Safety considerations change as the source of hazards transforms, such as on moving workstations like automated guided vehicles (AGVs). Even Boeing’s 787 Dreamliner is assembled on slow moving AGVs. How can guarding for operator safety accommodate changing hazard levels during assembly?
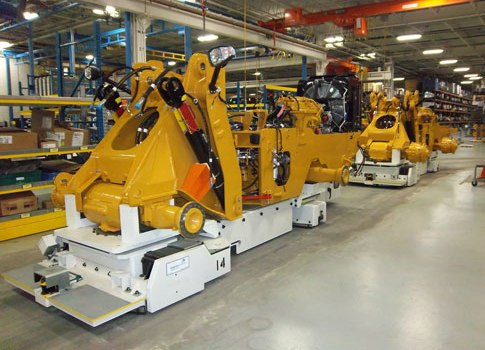
More applications of custom-designed automated guided vehicles (AGVs) have emerged over the past few years. AGVs are now capable of carrying large earth-moving vehicles through assembly processes. Even Boeing’s 787 Dreamliner is assembled on slow moving AGVs.
How can guarding for operator safety accommodate changing hazard levels during assembly?Newer AGV systems eliminate hazards like the usual in-ground pits or carriers pulled by chains. The older systems with these kinds of hazards caused many injuries because of trips, slips, and falls, which are always on OSHA’s Top 10 list year after year. But now, in many cases operators are actually on the AGV-style carrier performing their tasks. Sometimes the AGV carriers constantly proceed very slowly as in the Dreamliner. In another example, the AGV carrier may proceed very slowly and stop at predetermined workstations. In either case, the assembly configuration is ever-changing, and many hazard sources change as well.
AGV hazards
Some of these changing hazards in a moving AGV manufacturing line are:
1. The number of operators on a carrier performing tasks
2. Heights risking falls
3. Electrical shock due to power applied
4. Changing lighting conditions
5. Unexpected moving parts
6. Unexpected AGV movement
7. Add-on or removable operator platforms
8. Broken fluid lines
9. Stored energy.
As more moving AGV carrier-style working platforms are adopted for assembly, aren’t hazard analysis and risk assessment becoming more dynamic for these applications? I don’t think the safety standards need to wrestle with this situation with the abundance of safety application standards already available. However, it may be how the application standards are applied to a dynamically changing hazard. Some things that come to mind include: work procedures, operator training, lockout/tagout, warning signs, e-stops, safety networks, railings, safety harnesses, warning lights, horns, pull cables, personal protective equipment (PPE), work space lighting, and grounding.
The factory of the future will transform how operators accomplish their tasks. Don’t the related safety methods have to change as the source of hazards changes? For the past few years we’ve talked about risk assessments as being live "snapshots" that need to be updated with change (new automation, different product, tooling, etc.). Perhaps risk assessments in the factory of the future will morph symbolically to "movies" that require ever-changing safety methods for mitigation driven by progressive assembly.
What are your thoughts? Has this presented you with any new perspectives? Do you have some specific topic or interest that we could cover in future blog posts? Add your comments or thoughts to the discussion by submitting your ideas, experiences, and challenges in the comments section below.
See links at the bottom of this post for related articles:
• Automated guided vehicles integrate power, without batteries
• Machine Safety: Design a safer machine with risk assessments
• Machine Safety: Consequences of not performing risk assessments
• Machine Safety: Does a risk assessment need to be updated for a minor modification to a machine?
• Machine Guarding & The Hierarchy of Measures for Hazard Mitigation
Contact: https://www.jbtitus.com for “Solutions for Machine Safety.”