Maintaining temperatures inside enclosures protects electrical and electronic equipment. However, equipment heating and cooling options have their pros and cons.
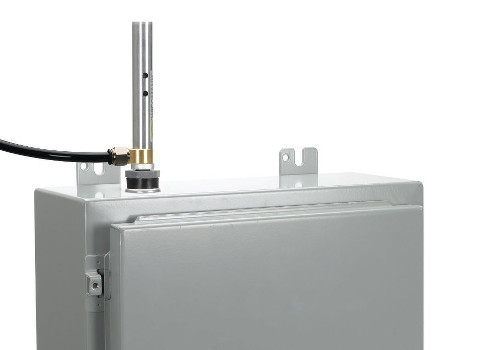
When automation system enclosures are installed in industrial facilities and plants, cooling and/or heating thermal management systems are often required. These systems protect the automation components installed therein from temperature extremes and moisture buildup. Consistent temperatures are required to ensure optimal operating conditions. Otherwise, cyclic broad temperature fluctuations may significantly reduce the life expectancy of electronic components.
Enclosure thermal management systems provide the required operating conditions through the use of heaters, fans, heat exchangers, air conditioners, vortex coolers, thermoelectric coolers, thermostats, hygrostats, and other components.
Enclosure heating
Enclosure heating systems are simple compared to their cooling counterparts. Enclosure heating is needed to protect components from moisture buildup caused by condensation, which may cause component failure due to changing contact resistances, flashovers, creepage currents, reduced insulation properties, and corrosion. While the greatest risk lies with equipment exposed to high humidity or extreme variations in temperature—as may be found in outdoor installations and poorly insulated enclosures—moisture buildup can also occur in highly protected and well-sealed enclosures under certain climatic conditions.
Enclosure heating systems usually consist of an electric heater installed at or near the bottom of the enclosure. Larger enclosures with heating requirements of more than 100 W may employ a heater with an integral fan to circulate the heat throughout the enclosure.
To prevent overheating of the electronic components, heaters are typically controlled by a normally closed thermostat or hygrostat. The control device may be integral to the heater or a separate device. Thermostats for heaters are available in fixed temperature (preset on/off temperatures) and adjustable temperature models.
While only some enclosures require heating, many more need cooling because the components housed therein often generate significant amounts of heat.
Problems with excessive heat
Excessive heat inside an enclosure can have many destructive consequences including:
- Decreased life expectancy of expensive control equipment, such as programmable logic controllers (PLCs), human-machine interfaces (HMIs), and ac drives
- Nuisance faults in electrical and electronic components, such as overloads tripping unexpectedly
- Erratic performance of circuit breakers and fuses, which can cause entire systems to shut down unexpectedly.
The same components that can be damaged by heat may also be the source of the heat. These components include, but aren’t limited to, power supplies, ac drives/inverters, transformers, communication devices, battery backup systems, soft starters, PLCs, and HMIs. The heat from these internal sources may be augmented by external heat sources, such as high ambient temperatures, solar heat gain, and external heat-producing equipment, such as nearby ovens and furnaces.
There are many options for enclosure cooling systems. Choosing the right one depends on a proper understanding of the enclosure protection requirements, the equipment inside the enclosure, and the surrounding environment. Fortunately, there are a number of options for dealing with internal and external heat sources.
Convection cooling
"Convection" is the term for heat transfer occurring between a moving fluid or gas (typically air in this article) and a solid surface where there is a temperature difference between the fluid and the surface. In everyday terms, convection is why it feels colder on windy days than when the air is calm.
Convection is complex to quantify, but there are a few basic principles to consider. These principles are intuitive; we know how convection feels. But they are worth mentioning because they help explain the relative merits of different cooling methods:
- Heat (thermal energy) always moves from the higher temperature material to the lower temperature material, such that the hotter material becomes cooler, and the colder material becomes warmer. Simply stated, this means you can’t cool something with hot air, and you can’t warm something with cold air.
- The heat transfer rate is proportional to the temperature differential between the two materials. If you are cooling something with air, using colder air will cool it faster.
- The heat transfer rate increases as the flow rate of the fluid across the surface of the solid increases. If you are cooling something with air, increasing the air flow rate will cool it faster.
The simplest method of enclosure cooling is by natural convection through the surface of the enclosure. Natural convection is the airflow created when warm air rises and is replaced by heavier cool air. Natural convection inside an enclosure occurs when the air around a heat source is warmed and expands, making it less dense than the surrounding air. This warmer air rises to the top of the enclosure and is replaced by cooler air.
This constant exchange of air around heat sources induces air flow within the enclosure that can be used to remove heat. Louvers can be added near the top of the enclosure to allow the hot air to escape, while grilles can be added near the bottom to allow cooler outside air to be drawn in.
However, natural convection has several limitations:
- The air flow rates induced by natural convection tend to be small, which limits the heat load that natural convection is capable of cooling.
- The maximum ambient temperature must be colder than the maximum allowable enclosure temperature.
- The enclosure protection rating must allow it to be open to the surrounding atmosphere without risk of component failure due to dust or water intrusion. This is often an issue as the louvers and grilles that allow natural convection can frequently permit airborne contaminants and/or spraying water to enter. Filters can be added to prevent dust intrusion where there are low concentrations of airborne dust, but using high density filters will impede air flow and reduce cooling capacity.
Because of these limitations, louvers and grilles are typically only effective for NEMA 1 enclosures with small heat loads located in climate-controlled spaces. These spaces must also be generally clean and dry.
If the heat loads are too high to be cooled by natural convection, forced convection can be used to cool the enclosure.
Fans improve convection cooling
Forced convection simply means that some type of air-moving device is used to increase the flow of air across the enclosure components to increase the cooling rate. The simplest forced convection system for an enclosure is a fan, which typically requires the use of a filter. Fans can produce much higher air flow rates than natural air convection and, in turn, produce a much greater cooling effect. But aside from higher air flow rates, fans have two of the same limitations as natural convection:
- The maximum ambient temperature must still be colder than the maximum allowable enclosure temperature. As with natural convection, the higher the temperature differential, the more effective the cooling.
- The enclosure protection rating must allow it to be open to the surrounding atmosphere without risk of component failure due to dust or water intrusion. As with natural convection, airborne contaminants and/or spraying water can enter the enclosure with the air drawn in by the fan. Filters are generally necessary to prevent dust intrusion. This is true-even where there are low concentrations of airborne dust-because the fan will draw the dust in at a higher rate than with natural convection. Using a fine-density filter will also allow the enclosure to maintain a higher NEMA rating than will a louver and grille system.
Fans with filters are typically used in NEMA 1, NEMA 2, or NEMA 12 enclosures located in climate-controlled spaces that are generally clean and dry. Because they consume minimal electrical power, filter/fan systems may be installed to run continuously without a control device. In some applications, a normally open thermostat may be required if the enclosure also employs a heater. This prevents the fan from working against the heater.
Heat exchangers maintain enclosure ratings
Air-to-air heat exchangers have the same general degree of cooling capacity as a fan and, like all convection cooling systems, can be used only where the maximum ambient temperature is less than the maximum enclosure temperature (see Figure 1). However, these heat exchangers create a closed-loop system in which the air inside the enclosure is cooled and circulated without exchange with ambient air, maintaining the enclosure’s NEMA rating.
Heat exchangers use a simple refrigeration cycle to cool the inside of the enclosure. An evaporator fan forces air heated by the enclosure components to pass across the evaporator end of the heat exchanger’s heat pipes. The heat transferred to the heat pipes causes the refrigerant inside the heat pipes to boil, producing a vapor. This refrigerant vapor rises through the heat pipe to the condenser end of the heat pipe where a condenser fan blows ambient air across the heat pipes.
The ambient air absorbs the heat from the heat pipe causing the refrigerant to cool and condense back into a liquid. The liquid then drains back to the evaporator end of the coils, and the cycle repeats. The evaporator and condenser sections are separated and sealed. The only thing that can pass between them is the refrigerant inside the heat pipes. Therefore, there is no transfer of air between the inside and outside of the enclosure.
Depending on its construction, a heat exchanger may be used with a NEMA 4, NEMA 4X, and/or NEMA 12 enclosure in an indoor or outdoor application, provided that the maximum ambient temperature is less than the maximum enclosure temperature. Like a fan, a heat exchanger may be installed with or without thermostatic control.
Air conditioning is highly efficient
So far we have limited ourselves to the discussion to convection cooling methods, but many times we require air colder than ambient, which adds another layer of complexity to the cooling system. Like heat exchangers, enclosure air conditioners create closed loop cooling, where the air inside the enclosure is cooled by an evaporator coil and circulated without mixing with outside air (see Figure 2).
The difference is that an air conditioner uses a more sophisticated refrigeration cycle employing a refrigerant compressor and an expansion valve. This creates lower refrigerant temperatures in the evaporator coil (for heat absorption from the enclosure air) and higher refrigerant temperatures in the condenser coil (for improved heat shedding to warmer ambient air temperatures).
Like a heat exchanger, an enclosure air conditioner may be used with a NEMA 4, NEMA 4X, or NEMA 12 enclosure in an indoor or outdoor application. Air conditioners have high cooling capacities and are generally very efficient. But like any air conditioner, they use chlorofluorocarbon refrigerants and require regular maintenance. They also tend to be fairly large due to the compressor, multiple fans, and refrigerant coils. Low-volume enclosures may not be large enough to install even the smallest available air conditioner.
Many enclosure air conditioners include an integral thermostat to control the operation of the air conditioner. An air conditioner without an integral thermostat should be installed with a normally open thermostat to prevent the unit from running continuously. Continuous operation would consume power unnecessarily, increase operating cost, and shorten service life.
Vortex coolers are compact
An alternative to an air conditioner is a vortex cooler (see Figure 3). These units take a filtered compressed air stream and spin it into a high-speed vortex, which splits the air into a hot air stream and a cold air stream. The cold air is fed into the enclosure to cool the internal components. The cold air also displaces the warm air inside the enclosure, which is exhausted with the warm air stream from the vortex cooler.
Enclosure vortex coolers are not closed-loop systems like heat exchangers and air conditioners because the air inside the enclosure is being replaced. However, because the enclosure air is being replaced by filtered compressed air rather than ambient air, an enclosure vortex cooler may be used with a NEMA 4, NEMA 4X, or NEMA 12 enclosure in an indoor or outdoor application, provided that an adequate source of clean, compressed air is available.
Enclosure vortex coolers have the added feature of creating positive pressure inside the enclosure, so dust and other airborne contaminants will not be drawn in when the door is opened. Vortex coolers are also much smaller than heat exchangers or air conditioners, which is an advantage when space is at a premium.
Vortex coolers have no moving parts, service life is very long, and they require little or no maintenance if the compressed air supply is clean. They contain no chlorofluorocarbons, further reducing maintenance. But vortex coolers are noisy, and larger models consume a high volume of compressed air.
Vortex coolers can run continuously without detrimental effects. However, to minimize the consumption of compressed air, thereby reducing operating cost, vortex coolers are typically controlled by the combination of a thermostat and a solenoid valve installed at the compressed air supply.
Thermoelectric coolers pump and remove heat
Another alternative to a conventional air conditioner is a thermoelectric cooler. Thermoelectric coolers are solid-state heat pumps that use a phenomenon called the "Peltier Effect," where a dc current is passed through two dissimilar semiconductors, causing one side to get cooler while the opposite side gets hotter. The cold side of a thermoelectric cooler is placed inside the enclosure, and the hot side is placed on the outside of the enclosure. Fans may be added to both sides to increase heat transfer.
Thermoelectric enclosure coolers are available for NEMA 4, NEMA 4X, and NEMA 12 enclosures. Like vortex coolers, they have no moving parts, so they require minimal maintenance and have a long service life. They also don’t use chlorofluorocarbons and are available in very small sizes for smaller enclosures.
But thermoelectric coolers are much less efficient in terms of performance than air conditioning systems, as they will typically use about four times the electrical power to produce the same cooling effect as an air conditioner. They are also limited with regard to how much heat can be removed per unit area of the cooler’s cold plate, so thermoelectric coolers with large cooling capacities can be very large. Thermoelectric coolers are typically controlled by thermostats to minimize power consumption.
Know your options
Enclosure heating options are very simple compared to enclosure cooling choices. However, heating is often not required. But many enclosures will require some type of cooling—from simple natural convection to more complex cooling systems.
Knowing your options-along with the benefits and limitations of each—will help you make the best choice for your particular application.
Jody T. Kinney, PE, is a product manager at AutomationDirect in Cumming, Ga., where he is responsible for market analysis and strategy, product selection, and supplier relations for electrical enclosures, enclosure thermal management products, and tools. He has a BS in mechanical engineering with high honors from the Georgia Institute of Technology. He has more than 26 years of experience in design, construction, manufacturing, laboratory analysis, forensic engineering, and product management.
This article appears in the Applied Automation supplement for Control Engineering and Plant Engineering.
– See other articles from the supplement below.