Assigning accurate costs to compressed air, chill water, and steam generation allowed more efficient use of resources at a Thomson RCA plant and annual savings of $35,000 for compressed air alone. Electrical demand, power, pressure, and flow are among measured variables.
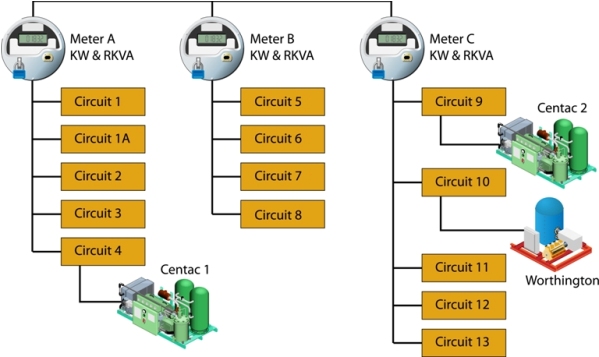
Accurate knowledge of the cost of energy production allows for more efficient use of resources for compressed air, chill water, and produce steam in a multi-building Thomson-RCA facility in Indianapolis, IN.
The energy management and information system, connected with automation hardware and software, uses analog and digital connections to field equipment to track power, equipment, and systems, for more accurate and efficient cost allocation across multiple plants and customers. More effective asset utilization, just for one compressed air unit, will save $35,000 a year. Additional savings are expected.
When French communications, media, and entertainment giant Thomson SA purchased RCA from American conglomerate General Electric, Thomson remained headquartered in Europe but operations continued at several RCA offices, including those in Indianapolis. Later, when these offices moved to a new facility north of the city, plans were made to rent the vacated space.
The old location, spread over more than 80 acres, has a central boiler plant providing chilled water, compressed air, heat, and domestic hot water to several buildings. Energy costs across multiple systems needed to be measured, optimized, and accurately allocated to various stakeholders on campus.
To get this data, Thomson-RCA implemented an AutoPilot Energy Information System designed by Holmes Energy, with Opto 22 hardware and software. Using analog and digital interfaces that connected Opto 22 I/O processors to field equipment via multiple I/O modules, the Autopilot system was able to monitor 108 I/O points. The monitored machinery and equipment included gas and electric meters, as well as chillers, cooling towers, boilers, and water heating equipment. The AutoPilot system also monitored the facility’s compressed air system—electrical demand and power consumption of two 500-hp Centac compressors and one 350-hp Worthington compressor, along with system pressure and airflow.
Data gathering
The system was initially intended to monitor only energy use and offer real-time screens detailing the status of each monitored point, individually and as a part of a group. But the system also provided human-machine interface (HMI) screens that offered data archiving and historical reports, as well as charts and graphs showing consumption and power demand in 15-minute intervals, along with monthly and annual totals.
As Thomson underwent internal restructuring, the company increased emphasis on utility cost reduction. Reports generated drew attention towards excessive energy use by the compressed air system and showed significant variation in efficiencies based on air demand and compressor. The most obvious differences seemed to occur when the Worthington (the smallest compressor) operated and during times of low demand.
Another somewhat startling discovery was the observation of a 30% variation in compressed air system efficiencies, from a low of 148 cubic feet per kilowatt to a high of 191 cf/kW.
Measure, analyze
To better determine differences among the three compressors, identify how many kilowatts each was consuming, explain variances in efficiency, and find optimum operating parameters for each under different conditions required, experimenting with different compressor combinations and loads.
In one such experiment, the first Centac compressor required 380 kW, the second Centac slightly under 350 kW, and the Worthington less than 250 kW. Based largely on this data (aggregated by the AutoPilot system), it became clear that running the Worthington alone on weekends offered the largest savings opportunity. In addition, Centac 2, thought to be identical to Centac 1, was more efficient under all conditions.
“Discoveries such as this—ones that offer tremendous revenue saving opportunities—are only made possible through the close examination that real-time monitoring provides,” says Bill Holmes, designer and integrator of the AutoPilot system. “But before one can even begin to consider how to cut costs, before any control can or should be exercised, and even before energy usage behavior can change, one needs to first closely observe and accurately measure.”
Demand cut, costs saved
Using the data gathered from the system, boiler plant personnel began changing the operating sequence for the three compressors to maintain the highest system efficiency under all operating conditions. Controls were modified to allow the Worthington to run as the primary unit with the Centacs serving as automatic backups. Data (and some quick math) showed that with good compressor management, a demand reduction of approximately 175 kW could be achieved and the facility’s compressed air requirements could still be satisfied.
Implementation resulted in nearly 64,000 kWh savings per month. Air compressor electrical costs were reduced by 20%, leading to an annual cost savings in excess of $35,000.
“In addition to tracking the power used in the buildings, we also began monitoring all of the individual equipment in the powerhouse and other facility systems,” says Thomson’s manager of maintenance, John Munchel. “With that information we were able to assign accurate dollar figures on what it cost to generate compressed air, chill water, and produce steam, and then accurately allocate costs between any departments or companies we would lease to.”
About the companies
Opto 22 develops and manufactures hardware and software for applications involving industrial automation and control, remote monitoring, and data acquisition.
www.holmesenergy.com
Holmes Energy is lead by Bill Holmes, PE, mechanical systems designer, and former professor of thermodynamics, power systems, and energy conservation at Purdue University. Clients include General Electric, DuPont, Honda, and GenCorp.
RCA