While variable frequency drives save energy, they sometimes lead to premature bearing and motor failure when not properly grounded and programmed. Beware of this “new” cause of bearing failure and know how to prevent it by eliminating common mode voltage.
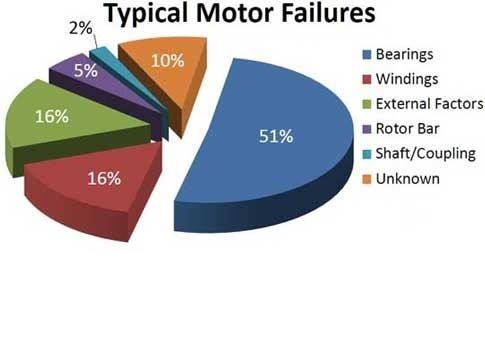
Variable frequency drives, as useful as they are for saving energy in many applications, may cause premature motor failure without proper grounding. Consider this: As a typical maintenance engineer attends to the regularly scheduled points of interest on the top of the typical commercial building or industrial plant, the days go by re-greasing motors and checking for other signs of fatigue. Without preventive maintenance tools or advanced predictive control software to provide an alarm, the engineer may stop and think, “Are those motors getting louder, or is it just my imagination?”
The experienced engineer’s internal sensors (hearing) and hunch (predictive alarm) may be correct. Over time the bearings have been experiencing premature wear without anyone being aware, but why?
Why do motors fail?
While there are many different causes of electric motor failures, the number-one cause, time and time again, is bearing failure. Industrial motors typically see a wide range of environmental factors which can lead to detrimental effects on the life of the motor.
While contamination, moisture, heat, or incorrect loading can certainly cause premature bearing failure, another phenomenon which can contribute to their failure is common mode voltage.
Common mode voltage
Most motors in service today operate on across the line voltage, meaning they are connected directly to the three-phase power source (via a motor starter) coming into the facility. As applications have become more sophisticated over the past few decades, motors driven by variable frequency drives (VFDs) have become more prevalent. The benefit of using VFDs to drive motors is to provide speed control on applications, such as fans, pumps, and conveyors, as well as running the load at optimum efficiency to save energy. One downside to VFDs, however, is the potential for common mode voltage, which may be caused by imbalance present between the three phase input voltage to the drive.
High-speed switching of pulse-width modulated (PWM) inverters can be problematic for a motor’s windings as well as the bearings. The use of an inverter spike-resistant insulation system does a good job of protecting the windings, but when the rotor sees a buildup of voltage spikes, the current seeks the path of least resistance to ground: through the bearings.
Since motor bearings use grease for lubrication, the oil in the grease forms a film that acts as a dielectric. Over time, this dielectric breaks down. As the voltage levels increase in the shaft, the current imbalance seeks the path of least resistance through the bearings. This causes arcing in the bearings, commonly referred to as EDM (electrical discharge machining). As this continual arcing occurs over time, the surface areas in the bearing race become brittle and tiny pieces of metal can break off inside the bearing. Eventually, this damaged material works its way between the bearing balls and the bearing races, causing a grinding effect, which leads to frosting or fluting (and can increase ambient noise, vibration, and temperature of the motor, along the way). Some motors can continue to run as this gets progressively worse. However, depending on the severity of the problem, the eventual demise of the motor bearings may be unavoidable, since the damage already has been done.
Grounded in prevention
What one would hope happens in installation is that the motor and drive are installed, wired, grounded, and programmed as specified by the manufacturer. NEMA (National Electrical Manufacturers Association – the trade association for the motors and drives industry) provides a guide to assist in best practices as well. Industrial applications typically don’t experience these bearing difficulties on inverter-fed motors. But in some installations such as commercial buildings and airport baggage handling, robust grounding is not always available.
So, what is one to do to divert this current away from the bearings? The most common solution is to add a shaft grounding device to one end of the motor shaft, especially in applications where common mode voltage can be more prevalent. A shaft ground is essentially a means to connect the turning rotor of the motor to earth ground via the frame of the motor. Adding a shaft grounding device to the motor prior to installation (or buying a motor with one pre-installed) can be a small price to pay when compared to the price tag of maintenance costs associated with bearing replacement, not to mention the high costs of downtime in a facility.
A couple of types of shaft grounding devices are common in the industry today. The old faithful carbon brush mounted in a holder is still prevalent. These are similar to a typical dc carbon brush, which essentially provides the electrical connection between the rotating and stationary portions of a motor’s electrical circuit.
A relatively new device to the marketplace is the fiber brush style, ring type device. These devices work in a similar fashion to that of the carbon brush, but do so with multiple strands of electrically conductive fibers arranged inside a ring around the shaft. The outside of the ring remains stationary, typically mounted to the endplate of the motor, while the brushes ride on the surface of the motor shaft, diverting the current through the brushes and safely to ground. On larger motors (above 100 hp), however, regardless of which shaft grounding device is used, it is generally recommended that an insulated bearing be installed on the opposite end of the motor from which the shaft grounding device is installed to ensure that all voltage in the rotor discharges through the grounding device.
3 variable speed drive installation tips
Three considerations for the maintenance engineer when trying to reduce common mode voltage in VFD applications are:
1) Ensure that the motor (and motor system) is properly grounded.
2) Determine the proper carrier frequency balance, which will minimize noise levels as well as voltage imbalance.
3) If a shaft grounding device is deemed necessary, select one that works best for the application.
– David E. Steen is product manager, definite purpose motors, Baldor Electric Co., a member of the ABB group. Edited by Mark T. Hoske, content manager, CFE Media, Control Engineering, Plant Engineering, and Consulting-Specifying Engineer, [email protected].
ONLINE
Manufacturing: Get lean, flexible, and improve product flow
Motor efficiency: Motor efficiency requirements come December 2010. Are you ready?
Protect motor bearings from shaft currents
Key concepts
- Variable frequency drives save energy.
- VFDs can cause common mode voltage and ground faults through bearings if not installed properly.
- Grounding the motor shaft can be the cure.
Consider this
In addition to proper grounding, shouldn’t your most important motor-drive systems include advanced diagnostics?