With variable frequency drive (VFD) commissioning, aspects such as design, codes and standards, and the nature of a specific project need to be considered.
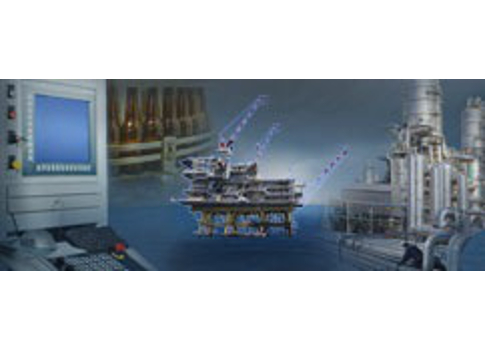
How valuable is a reduction in installation and commissioning time? Investigating some of the items discussed below can help users in choosing, configuration, and commissioning variable frequency drives (VFDs).
VFD design considerations
Are supply reactors needed to keep a clean electrical system? Are there enough VFD motors in one location that would require a supply reactor to each VFD? Is VFD technology that would require no supply reactor or reduced requirement on small VFDs being selected? Check with the electrical engineer to determine if the mixture of VFDs with other MCC devices will be acceptable.
What type of cabling, wiring, VFD-specific use cabling being used? Is it installed in EMT, rigid, stainless, aluminum, or tray? The type may have an unexpected distance restriction to the motor location. Is that motor location far enough to require a load reactor? Users should answer these questions on installation before the final design is completed.
The motor selected may be a conventional, heavy-duty, or vector quality motor. Is it an efficient NEMA motor that meets today’s standards? Check the data with a motor representative. Is that VFD for a pump, fan, or agitator application? Some VFDs are programmed differently for those motors.
When interfacing with specific vendors, ask about fail-safe modes of operation and what happens when power is lost to the programmable logic controller PLC/DCS talking to the VFD. Some VFDs, when powered up, will not respond to an already issued on (run) for safety reason unless the PLC/DCS signal is cycled off then on. Loss of a 4 to 20 mA speed setpoint may start a fail safe and trip the VFD. Learn the specifics from the manufacturer.
The client may require a positive proof that a specific VFD/motor combo has lockout/tagout (LOTO) for maintenance. The addition of a jog/off/auto setting may be added for testing the LOTO in jog at the motor. Additionally, the VFD can rotate the motor at a reduced test speed to test for operation, rotation, etc. Many European clients are using positive proof of LOTO in automation projects in Europe and around the world.
Some European VFDs require a multiplier against the users’ full load amps (FLA) to compensate for a 1.00 service factor for example. Class 5 to class 40 or NEMA standards? Some manufacturer’s state class 10 and sometimes Class 20 is equivalent to NEMA. Consult the manufacturer to get the answer.
With the factory acceptance test (FAT), are all the vendors’ special jumpers, dipswitches, and other special features installed, tested, and documented at FAT? What about when it ships to the field? It’s amazing how many jumpers are missing and how much time is wasted troubleshooting on such an easy subject.
Some manufacturers have changed parameters with specific values during FAT to coincide with internal I/O that is used within the VFD cabinets. Especially the large drives. The large drives can contain additional temperature, voltage, and monitoring devices that are pre-programmed above the factory default. Consult the manufacturer when in doubt. Always save the drive configuration before resetting to a factory default. You can compare some items.
Some VFDs use reduced voltage sources for field devices such as hand switches, safety instrumented systems (SIS) interlocks, and others. Do a little upfront engineering to assure the voltage drop from the selected VFD will work with the field device. Also, consult the VFD specifications to determine the maximum tolerances.
Configuration
Do any configuration work in the office to eliminate environmental distractions. Allow a second set of eyes after configuration to catch potential mistakes. This can save hours in the field from minor typo mistakes. Use a simulator if available and test the applications.
Proper training is vital because some VFDs today come with over 4,000 parameters and 3,000 pages of documentation to name a few. Check with the vendor and in most instances they will provide training on their VFDs at the distributor at no cost. A few days or hours with the vendor will jump-start the project and help maximize efficiency.
There are mechanical needs such as kVA vs. kW on pumps, fans, and motors during mechanical checkout. Commissioning may require a check of that pump curve. It may be in KW. Ask the mechanical commissioning guru for their needs. If there is network, assure that these requirements are a part of the network values to the PLC/DCS. Set up a commissioning page or instructions so the mechanical guru can observe without any additional involvement.
Also, pre-register with the VFD vendor. Last minute advice, manuals, firmware, or drivers may be required today instead of later. Buy a service/technical warranty package from the vendor for prompt 24-hour response. Integrator partners should receive training on the product. This will be a far more productive experience when an expert is needed.
Preparation for commissioning
On a Greenfield project, there may not be a control room built before the motor control center (MCC) and VFDs are installed. Develop a laptop with the software will allow starting of commissioning of the drives far in advance. Control rooms are great but on large projects the programming terminal may have a limited availability when several section of the plant are being commissioned at the same time with multiple personnel. If configuration is performed from the DCS, the network communications to the VFD may be down for a short time. A laptop with the proper software will allow the user to continue commissioning and troubleshooting at a moment’s notice. While an extension cord is handy for a laptop, be sure to purchase additional batteries for those long days.
Network cabling should be evaluated during installation for proper placement in the cabinet to reduce the electrical noise. Connectors should be selected to eliminate improper bend radius. Check the manufactures recommendation on grounding and shields of the network. If possible use a network tester to verify the network. Finally, check network error rates by the system. Correct as required.
USB and SD memory sticks used for firmware updates may have special restrictions such as speed and size. A number of manufacturers are still using slower and smaller memory from years ago and will not be available to update that firmware as a result. Check on this before going to the field.
Collect all literature/reference materials and put it on a thumb drive or the laptop for fast reference. The Internet may not be available on site and some industries won’t allow the use of cell phones and wireless access in the process area.
With increasing Occupational Safety and Health Administration (OSHA) regulation on electrical equipment, there will be times when it is not advised to open that VFD panel door to connect a programming cable or device without wearing flame retardant (FR) clothing and special personal protective equipment (PPE). Design a plan on how to access the VFD panel during commissioning and maintenance. Suggestions can be from installing programming cable connectors already installed to the doors in advance, pre-wire Ethernet or other networks to switches that are accessed outside the VFD panel doors, or it may be as simple as removing power to the VFD cubicle, install the programming cable connection, close the door, and repower the VFD cubicle. Is the commissioning project OSHA safe? What about configuration/maintenance in the future? Will programming in the future be done over the network with the door closed?
Commissioning
Commissioning the field devices attached to the VFD should be done first to eliminate potential issues such as miswiring and last minute instrument configuration. Commissioning VFDs is intense enough without worrying about the field devices.
Use a spreadsheet, check sheet, or signoff procedure for verification of the 20 or so critical items during commissioning. Fatigue will set in; these methods will avoid extensive rework. Make sure that DCS/PLC scaling value for example current, power, speed, etc. is really the VFD’s configured values.
With motor rotation, is it going to be corrected by hardware swapping, or by correcting the software? What is maintenance going to do when a VFD or motor is replaced?
Be aware of replacement parts, the parts may look and feel the same and come with outdated firmware. Put together a USB thumb drive or plan to allow quick loading of firmware.
Some VFDs now come with auto setup of the motor and field conditions. Some can be done with the actual motor not rotating more than a ¼ turn for safety reasons. A short bump of the motor will learn all the characteristics of the motor and electrical installation. Check with the manufacturer for commissioning requirements. This can save valuable time.
Other considerations for users
Suppose someone walks out of the MCC room and trips over construction items and drops the laptop. Is there some kind of recovery plan in place?
Correct documentation, which means drawings, checklist, and databases. There is nothing worse than incorrect field information.
Does the client have a technical staff capable of maintaining the VFDs? Provide step-by-step procedures and offer training to the client. They will be very grateful.
This post was written by Dan Auringer, P.E. PMP. Dan is a principal engineer at Maverick Technologies, a leading automation solutions provider offering industrial automation, strategic manufacturing, and enterprise integration services for the process industries. Maverick delivers expertise and consulting in a wide variety of areas including industrial automation controls, distributed control systems, manufacturing execution systems, operational strategy, business process optimization, and more.
Maverick Technologies is a CSIA member as of 8/4/2016.