The CiA 402 motion control and drives profile originally developed for CANopen systems will be extended for functional safety. In addition, A new PDO mapping was introduced, to control asynchronous as well as synchronous motor with the very same device.
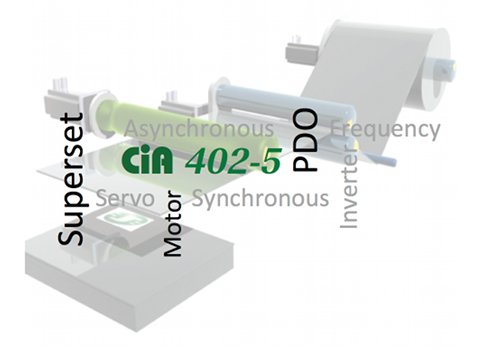
The internationally standardized CiA 402 motion control and drives profile (IEC 61800-7-201/301) is one of the most-used network profiles for electrical motors. Originally used by CANopen, the IEC standard also specifies adaptions for CC-Link IE, EPA, EtherCAT, and Powerlink. Additionally Safetynet and Varan, two other industrial Ethernet communication systems, are using CANopen-similar application layers, so that CiA 402 can be used easily.
To support functional safety, CiA 402 has been extended. In CiA 402-4, the mapping of the bus-independent functional safety for motion control developed by the EtherCAT Technology Group has been specified. The functional safety related parameters are in the object dictionary in the address range from index 6600h to 66FFh. The CANopen and the EtherCAT mapping is harmonized, meaning the parameters in the object dictionary are available at the very same indexes.
The CiA 402-4 specification includes also the SRDO (safety-related data object) mapping. The drive controller receives in the SRDO the control-word, which commands a dedicated safety function. The corresponding status-word is transmitted safely in an SRDO to the host controller. The specification includes 16 safety functions. Besides safe torque-off and safe stop, this includes functions such as safe maximum speed, safely-limited increments, and safe acceleration range.
New PDO mapping
CiA 402 specifies a generic PDO mapping as well as a type-specific mapping for frequency inverters and servo/stepper motors. Because the drive manufacturers are going to provide control units capable to manage asynchronous as well as synchronous motors, an additional PDO mapping has been developed. It is specified in CiA 402-5.
Traditionally, servo amplifiers and synchronous motors were used for positioning applications, while frequency inverters and asynchronous motors were applied for speed-variable movements. Due to increasingly powerful micro-controllers and requirements towards higher functionality and dynamics, nowadays frequency inverters virtually have the same characteristics as servo amplifiers. That means: In a large field both device types of drives have grown closer together. That is why CiA members have specified an additional PDO mapping that covers controlling of synchronous and asynchronous motors with the very same drive.
For the user this is not only convenient but also avoids the need of two different sets of PDOs. The first PDO is used to control the CiA 402 state machine and to confirm the state change request. The second PDO additionally contains the target position respectively the current position, and the third provides the target velocity or the current velocity. All these PDOs are predefined. This means that the CAN identifiers are assigned automatically depending on the setting of the device’s node-ID.
Schneider Electric will introduce drives supporting the CiA 402-5 PDO mapping in the middle of this year. The first version will support asynchronous motors. At the end of this year, this product will also be able to control synchronous motors in velocity mode. Drives featuring a positioning mode as well are planned for next year. This mode will be available for both synchronous as well as asynchronous motors.
What is PDO mapping?
The Process data object (PDO) service in CANopen is used to send unconfirmed command and status information. The corresponding PDO protocol uses just one CAN message with one to eight bytes of payload. This payload can contain one or more process data. The content of the PDO is described by the PDO mapping parameter, which contains the pointers to the process data addresses in the CANopen object dictionary. The object dictionary is the parameter list. The 24-bit address for each entry is logically divided in a 16-bit index and an 8-bit sub-index. In CANopen, the system designer has the opportunity to configure the mapping. Nevertheless, CiA 402 provides three different default mappings, which are indicated in the device type parameter (Index 1000h), so that the host controller can be programmed accordingly.