International Labor Organization said every 15 seconds approximately 160 workers have a work-related accident, and one of those injured workers will die. So, does it make sense to keep detailed records of injuries to claim that an absence of injuries equates to the presence of safety? Know the 5 progressive steps to a strong safety culture.
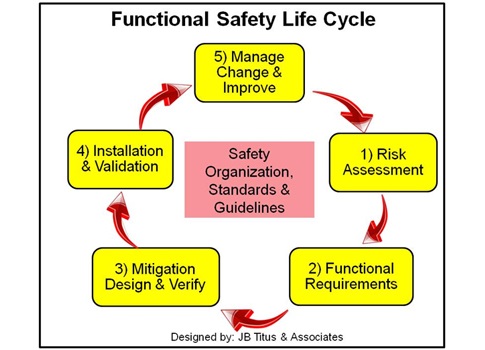
According to the International Labor Organization, every 15 seconds approximately 160 workers have a work-related accident, and one of those injured workers will die. So, does it make sense to keep detailed records of injuries to claim that an absence of injuries equates to the presence of safety?
5 progressive steps to a world class safety culture
It’s widely understood that many safety cultures within companies can and do advance to the “calculative” middle step. In total, the five progressive steps identified by professor Patrick Hudson are Pathological, Reactive, Calculative, Proactive, and Generative. Looking, briefly, at each step:
1. Pathological is the most basic level of safety cultures based largely on fear.
2. Reactive is where guarding systems often include engineered controls, administrative controls, and regulatory based controls.
3. Calculative is often represented by overall system wide controls and the application of technology based guarding measures.
4. Proactive, as the name suggests, is a bit more complex because this level introduces behavior and human and sociopolitical influences on behavior.
5. Generative is probably the most complex level delving more deeply into the cultural and sub-cultural influences on personnel behaviors.
Cross-organizational tools
In addition, there are several cross-organizational tools which can also be applied to help organizations improve their safety culture. Among these tools reports is the “Safety Maturity Index.” This on-line tool is designed to capture (as a benchmark) your existing performance in safety culture, your compliance processes and procedures and your capital investments in safety technologies. Analyzing these three pillars of a safety program allows companies to scale and optimize their existing safety program and to develop measures as necessary to improve both safety and profitability. These measures can then become the key steps for seeking best in class overall safety performance.
These examples are just two of many available today which can help companies advance their safety performance beyond the “calculative” stage. Remember this quote from Bill Hilton, director of health and safety at Georgia-Pacific: “A historical lack of accidents does not imply a current presence of safety. It simply means you’ve been faster than the machine.”
Engineering interaction: What transition from stage to stage offers the most challenge in your opinion? Do you have any questions about the 5 stages of safety culture? Add your comments or thoughts to the discussion by submitting your ideas, experiences, and challenges in the comments section below.
Related articles:
Risk and Safety Maturity Matrix from Riskex Pty Ltd.
World Statistics, International Labor Organization
Safety Maturity Index – more information from Control Engineering
Contact: www.jbtitus.com for “Solutions for Machine Safety.”