System simulators allow developers to test most of a new control system, but not the entire system. See 6 tips for the factory acceptance test (FAT) phase of your project.
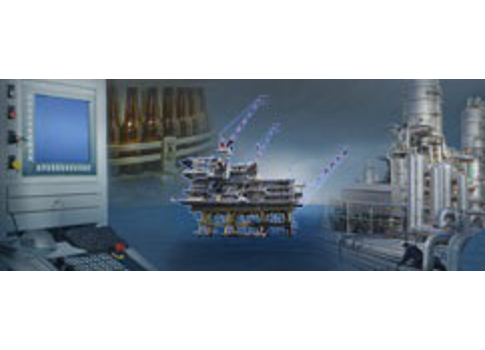
Virtual machines and control system simulation have been a great help in checking out systems during development. These have allowed the developer to be able to check out the control system code prior to installation. Most factory acceptance tests (FATs) are conducted using a simulated system or part of the real system that will be used for final installation. Over the past several years I have developed several new plant control systems using system simulators. Although this allows the developer to check out most of the system it does not check out the entire system.
I have heard several times during the site acceptance test (SAT) or commissioning phase of the project: “I thought the system was completely tested during the FAT.” One should remember that usually the instrumentation is not present during the FAT. Unless the testing team follows a rigorous test plan that includes checking signal ranges, controller loading, etc., the commissioning team may run into surprises during startup. Although issues that arise are not usually show stoppers, they do take time to resolve.
Here are six quick checks that can be done to make sure that you do not get surprised after the FAT is complete:
- Make sure to fully check that the configured instrumentation ranges match the actual instruments being used in the field. Most manufacturers will configure the ranges on smart devices at a small cost.
- For systems that use fieldbus protocols make sure that the addresses are set properly in the configuration and at the device. Also make sure the device actually supports the protocol you think it does.
- For discrete signals, verify the normal operation of the signals. Fail or normal position is not always what one thinks it is. This pertains to both inputs and outputs.
- Make sure the I/O card number and types match the actual I/O cards used in the system.
- Make sure you understand the voltage level of the signals being interfaced to the control system. I have seen people make assumptions that were wrong just to find this out during loop checks.
- Make sure that controller loading and system performance is not an issue. This is something you do not want to be surprised with during startup. Some simulation systems have the ability to check controller loading.
Although this does not include everything this should start people thinking about what was not done during the FAT checkout and what needs to be done before startup. I wonder if others have experiences to share that are similar to this?
This post was written by Jeff Wood. Jeff is a senior engineer at MAVERICK Technologies, a leading automation solutions provider offering industrial automation, strategic manufacturing, and enterprise integration services for the process industries. MAVERICK delivers expertise and consulting in a wide variety of areas including industrial automation controls, distributed control systems, manufacturing execution systems, operational strategy, business process optimization and more.