Companies should expect to start hearing a lot more about FDI in 2016, as products that support this new device integration standard come to market. Control Engineering Europe reports on FDI's journey so far.
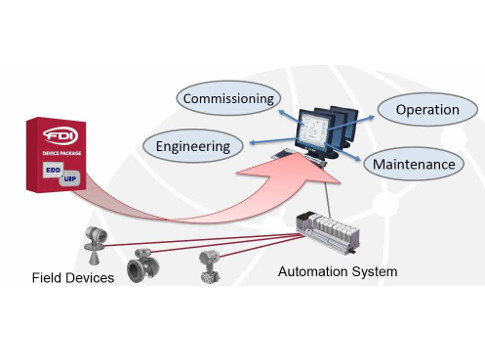
After a four-year effort, on June 28, 2015, the FDI Cooperation LLC declared victory and elected to disband. Initially formed in 2011, the 40-person FDI Cooperation team, represented by technologists from major suppliers and field communication foundations, set out to resolve a host system integration problem said to have become a nightmare for device manufacturers, host system suppliers, and end users.
Victory in this case means three things: first, approval of the IEC 62769 standard, Field Device Integration (FDI); second, transfer of core tools and technology from the FDI Cooperation to the major process industry communication foundations who will, in turn, provide some or all of the training, product registration, maintenance, and enhancement services needed to assure a thriving eco-system of FDI approved devices, controllers, and host systems; and finally, the announcement by the recently formed FieldComm Group of the availability of new releases of the tools necessary for creating FDI registered systems and devices.
"The partnership worked very well because the activity was strongly supported by the process control industry," says Achim Laubenstein, manager of fieldbus standardization at ABB who previously served as FDI Cooperation’s executive director and is now technology director at FieldComm Group. "The original complaint was users had many field devices with lots of data, but they couldn’t use it because they had no single integration technology and lacked interoperability. That was the problem FDI Cooperation’s members took up."
Historical overview
In the early 1990s the text-based Device Description Language (DDL) began to be used to author Device Descriptions (DDs) for many process-centric instruments. Initially the DDs simplified the integration of digital information gathered from the device to the control system. Over time, as multiple versions of DDL emerged, integration became more complex. Eventually, efforts to standardize DDLs began, ultimately resulting in the release, in 2006, of the EDDL specification as IEC 61804.
Meanwhile, in the late 1990s, principally driven by the more data intensive needs of ever more sophisticated devices, work on FDT/DTM technology also was underway. In 2005 the FDT group was founded to manage and evolve this technology. Unlike EDDL, FDT requires the writing of device-specific software applications and their integration into the host through standardized Microsoft Windows-based interfaces.
On the host system side of the equation Microsoft Windows-based operating systems (OS) became the norm, and so host systems became linked to Microsoft operating system software upgrades. Some host systems suppliers only supported FDT/DTM, others only supported EDDL, and few supported both. As new Microsoft Windows Service Packs and full version releases were made, each DTM needed to be re-verified with the new OS. Often, changes in a DTM were required to function in the new version of the OS.
The burden of integration of the device to the host system was spread across the value chain. Device suppliers needed to develop, test, and register a DD for each device. In addition, they were required to develop, test, and register a DTM across multiple versions of Microsoft Windows OSs for each instrument they manufactured.
Host system manufacturers had to choose between EDDL and FDT/DTM-based platforms and then needed to develop and support that platform. DTM testing and registration organizations were forced to upgrade test protocols to keep current with the latest version of the OS.
End users were faced with extremely challenging device integration burdens and the common problem of an EDD or DTM not being available for a specific instrument.
All of these factors contribute to inefficiency, cost increases, complexity, and a tendency to avoid system upgrades. As a result many host systems in brownfield installations are operating with software versions sometimes 10 years outdated.
Enter FDI
"FDI improves interoperability between field devices and host systems through the use of FDI Packages," said Laubenstein. "FDI Packages include everything a host system needs for consistent device visualization and parameterization across platforms" (see Figure 1).
"The big advantage of FDI is it replaces various platform-dependent integration solutions and makes device packages interoperable with host systems because their device descriptions are harmonized across the communication protocols and host systems. This saves users a lot of time and effort and gives them access to device data they didn’t have before, so they can create more value for their applications."
FDI combines EDDL and FDT/DTM technologies. Benefits of text-based EDDL are realized for set up and parameterization, and an optional software interface is available when needed. According to Martin Zielinski, director of HART and Fieldbus Technology at Emerson Process Management, "Text-based EDDL is used to set up our device to measure the physical properties of flow, pressure, and process temperature.
But to calculate mass flow, certain parameters from a database are required. With FDI we can add a software application that does this. FDI can do both text-based functions and then display calculated parameters like mass flow because it combines EDDL and the software application that is a derivative of FDT. This also allows FDI to perform complex diagnostics in a valve, such as a partial-stoke test."
Device vendors provide a device package for their devices, which is a virtual representation of the device and provides all information needed by a host system. By running the package, a host system provides all the device functionality to the user such as parameterization, diagnosis, and maintenance. A FDI Package allows added device data to be accessed through one integration technology. With FDI, the end users get access to their valuable device information.
Adopting FDI
Simultaneous with the transition of the FDI Cooperation technology to the global foundations, ABB and CodeWrights announced the availability of the first FDI products. Most major suppliers are aware of and are planning development of FDI-supported products. Rapid and significant FDI market adoption requires initiative from all parties in the supply chain, including independent foundations such as FieldComm Group.
Device manufacturers need to train their staffs, create a roadmap for FDI for all instruments, and then develop and test.
Host system suppliers must incorporate the FDI common component architecture into their host system software. For some suppliers this is a straightforward task, for others it represents a significant development effort.
The FieldComm Group prepares qualification test suites, training materials for device suppliers, host system manufacturers, and end users.
And finally, end users need to upgrade their systems to support FDI. Similar to host system suppliers this could be a simple or arduous task based on the release level of the current control system.
When FDI works through the supply chain the benefits should be significant and include:
- For a given device, one FDI device package with all configuration information, documentation, and display information that works with all host systems registered as FDI-compliant.
- Minimal dependency on Microsoft versioning for those devices that require an optional software application.
For end users and suppliers, the benefit is clear. FDI standardizes integration of field devices through a future-proof technology that ensures unrestricted interoperability of device packages from a wide variety of device manufacturers with FDI compatible hosts from multiple control system suppliers.
FDI is a support technology that provides a means to easily integrate digital information into host systems.
Get additional insights about FDI from automation vendors.
Control Engineering Europe posed some of the most frequently asked questions about FDI to automation vendors.
Q1. How do you see FDI fitting into the developing Industry 4.0 architecture?
Achim Laubenstein, manager of fieldbus standardization at ABB: FDI is designed to bring field devices to the Industrial Internet of Things (IIoT). It fits seamlessly into the Industry 4.0 architecture and is referenced by the Reference Architecture Model (RAMI). Real devices are represented as virtual objects in the FDI Server. By this all device data is accessible by other applications in a standardized way. FDI can also bring the data of existing field devices (installed base) into the Internet of Things (IoT) without changing the device itself. Only a device package is required.
Martin Zielinski, director, PlantWeb Technology, Emerson Process Management: One theme of Industry 4.0 is to provide end users with actionable information from a variety of different devices. FDI is the underlying technology that translates the raw data delivered via HART, Foundation Fieldbus, Profibus PA/DP, or Profinet communication protocols into information upon which end users can take action.
Q2. What benefits will be offered to the end user as well as system integrators and machine builders?
Laubenstein: The key benefit for end users, device vendors, systems vendors, system integrators, and machine builders is interoperability. The device package delivered with the device will fit all systems. In addition, device vendors and system vendors will make cost savings as they need only support only one solution (FDI) instead of several DD variants and FDT.
Zielinski: FDI is an integration technology. Today, there are multiple integration technologies. End users sometimes cannot use their preferred device because the system doesn’t support the integration technology used by the preferred device. FDI is intended to provide one integration technology used by all systems and devices and was developed by a consortium of suppliers and standards organizations for this express purpose.
Q3. What traditional device management problems can FDI help overcome?
Zielinski: In a word-commissioning. For a given field device, there will be a single FDI Device Package that can be used by all host systems registered as FDI compliant. Not having the correct integration file for the host can delay system start up or device replacement.
FDI and FDT: living in harmony?
In January 2015 Control Engineering Europe reported on comments made by Glenn Schulz, managing director of the FDT Group, which explained how FDI will sit alongside the FDT standard. He said, "The release of the FDI standard will result in the creation of a single, common, interpreter for all the different EDDL files across the EDDL-based networks. This will simplify the architecture from a host perspective and should dramatically improve interoperability going forward."
"The FDI standard will also add improved graphics capabilities for device configuration. EDDL has been somewhat limited in terms of what it can do graphically." FDI, he said, would bring highlight interactive graphics capabilities to EDDL.
One of the key considerations in the development of FDI was that it was designed to be compatible with the FDT standard-and to avoid even more competing industry standards. It is designed to support EDDL-based standards. However, there are many other networks being used in industry today that need to be integrated to build a complete solution. A method was needed to bring them all together, to create scalable solutions. This is where the FDT standard comes into play, with its ability to standardize the communication and configuration interface between all field devices and host systems.
FDT technology provides a common environment for accessing features of a device via a DTM (Device Type Manager). A DTM, which is supplied by the device vendor, is a software representation of the device, and it can offer a host of functions. It can assist with device configuration and diagnostics, it might also be able to handle troubleshooting, and will also include a device manual. The network communication devices are also represented by a DTM making the standard highly flexible for the end user.
"Although the FDT standard and the FDI standard share many similarities, they are not the same," said Schulz. "An FDI host, for example, is not able to support DTMs. It can only support EDDL-based networks. This is why we talk about integrating FDI into FDT." Any number of DTMs can be loaded into the FDT host, which is able to talk to any number of industry networks. "When FDI-based devices do start to appear, a special DTM-called an FDI DTM-will be created. Inside this FDI DTM will be the common EDDL interpreter, which is needed for the FDI standard, as well as the other components that support the FDI standard."
"With an FDI DTM solution all the FDI functions will be fully enabled within FDT with no limitations. All FDT DTM features are also fully enabled, making it possible to take DTMs for devices on any of the industrial networks or fieldbuses and use them within this integrated solution."
Suzanne Gill, editor of Control Engineering Europe. Edited by Joy Chang, digital project manager, Control Engineering, [email protected].
ONLINE extra
See additional stories from Control Engineering Europe about FDI linked below.