million dollars.
There are a few details a panelbuilder will notice right away:
- There are no terminal block labels.
- The wires are not very straight and there is no wireway.
- The wire labels, though they can’t be seen in this picture, are numbered.
IEMs often tend to design their equipment this way, probably because the primary focus when the equipment is designed is on the mechanical side. When the product is initially designed, the inventor or designer of the equipment goes out and looks for whatever local resources they can find. They are usually on a budget as a fledgling company, and the first electrical person hired often doubles as a service technician. After all, its not like something new is being designed every few months.
So unless an IEM consciously decides to go out and hire experienced electrical and controls design companies, that part of the machinery often lags the mechanical side. It is not economical for them to hire a full-time controls professional. And even if they did, a good controls engineer who has been exposed to the wide variety (and excitement) of challenging custom work would soon be pretty bored building the same thing all the time.
Documentation is often another problem. If the concentration is on the mechanical side of the equipment, there is a good chance that any electrical computer-aided design (CAD) work is also substandard.
Manufacturers of standard equipment like this often don’t even know there is a problem, and unless the customer complains they probably never will. They have no standard to compare it to. If equipment is sold into a manufacturing facility, the maintenance people probably know since they see equipment built by large professional custom builders, but the information generally doesn’t make it back to the IEM.
A common method of avoiding these problems is to find a professional controls company early in the development process. There are "controls houses" in every state in the country, and finding help is usually not difficult. Controls companies do design and programming for a wide variety of industries and have seen all kinds of applications. An early investment in professional help can save a lot of headaches later.
Frank Lamb is the founder of Automation Consulting Services Inc. This article originally appeared on the Automation Primer blog. Automation Primer is a CFE Media content partner. Edited by Chris Vavra, production editor, Control Engineering, CFE Media, [email protected].
ONLINE extra
See additional stories from Automation Primer linked below.