Changing demographics and the ability to deploy trainers to remote locations are driving new technologies for the next generation of operators.
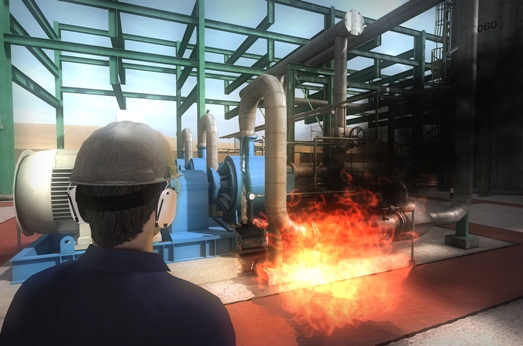
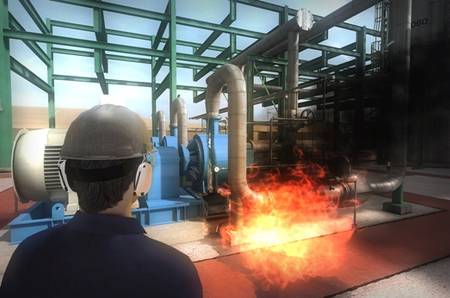
Now imagine a different scenario: A new plant is getting ready to open in a very remote part of the world where there are few process plant operations. The company is having difficulty attracting experienced operators and trainers to that location and is stuck trying to do its best working with locals who have little or no relevant experience. Those trainees probably won’t learn from a few hundred PowerPoint slides either.
These types of situations are becoming ever more common, and the associated problems are visible to suppliers trying to fill the gap. From time to time, Control Engineering has discussed various approaches using new technologies borrowed from the video gaming industry to train new operators. Simulation techniques are a common denominator of some of the more interesting solutions, and they permit trainees to visit a 3D representation of a plant facility where they can turn valves, change operating setpoints, and sometimes fight fires or other disasters. The model can be as realistic as necessary—exactly like the actual plant, in some cases—because such simulations are generally purpose-built for a specific facility.
Eyesim, by Invensys, is a platform that creates an immersive virtual reality experience. It starts with a process simulation that can duplicate what’s going on in the reactors, distillation towers, and pipes so that trainees can understand how the process works. It contextualizes that in a 3D model so trainees can do a virtual walkthrough of the facility. If someone closes a valve or starts a pump, the process will respond appropriately.
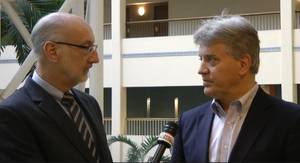
Fraser says that younger operators take to the virtual experience naturally, thanks to years spent playing video games. Others who might have come through the military, for example, also have extensive experience with this kind of training approach. The demand for adopting this kind of process will continue to become clearer as circumstances change, technologies develop, and costs become more attractive.
Peter Welander, [email protected]