Centralized monitoring of process plants can be a critical enabler for operational excellence, but it requires easy access to contextualized data from automation systems.
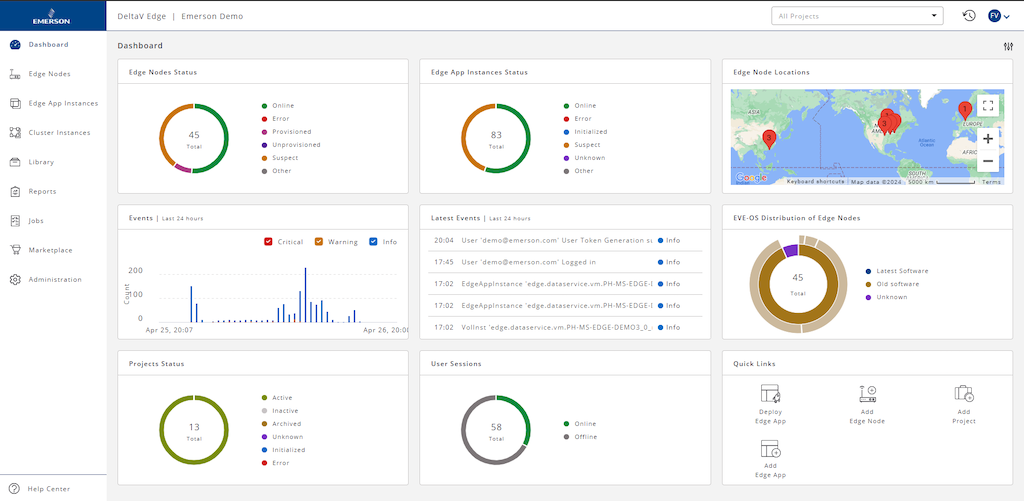
Learning Objectives
- Discover how centralized monitoring techniques can drive process manufacturers’ visibility.
- Learn the ways in which edge environments and a centralized portal are necessary for centralized monitoring.
- Determine how centralized engineers can be more proactive in applying best practices to maintain control systems across multiple plants.
Centralized monitoring insights
- Centralized monitoring is being used by organizations to increase visibility and standardize operations.
- Software-as-a-service (SaaS) is essential to centralized monitoring.
- Two key elements for centralized monitoring are built-for-purpose edge environments and a centralized portal for end-to-end lifecycle management of automation systems and software
As process manufacturing enters a new era of increasing competitiveness, achieving and maintaining operational excellence has become more important than ever. Today’s companies must distinguish themselves from the competition, and the best way to do so is to provide the highest-quality product, as reliably as possible, at the most reasonable price. But operational shortcomings quickly eat away at quality, speed and cost savings.
As a result, plants around the globe are focused on operating at peak efficiency to stay ahead. However, this has become increasingly challenging as companies face a two-pronged problem of increased personnel retirements coupled with a global shortage of experienced workers.
It is common for multiple plants across a fleet to have staff with a wide spectrum of experience and expertise, and that can lead to significant variability in operational performance, even across plants that are otherwise nearly identical. If every plant in the fleet operates differently than all the others, it can be difficult to optimize operations, and, by extension, challenging to achieve operational excellence.
Today’s management teams want to take what works best in engineering practices, operations procedures and maintenance tasks, and then replicate it across all the plants in their fleets. Uniformity leads to increased use of best practices and makes it easier to reduce waste and inefficiencies. To accomplish this uniformity, many organizations are exploring centralized monitoring and analytics to increase visibility and standardize operations. This shift, in turn, requires seamless data mobility.
Getting the right, contextualized data to a central location for use in enterprise tools or software-as-a-service (SaaS) solutions is the most essential step in centralizing monitoring. Fortunately, it is also one of the easiest to achieve with modern technology.
The challenge of accessing data
For decades, control systems have been built to keep out the external world due to cybersecurity and other tampering concerns. Basing infrastructure on the Purdue model for control system security, engineers have long segmented automation networks to effectively airgap the control system. While such an infrastructure provides some protection against external threats, it also turns the control system into a silo of critical data. If users want to get contextualized data out of the control system, they must navigate a lot of complexity.
Accordingly, some organizations have engineered complex solutions to help them move contextualized data up from the control layer. These plants typically send data to an enterprise historian or data lake, and they require a team to manually layer a logical hierarchy or framework over that historian data to rebuild lost context from the source. This type of solution is complex, time-consuming and error-prone. Not only does the team have to maintain a custom-engineered connection to move the data through firewalls to the enterprise historian, they also must manage the manual mapping. If the underlying conditions of operations change, so, too, must the mapping. Or, if IT solutions change, someone must manage the necessary changes in all related data pathways.
To navigate these challenges, forward-thinking organizations are implementing two key technologies: built-for-purpose edge environments, coupled with a centralized portal for end-to-end lifecycle management of automation systems and software. When used together, these solutions:
- simplify the transmission of data
- make it easy and seamless for teams to securely move contextualized data out of the control system and into their enterprise tools for better fleet management
Enterprise access via the edge
Edge environment solutions are central to the boundless automation vision of seamless data mobility from the intelligent field, through the edge, and into the cloud. Modern edge environments eliminate the need for complex custom engineering, allowing control system data to escape the layers of automation infrastructure. Secure, unidirectional communication transmits control system data — with all its associated context intact — directly to management and analytics applications at the edge, without any risk of external access to the control system (see Figure 1).
The most effective solutions use open standards — and protocols like Open Platform Communications Unified Architecture (OPC UA), Representational State Transfer Application Program Interface (REST API) and Message Querying Telemetry Transport (MQTT) — to ensure seamless, secure connectivity with centralized data management systems, analytics software, and other critical tools to provide deep operational insights. Because edge environments seamlessly integrate with the control system, cross-functional teams across the enterprise have continuous, real-time access to the data they need for innovation and insight, making it easier to see how individual operations measure up to each other and compare with benchmarks.
More efficient lifecycle management
In addition to edge environment solutions, many organizations are adopting centralized lifecycle management solutions for automation systems and software to further increase their visibility of operations and maintenance across their fleet. Using a fit-for-purpose performance management platform, organizations can see the software and hardware installed at every site from a centralized location. Management teams can quickly identify patch and lifecycle status of hardware and software deployed at each site, and compare performance in those areas against recommended baselines (Figure 2).
Armed with up-to-date system health status, centralized engineers can be more proactive in applying best practices to maintain control systems across multiple plants. Teams can identify their security posture, manage risk and enhance decision making surrounding software releases and evolving standards. Managing everything from one place reduces the number of expert personnel who must travel between locations to collect and compare data, freeing them to perform the work necessary to bring systems up to date.
Data-driven decisions are accessible
Making significant headway toward operational excellence requires organizations to effectively and honestly evaluate the ability of all their plants to promote best practices for operating and maintaining equipment, and for sustaining operating procedures around specific processes. Performing such analysis on a site-by-site basis is helpful, but truly transformational improvement comes from identifying opportunities and managing standards across the entire fleet — a task that can rarely be accomplished effectively without central monitoring across the enterprise. Modern technologies like edge environments and asset and software performance platforms make that task easier than ever, helping to level the playing field for organizations of any size by providing continuous, intuitive access to the data necessary to make decisions and innovate to secure competitive advantage.
Sean Saul is the vice president of the DeltaVâ„¢ platform at Emerson, where he is responsible for leading the overall product direction for the DeltaV Distributed Control System and Safety Instrumented System platforms.