Recently the wireless industry has seen new advances in Wi-Fi-enabled devices in the commercial space. New features to improve throughput are becoming standard for many commercial devices.
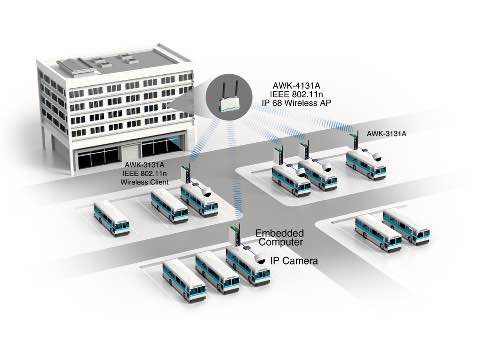
Today’s industrial Wi-Fi networks are primarily 2.4-GHz deployments. These wireless networks were designed before the widespread acceptance of 5-GHz chipsets. The low cost of the 2.4-GHz designs found in countless client devices make it the common denominator for existing Wi-Fi.
Many 2.4-GHz technologies can be found in operation in addition to Wi-Fi at industrial sites. For example, active Radio-frequency identification (RFID) in vehicle toll collection and vehicle fleet identification systems operate in the 2.4-GHz range. IEEE 802.15.4 includes ZigBee, a low-bandwidth wireless mesh used for monitoring applications, also operates in the ISM 2.4-GHz band. Many IEEE 802.11b/g access points are deployed for different industrial applications. This band also may be shared by enterprise and guest networks, as well as by industrial monitoring and control networks. IEEE 802.11 is a collection of wireless local area network standards. (See link in this article online.)
Many legacy industrial control networks that employed the IEEE 802.11b standard are particularly problematic. When these access points and clients transmit on channels shared with other higher speed networks such as IEEE 802.11n, they have the effect of slowing down everything sharing the channel. In fact, the performance of the high-speed network sharing the channel can be reduced to a crawl by just one client connecting frequently and transferring at 1 MB/sec.
To make matters worse, there are only three non-overlapping channels on a 2.4-GHz band. If one of these IEEE 802.11b networks is on an overlapping, adjacent channel, there will be significant performance issues caused by collisions on the overlapping channels. It also can be an enormous challenge fixing issues on existing deployments since the many networks are managed by different individuals or departments and can be difficult to coordinate. These are a few reasons why most wireless local area network (WLAN) professionals do not recommend 2.4-GHz for new deployments.
IEEE 802.11n: Equals more throughput and better productivity
The move away from the 2.4-GHz band has been going on for quite a while. It started with the adoption of the IEEE 802.11a standard, which was primarily used for industrial applications and saw low adoption in the commercial space. Now with the proliferation of IEEE 802.11n and the low cost of 5-GHz chipsets, the industry is seeing a significant move toward all 5-GHz technology for enterprise and industrial applications. Currently, the 5-GHz channels are relatively clean with little interference. The channels are planned such that there are no overlapping 20-MHz channels.
IEEE 802.11n improved throughput. Whereas IEEE 802.11a allows a maximum data rate of 54 Mbps, with IEEE 802.11n, one 20 MHz channel and single spatial stream can provide a data rate up to 72 Mbps. By itself, this is a modest improvement, but the standard doesn’t stop there. IEEE 802.11n also enables the use of multiple antennas (MIMO, which stands for multiple in, multiple out), transmit and receive chains, and the use of 40 MHz wide channels to allow up to 600 Mbps theoretical max, an impressive data-rate improvement. However, care must be taken to not overlap these wider channels, so planning is critical to avoid the same kind of issues that earlier 2.4-GHz deployments have faced.
IEEE 802.11ac: Gigabit
The next big wave in Wi-Fi is IEEE 802.11ac, which brings the promise of gigabit performance as well as other improvements. To take advantage of the technology sooner, the industry has been deploying the IEEE 802.11ac standard in phases. The deployment of the first "wave" or generation of IEEE 802.11ac-based technology was in 2014.
Unlike IEEE 802.11n, which supported 2.4 GHz and 5GHz, IEEE 802.11ac is 5 GHz only. It supports 20-MHZ and 40-MHz channels but also supports much higher data rates with an 80-MHz channel width. While allowing for much higher data rates, it also reduces available channels in the spectrum; channel planning must be done to avoid overlapping. IEEE 802.11ac also provides a higher density modulation technique, called QAM-256, to achieve its high performance. Because it requires a very high signal-to-noise ratio, the client must be very close to the access point to use this modulation scheme, especially in the presence of any interference or high-noise floor.
The next generation or "wave 2" is available this year and introduces 160-MHz channel width for even higher bandwidth and multi-user MIMO, or MU-MIMO, which allows several clients to be served at a time.
Industrial applications
The improved data throughput offered by new wireless standards is not always a key factor for adoption in the industrial space. In fact, IEEE 802.11n should continue to offer strong value for industrial users and has become the common denominator due to its fitness for industrial applications. For example, wireless often is used in industrial settings for monitoring or supervisory control and data acquisition (SCADA) applications. The amount of data sent from a client is relatively small and could be less than a few hundred bytes. This data also is polled at a low frequency. Support for block transfers at high speeds, which would be a benefit when transferring large files, essentially is irrelevant for these types of applications. The technology that has more relevance to industrial users would be the optimization of data transfer times over the channel, so that many more clients can be supported within a channel.
One feature of IEEE 802.11n that also has great relevance to industrial users is the ability to reconstruct signals in environments with a lot of multipath interference. In industrial environments, metal structures can create significant multipath interference. Since typical IEEE 802.11n-capable radios contain two antennae in a 2×2 configuration, they can support multiple spatial streams and signal reconstruction of multipath reflections.
Redundancy, loop protection
In addition to the basic technologies provided by chipset manufacturers, industrial applications sometimes require special features to ensure optimal and reliable performance for different applications. In rail applications, where train-to-wayside communication is required, system designers want more than one active wireless connection to the wayside for redundancy. This requires use of multiple radios and creates problematic network loops from the train to the ground. Therefore, a redundancy and loop prevention protocol must be used. Spanning tree protocols have been used in the past to address this, but they do not perform well in this environment due to the lossy nature of wireless (meaning it attenuates or dissipates) and the constant re-convergence that can occur during roaming.
Learn more about fast roaming technology and transportation connectivity.
Fast roaming technology
In many industrial applications, the client device is not stationary but is on a moving chassis. This is common in automatic guided vehicles (AGVs). A fast connection time is critical for an AGV, which must be able to roam seamlessly throughout a warehouse. These applications can be sensitive as the client moves and reconnects between access points. The typical latency of 2 to 5 seconds for a client to associate to a new access point often is enough to cause a connection timeout for the end application.
Systems designers look for technology to help them address this issue, and fast roaming technology has been developed to accomplish the task in milliseconds. Fast roaming technology can be found in WLAN controller architectures or in autonomous radios themselves. Fine tuning of thresholds may be required to optimize performance based on environmental conditions.
MAC address cloning
A common wireless application in manufacturing plants is connecting older technology on the plant floor-to-network infrastructure. Many manufacturing facilities have machines that do not have Ethernet or wireless expansion built-in. Companies still may have a significant investment in these computer numerical control (CNC) machines and are not so quick to replace them. For machines with Ethernet cards, a common technique is to add an Ethernet-to-Wi-Fi client radio.
However, this typically results in the media access control (MAC) address of the end device or machine not being passed through the wireless infrastructure and, instead, being replaced by the MAC address of the attached wireless radio. This can create issues for industrial users, since there are protocols that depend on the MAC address or layer 2 transparencies for proper operation.
Depending on the wireless infrastructure manufacturer and the presence of a WLAN controller, this can also cause an alert to be raised by the security features of the wireless controller, resulting in communication shutdown. The remedy is to use a feature called MAC cloning or MAC transparency. For wireless radios that support this feature, the radio will recognize the attached device on its LAN port on boot up and will clone its MAC address on the wireless network. This device plus the client can appear as one device on the network, and the layer 2 protocol will be able to work over the wireless bridge.
Transportation connectivity
In transportation applications, there can be many devices connected to a wireless client radio on the bus. Video cameras, recorders, and toll-collection devices are a few examples. In the past, each bus had to use unique IP addresses for every device to be managed by the control infrastructure. This is impractical as the number of buses scales up and more devices, such as cameras, are added.
A key feature of an industrial client is the ability to do network address translation or operate in client-router mode. This allows each bus to use the same local IP addressing information for local devices on the bus. These local addresses are not exposed to the wireless network. They are instead translated by the radio. This greatly simplifies the configuration, requires fewer unique IP addresses, is less prone to errors, and reduces the chances for duplicate IPs showing up on the network.
Another typical requirement for transportation applications is high-bandwidth wireless communication while in the bus yard to allow offload of captured video and toll collections. IEEE 802.11n is currently meeting this need, but IEEE 802.11ac is expected to become more prevalent for this in the future. As vehicles move about the yard, they also need to maintain a connection to the infrastructure as they move in and out of range of different access points. Some applications do not want to contend with the unlicensed bands and will, therefore, need private licensed band capability. The ability to support both licensed and unlicensed bands is a positive for radio manufacturers.
Since the majority of eBus applications are outdoors, access points must be able to operate in temperature extremes and be watertight, typically IP68-rated. The client radios on the bus must also be industrial since they are located in tightly packed compartments that are subject to high-temperature conditions. The constant motion also makes the units susceptible to damage from electrostatic discharge (ESD) and power transients, so surge protection on the power and antennas is often required.
Overall, developments in wireless technology for industrial applications go beyond the chipset innovations that are agreed upon by the industry standards organizations. While improvements to throughput are important, throughput is often not the primary consideration for industrial applications. Many applications place a much higher importance on the reliability of the wireless link rather than on throughput. Manufacturers will need to develop unique features to address the needs of these industrial users, and the process has been underway for some time. The good news is that radio technologies are now available to not only meet the latest industry standards, but also provide value-added features for specific industrial use cases.
– Mike Werning, Moxa Americas, field application engineer. Edited by Eric R. Eissler, editor-in-chief, Oil & Gas Engineering, [email protected].
Key concepts
- The improved data throughput offered by new wireless standards is not always a key factor for adoption in the industrial space.
- The next big wave in Wi-Fi is IEEE 802.11ac, which brings the promise of improved gigabit performance.
Consider this
Many applications place a much higher importance on the reliability of the wireless link rather than on throughput.
ONLINE extra
IEEE Std 802.11 for wireless local area networks (WLANS) as well as enhancements to the existing medium access control (MAC) and physical layer (PHY) functions
https://standards.ieee.org/findstds/standard/802.11-2012.html