For a system to qualify as a SCADA system, it should have elements of both control and data acquisition whereas HMIs often lack control capabilities within themselves.
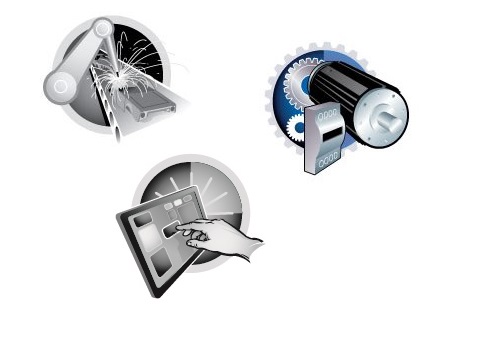
I often get asked when teaching my classes the difference between supervisory control and data acquisition (SCADA) systems and human-machine interfaces (HMIs). While there can be some overlap, especially now with enhanced HMI capabilities on CE computers or thin clients, there are some fairly clear indicators I use when defining one or the other.
SCADA is usually referred to as a system because it often encompasses multiple controllers and computers. Just because an operator interface resides on a computer, that does not make it a SCADA system. Usually, a computer is used either because other applications besides the HMI software need to run on the platform or because large amounts of data need to be stored and retrieved. I have worked on HMIs that were on a computer platform because operators or maintenance personnel needed to run a programmable logic controller (PLC), vision, or robot software, and it was more convenient to put all of the packages on the same computer.
Computer-based HMI packages often have more capabilities than a dedicated HMI. Where typical control-type HMIs have elements that can be configured to enter or display data in PLC registers, a SCADA control might do something more like the following commands inside of a single icon on a screen:
abort service_manual_operation;
& set geralnamesobject "060 M31″;
& set geralselectionsauto_man equipfbo_060_m31;
& set geralselectionsman_on_off equipfso_060_m31;
display service_manual_operation /p "060_m31″
The tags that are addressed come from two different systems and populate a faceplate that pops up when the icon is pressed. Additional instructions could easily be added to this text that moves data from one location to another, starts external applications, opens a database, or a host of other possibilities.
In my opinion, for a system to qualify as full-blown SCADA, it has to have elements of both control and data acquisition. All HMIs can change the status of data inside of another controller, but not all HMIs have control capabilities within themselves. There are HMIs with built-in I/O and control capability, but they generally don’t hold lots of archived data. There are computer systems that do lots of data archiving in Microsoft Excel or Access, but don’t really do any control other than manipulation of data inside another controller. I don’t typically consider these SCADA, though they are sometimes called by that name. Typical machine control rarely uses SCADA unless it is part of a coordinated line of machinery integrated into a plant’s IT system.
Terms such as data historian, alarm logging, and production management may imply that a SCADA system is being used on a line. SCADA is almost always present in process control, partially because control systems are large and processes may be batched or take a long time to complete. In these instances it might be important to archive lots of data and have the capability for the system to interrupt the process from outside of the controller.
There are a lot of opinions on the subject, and companies often call their data acquisition computer a SCADA system or think that because their machine has five HMIs and stores lots of data in the PLC that it must be SCADA. While people can call something whatever they want, in the interest of having to provide a definition to my students, these are the requirements I usually define for a system to properly be termed SCADA.
– Edited by Anisa Samarxhiu, digital project manager, CFE Media, [email protected]