The ability to program and control robots, servos, and drives with one software package is available with the Yaskawa Singular Control concept. Yaskawa’s MotionWorks IEC development platform uses IEC 61131-3 programming languages and motion function blocks that conform to PLCopen standards. The software was shown at Pack Expo 2015 in Las Vegas, demonstrating a Robotic Case Packing application.
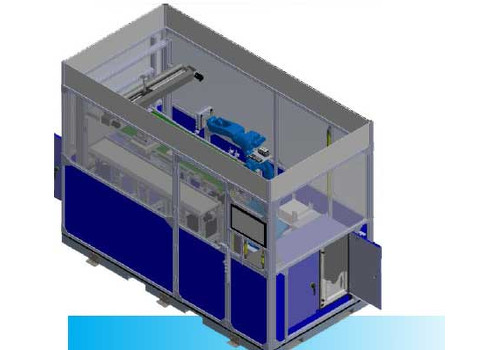
Yaskawa MotionWorks IEC Pro Machine Controller software, part of the MotionWorks IEC development platform, can operate Yaskawa Motoman brand robots, Yaskawa servos, variable-speed drives and related logic for each without need for a specialized robot programmer. The company calls this unified programming environment Yaskawa Singular Control. It uses IEC 61131-3 programming languages and motion function blocks that conform to PLCopen standards. The software was shown in a demonstration of the Yaskawa Case Packing Toolbox and Yaskawa Motoman brand robots on an example robotic case-packing application.
In a discussion with Control Engineering prior to the show, Doug Meyer, Yaskawa motion project manager, explained, "The Singular Control strategy brings three main Yaskawa product lines together, robots, servo motors, and ac drives, all controlled by one controller in one environment to increase usability and flexibility and to reduce costs."
The work cell demonstration eliminates the need to manage multiple controllers, incompatible software, and competing control vendors. Development is said to be faster and easier with Yaskawa’s Case Packing Toolbox application function blocks, which allow engineering work to be completed in less time without losing the freedom to customize an application to specific case-packing needs, the company said. Application Toolbox function block packages continue to be developed for other applications.
Programming benefits
Benefits of Yaskawa Singular Control, Meyer said, include:
- Versatility: Run Yaskawa Motoman robots, standard kinematic mechanisms (such as gantry T-Bots and H-Bots), or custom mechanisms using the same application code. For example, a user could develop a case-packing application using a gantry mechanism, then convert to a robotic mechanism with very few program changes.
- Ease of use: Yaskawa Motoman robots and Yaskawa servo motors are programmed using familiar ladder logic and function blocks. Internal engineers can develop robotic applications without needing to learn a proprietary robot language.
- Lower cost: Having one software package for motion development, configuration, and maintenance simplifies design and reduces development costs for the original equipment manufacturer (OEM) or system integrator (SI). It also lowers the cost of training, installation, and maintenance for the machine’s end user.
- Web interface: The controller provides operation and diagnostic data without the use of proprietary software, with the ability to monitor system status through any Web browser from any location.
Easier case packing
Features of the Yaskawa Case Packing Toolbox include:
- Teach Pendant Toolbox: Uses a teach pendant to manually teach user frames, interference zones, and move points. Use the same teach pendant for manually jogging robots or any other servo axes.
- Path Generator: Enter the case packing data (case size, product details, and pack pattern) and the PathGenerator creates a complete, adjustable robot path for the pick-and-place sequence, including support for mixed cases and multiple pack patterns.
- Path Processor: Executes and coordinates motion sequencing and error recovery.
- Conveyor Tracking: Enables the tracking of moving parts in any configuration for easy, accurate picking and packing.
The full integration of a packaging line often requires working with multiple controllers and software packages, creating problems with incompatible programming languages, technical support, and training, Yaskawa said, resulting in extra cost, logistics nightmares, and uncertain reliability. Yaskawa can support all the major control components of a case packing machine and integrate seamlessly with upstream and downstream equipment, especially when Yaskawa’s PackML Template is used as the code foundation.
Easier integration, future opportunities
Supporting applications will converge into the new Singular Control platform as well, as more function blocks are created to integrate robotic control.
"We’re in the process of harmonizing robot control into [a] library of PLCopen motion function blocks," Meyer explained, "and will continue to develop application specific blocks, such as the case-packing toolbox of functions, as demonstrated at Pack Expo this year."
He expects the new approach to ease integration of robotics into other processes as all axes of motion are handled as a group, rather than individually. With the new functions, robotic programming via a teach pendant will be optional, which could save several thousand dollars, he added. Fewer software packages also will decrease the need for training over time, he added.
Yaskawa Drives & Motion Division, Yaskawa America Inc., is based in Waukegan, Ill. The company says it is the world’s largest manufacturer of robots, drives, and motion control components, with annual manufacturing of 20,000 robots, 800,000 servo amplifiers, 900,000 servo motors, and 1.8 million variable-speed drives.
– Mark T. Hoske, content manager, CFE Media, Control Engineering, [email protected], with additional source material from Yaskawa.
Key concepts
- Universal programming software works with robots, servos, drives from Yaskawa
- Software uses IEC 61131-3 programming conventions, motion function blocks, and PLCopen standards
- Software saves time and can eliminate a robotic teach pendant.
Consider this
How many software programs are used for motion and robotics? How many would you like to use?
ONLINE extra
www.yaskawa.com