Deciding whether to repair, replace, or retrofit an asset within a plant depends on business goals and operation and maintenance requirements of each asset in a facility.
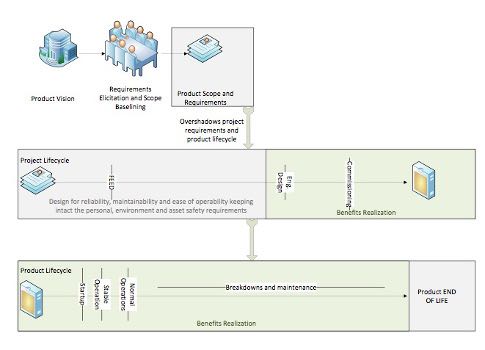
A key factor in determining the performance of any plant or facility is a thoroughly designed system that includes effectively monitoring operations and maintenance requirements, which play a critical role in sustainable production, process availability, and plant reliability.
Plants and facilities aren’t different from humans in the sense that they are made up of numerous assets (organs) where each has its own criticality, requirements, and constraints and must all work together to ensure sustained operation. Just as human fitness depends on lifestyle choices and receiving medical attention when faced with health issues, ensuring optimal performance in facilities depends on business goals and operation and maintenance requirements of each asset in a facility (see Figure 1).
When dealing with maintenance of any asset, the decision will come down to one of the three R’s: repair, replace, or retrofit. Choosing which option is best depends on a number of factors such as business goals, criticality to process, and the asset’s lifecycle relative to the project’s lifecycle.
Typical assets include production systems, generators, compressors, pumps, and control systems that automate and integrate all these assets for efficient operations. Each asset has unique maintenance requirements and criticality to facility operations.
The decision to repair, replace, or retrofit is based on a needs analysis of equipment function and its failure case. This analysis usually needs to be done on a case-by-case basis. The following criteria need to be considered in the design phase for ensuring operability and maintainability:
- Cost-effectiveness of the equipment for repair, replacement, or retrofitting-labor costs and downtime because of the activity
- Durability of the equipment, i.e., the operating cycles that can be performed by the equipment before it needs a repair or replacement of parts
- Reliability requirement of the equipment being repaired or retrofitted-selection of system based on time required for repairing
- Capability of the system to handle complexity of a process and its functional safety requirements
- Regulatory requirements of the government or international regulatory bodies
- Industry standards requirements and best practices from previous experiences
- Requirement for compliance for certification
- Contractual requirements due to partnerships, warranties, and original equipment manufacturer (OEM) requirements
- The company’s standard operating procedures.
The example shown in Figure 2 compares different types of failures and typical analyses performed to determine remedial action.
IEC61508—Functional Safety of Electrical/Electronic/Programmable Electronic Safety-related Systems—defines the mean-time-to-repair (MTTR) as the total time it takes to repair starting from time of failure to its subsequent startup, taking into account the travel time, location, spares holding, service contracts, environmental constraints, etc.
This standard also calls for the identification of modes of operation of plant-normal mode and abnormal mode. If the repairing time in abnormal mode exceeds procedural standard repair time, then additional actions need to take place to maintain a safe state.
The repair of faulty sub-systems within the MTTR period is calculated on probability of random hardware failure. During this time, continued process safety is ensured by additional measures and constraints. The risk reduction provided by these measures and constraints needs to be at least equal to the risk reduction provided by the safety instrumented system in the absence of any faults.
System maintenance is as important as having a good workable design. For example, in control valves many good control schemes fall into disuse because of a lack of proper fine-tuning, failure to adapt to changing process requirements, or poor maintenance. Over time, process parameters change in aging plants while control valves are subjected to continuous wear and tear, which may eventually lead to alarms and failure. An easy remedy to such situations would be to re-tune some controllers, but good maintenance cannot be replaced with just re-tuning. If the equipment fails, the loop should not be re-tuned; the piece of equipment should be repaired.
Another example is the case of economic justification for using a valve with a threaded bonnet. These are usually based on a life-cost model of "discard and replace," whereas larger valves, bolted bonnet valves, and control valves typically require a "maintain and repair" cost analysis. In special cases, the bonnet-to-body joint can be seal welded to prevent leakage of highly reactive, lethal, or radioactive fluids and then the repair or replace has to be planned and executed accordingly.
Ongoing optimization of older assets significantly reduces the cost and personal safety risks in the continuous presence of personnel on site. These activities are managed by initiating and executing retrofit projects.
An example is a facility from an offshore project that had been running for 30 years and could not afford an overhaul because of the end user’s production constraints. The provided solution involved several facets. The pneumatic controls were replaced with electronic controls and intelligent transmitters, and retrofit kits on valves with self-checking and self-validating function were installed. Self-diagnostics are important because the reliability of the measurements is essential for proper control and eventually reduces the mean time between repairs. The monitoring system was upgraded with asset management software, which reduced field maintenance costs and allowed re-calibration and troubleshooting of electronic systems from central control rooms.
In another retrofit project, field devices were upgraded to electronic control, and input/output (I/O) racks were added to a PLC5-based system. The control system was replaced with a higher memory model since the current system was already maxing out on program memory while utilizing the same human-machine interface (HMI) application. The retrofit was a very cost-effective solution, and minimum learning was required of plant operators to monitor and control the retrofit system amicably. This helped the end user save on a potential replacement of all its systems, which would have cost significantly more.
– Ammad Ahmed Baig is project manager at Intech Process Automation. Intech Process Automation is a CFE Media content partner. Edited by Chris Vavra, production editor, CFE Media, Control Engineering, [email protected].
ONLINE extra
– See additional stories about maintenance and machine safety linked below.