PC-based control systems provide many benefits and simplified solutions for industrial applications, including performance, decreased costs, and increased system lifecycle benefits. See five PC-based control myths and nine industrial PC benefits.
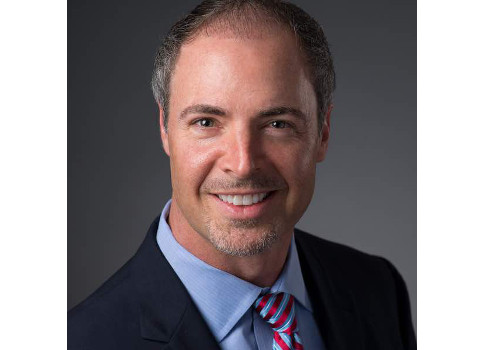
Industrial PC-based control systems increase connectivity capabilities for industrial applications while providing powerful, flexible, and cost-effective control. Understand the myths and benefits to help with control system specification.
PC-based control system misconceptions:
Many misconceptions are often attributed to PC-based control systems. Dispelling misconceptions can help with the implementation of and the benefits from PC-based control systems. Test your knowledge of PC-based control with the following five myths of industrial PCs:
Industrial PCs (IPCs) are not real-time because they rely on the clock speed of the PC.
FALSE: Most PC-based control platforms today use a real-time kernel running under the Microsoft Windows user mode. Windows starts the real-time kernel during start-up, and, once initialized, the kernel does not rely on Windows to function, although there is communication between the kernel and Windows.
Industrial PC-based systems are not as fast as a programmable logic controller (PLC).
FALSE: Typically, PC-based control systems leverage the newest and fastest processors; this ensures that the systems feature industry-leading performance while maintaining the lowest possible cost in all areas, including total cost of ownership, hardware, software, and networking. For instance, a system is capable of 50 microsecond (µs) PLC scan rates synchronous with a 50 µs network scan, while also capable of performing control in between the scan down to 1µs, all with accuracy in the nanosecond range. In addition, this can be accomplished with almost zero jitter, which is essential to the accuracy and determinism of the PLC and network cyclic updates. Highly accurate and deterministic cyclic updates enable increased accuracy for coordinated motion control and data samples at precise time intervals. PLCs typically offer scan rates in milliseconds, as opposed to the microsecond level.
Industrial PCs are not deterministic.
FALSE: A PC-based control system runs PLC scans in software with high determinism. When a task (such as PLC code execution) is scheduled to run, the system latency (also known as jitter) is quite low, coming in at less than 5 µs. Using the distributed clock technology available with the Ethernet for Control Automation Technology (EtherCAT) fieldbus, the accuracy of synchronizing fieldbus data runs in the nanosecond range.
Many PLCs on the market today, including some from the largest automation suppliers, do not run deterministic scans at all. Instead, these devices conduct back-to-back code execution cycles and, depending on the logic and execution sequence of the code, each scan’s execution time is different for varied PLC program execution times.
One scan might finish in 800 µs, and the next scan could take several milliseconds. There is no way to repeatedly capture an input that might only stay on for 1 µs without special I/O hardware. In addition, with varying program execution times, it becomes extremely difficult to synchronize motion control in a traditional PLC architecture. This is why many vendors implement an additional central processing unit (CPU), either on the same hardware or in a rack-based add-on module, to independently control the motion-control loops.
The added CPU and associated hardware increase costs, as well as increase required hardware, points of failure, and space. Larger, more expensive electrical cabinets are often required, and the machine footprint increases accordingly. PC-based solutions feature a high level of determinism that enables these systems to combine synchronized motion control with the PLC and other tasks, all on one centralized processor.
Industrial PCs don’t offer the same level of security as PLCs.
FALSE: According to reports, several of the largest, global PLC manufacturers have experienced hacks into PLCs through the software’s “back door.” PLC manufacturers bear responsibility for protecting this aspect of customer systems. With a PC-based control system, common and accepted approaches can protect the system and protect many third-party software packages that provide key components for comprehensive security solutions.
Hardware PLC manufacturers continually attempt to add further communication openness that is available with industrial PC-based control systems. Companies seeking to add those protocols and make the hardware PLC more open, while at the same time indicating that the openness of PC-based control is a security risk, are effectively taking both sides of the argument.
PC-based control manufacturers’ participation in leading organizations, such as the OPC Foundation, helps facilitate the development of new standard protocols for encrypted, secure data communication between the machine controller and the enterprise, as well as with cloud-based systems. The sum of these efforts has been the creation of the OPC standard, OPC Unified Architecture (UA), as well as standardization of PLC function blocks for OPC UA communications.
Companies are moving more towards distributed control over centralized control, and there is more risk in centralized control if the controller fails.
FALSE: Due to hardware PLCs’ performance limitations, there is heightened interest in distributed control as a way to meet the growing demands of new technology implementations for machines on the plant floor. In addition, smarter sensors create a need for protocols that can deal with the parameters available in the sensor, as these receive updates via on-board web servers. Ideally, all parameters for drives, sensors, and other devices across the system can be stored in one central location, so when connecting remotely these can be viewed and updated easily.
Decentralized control also has its place in automation solutions; however, this is not an argument for or against PC-based control. Manufacturers offer both centralized and decentralized control solutions. While the applications are few and far between, there are modular machines that can benefit from a distributed control strategy. If an application would benefit from distributed controls, manufacturers can employ EtherCAT automation protocol (EAP) for communication among many controllers. EAP is an open protocol managed by the EtherCAT Technology Group (ETG), www.ethercat.org providing fast communication using routable transmission control protocol (TCP) communication frames. The data proceeds directly from the real-time kernel and implements a “publish” and “subscribe” model to exchange data between controllers. This is also referred to as “master to master” communications.
To say that risk increases in the event of a failure when human-machine interface (HMI), PLC, motion, and other technologies are combined on a central controller is a misguided notion when the majority of machines cannot operate if any one of these critical functions is eliminated. Perpetuating this misconception simply adds unnecessary costs, complexity, and reduces the lifecycle of the system due to excessive hardware.
Learn more about the nine benefits of PC-based control systems.
Benefits of PC-based control systems
PC-based control architectures offer control strategy benefits.
1. Performance
PC-based control systems can quickly integrate faster, more powerful processors, offering higher performance over a hardware PLC. Most PLC vendors use CPU technology that is vastly slower than today’s common PC CPU. One principle is referred to as core isolation where specific functions in the automation controller are assigned to specific cores in the multicore CPU. High-performance PC CPUs have an outstanding price-to-performance ratio when compared to other CPU architectures or chipsets due to the economies of scale.
2. Reduction of hardware yields and costs
Most machines benefit from a centralized control approach, which makes PC-based control systems an ideal solution; although there are instances where decentralized control is advantageous. Generally, it is most advantageous to access all software and data from one central location and utilize one central communication method for all devices on the control system.
Traditional machine architecture approaches involve a PLC, a motion controller, and a PC for HMI and data collection. As stated previously, many vendors choose to integrate a secondary CPU for motion control in the main PLC body, or connect via a rack module, rather than a standalone box. No matter where the CPUs are located, the system involves three processors. While the machine typically already includes a PC with a processor capable of running the HMI and data collection, this approach also adds extra clock cycles for real-time PLC control and motion control. By combining these technologies into one powerful CPU, using a real-time kernel for deterministic control, unnecessary CPUs, and hardware is eliminated, and costs are reduced. This vastly simplifies the control system and improves uptime-a result of improved diagnostics obtained by keeping everything in central location. In a world where energy resources are becoming scarce and companies seek to reduce their ecological footprint, a centralized approach is the most logical solution.
3. Increased system lifecycle
When a PLC becomes obsolete the software also may require upgrading. In a PC-based control system, the end of a processor’s lifecycle does not mean the system architecture or software becomes obsolete. By incorporating more functionality into the software and running that on a standard IPC, customers can simply replace the aging IPC with a new one without any change to the balance of the control system, including the software. Automation programs and fieldbus configurations simply download to a software system on the new IPC, with no need for code changes. In the consumer PC market, new processors with increased performance are continually released at lower price points.
This cycle of price-to-performance ratio applies also to IPCs and PC-based control architectures. The technological development of hardware PLCs cannot react as quickly and continues to fall behind in terms of performance and lifecycle. Often, next generation PLCs enter the market with considerably higher costs and complexity when upgrading.
4. Flexibility
PC-based control systems offer maximum flexibility compared to a hardware PLC. A significant number of processors are available on the market, giving companies a choice of the best possible components for the job. With the release of Microsoft Windows 10, one operating system will be able to scale up to the highest performance multicore processors, cover the most widely used multicore processors, and even scale down to the lowest end microprocessors in the field.
Manufacturers offer many families of IPCs and embedded PCs-with a wide range of processors and housing types, enabling customers to flexibly select the processor and PC type that best suits the requirements for the application. The same I/Os can be used, whether directly connected to an embedded PC, similar to a PLC, or connected via a standard CAT5 cable out to a remote I/O rack.
5. Openness—standard, open protocols and third-party software support
Every manufacturer in the competitive global market today must analyze data from the plant floor to quickly produce high quality and accomplish this in the most efficient, cost-effective manner. Machines must offer open methods for collecting the necessary data and sharing it with the enterprise for further analysis. It is becoming increasingly important for companies to act on the results of the analysis and control the machines from the enterprise level, if needed.
The growing need for this functionality brings Industrie 4.0 and cloud computing, as well as the Internet of Things (IoT), to the forefront in the discussion of the next Industrial Revolution. To facilitate these new functions, companies need high-end computing and analysis tools that operate across their facilities and throughout the global enterprise.
PC-based control systems have been prepared for this next Industrial Revolution for years while PLCs may offer fewer open protocols and less connectivity necessary for this next phase in manufacturing. For example, communication via OPC UA across Ethernet provides an encrypted method of sharing data bi-directionally between the machine and the enterprise.
Due to the limited implementation of communications protocols in most traditional PLCs, connecting the controller to the enterprise or cloud involves separate hardware gateways or middleware to translate the data into a higher level protocol just to integrate the data into enterprise systems. This adds a significant cost to simply gather data from existing controllers. For PC-based control systems, most of the needed protocols are already available or can be easily added to the controller with available protocol software development kits. Additionally, devices that use standard Ethernet, USB, and other standard PC protocols are being deployed on the plant floor in increasing numbers.
The EtherCAT industrial Ethernet protocol provides advantages by eliminating proprietary rack backplane protocols. That said, the combination of a software system and EtherCAT offers communication capabilities to many other protocols, such as EtherNet/IP, Profinet, Profibus, DeviceNet, CANopen, Sercos interface, Interbus, Modbus RTU, Modbus TCP, and standard serial and Ethernet communication. This ensures the ability, if necessary, to migrate to new control technologies in multiple steps, at various speeds.
This system openness and availability to connect with almost 30 fieldbuses allows users to choose the appropriate sensor or device for the application without the possibility of communications problems when integrating with the main machine controller.
6. Leverage the most common programming languages and tools
A PC-based control system can use any third-party PC software, needing only the ability to run on the central controller alongside the HMI, PLC, and motion control software. Using any of the IEC 61131-3 programming languages is possible, including object-oriented programming extensions. When the two worlds of programming are combined, IEC 61131-3 and Microsoft Visual Studio, they provide the most open and universally accepted environment for programming globally. In terms of real-time, it is also possible to run C/C++ in addition to the IEC programming languages in the same software system, real-time kernel.
7. Improved diagnostics
A centralized, PC-based control solution offers one connection point for diagnostic data, making it easy to quickly troubleshoot problems and improve machine uptime. PC-based control solutions inherently enable remote connectivity, for example, through the use of standard tools such as remote desktop or even automatic sending of predictive maintenance and alarm data at the enterprise level or cloud for a quick review and remedy.
IPCs incorporate a helpful Web page to view IPC diagnostics, such as temperature, fan speed (if applicable), and storage capacity, among others. This IPC diagnostic data also can be accessed via OPC UA, as well as in the PLC project. Furthermore, the use of the built-in scope tool in the software and other standard diagnostic features can be accomplished remotely or locally, as the engineering environment can be loaded on the IPC with the kernel mode run-time.
EtherCAT communication adds diagnostic capabilities when implemented as part of a PC-based control system, particularly given that EtherCAT can serve as the sole communication protocol across a machine or plant. In a PC-based control system, EtherCAT also enables rack backplane communication to individual I/Os on the local and remote I/O racks. This provides diagnostics to the rack level and to the individual I/O level. As such, the central IPC can access a wide array of highly precise information, such as the exact location of a communication break to an I/O terminal in the middle of an I/O rack.
8. Protection of engineering investments and intellectual property (IP)
For PC-based control systems, programmers can develop code for their machine that can easily port to another IPC. There is always an abstraction between the PC hardware and the software, so the use of standard programming languages makes this code even more portable. Conversely, in a PLC environment, code is typically developed for proprietary hardware. When the hardware becomes obsolete, the software may not seamlessly transfer to the next-generation hardware. As a result, the user’s code and the engineering time spent for development may be lost. Developers are then faced with the prospect of backwards engineering to rebuild the lost code in the software environment that is needed for the new proprietary PLC hardware.
High levels of encryption technology easily integrate with PC-based control systems. This permits a high level of encryption, not only of source code files, but also compiled run-time files. Digital signing technology further protects code from being copied, stolen, or blindly moved from controller to controller without OEM control. PC-based control systems can use different levels of security within the software, but OEMs can employ further strategies as described to protect their IP addresses.
9. Larger pool of resources
PC-based solutions offer access to the most programming languages and tools, ensuring that manufacturers and machine builders have the widest possible pool of skilled programmers available. This provides competitive advantages today and into the future as the percentages of available PLC and PC programmers continue to skew in favor of computer sciences and IT.
As corporations pursue new and innovative ways to remain competitive in the global marketplace, it’s critical to focus on data collection across the enterprise without complex infrastructure and additional hardware, advantages that PC-based control systems provide. The importance of making the smartest possible decisions with this critical data, almost in real-time, provides a compelling argument for the increased predominance of forward-compatible, PC-based control and automation technologies. Machinery manufacturers must deliver systems that keep the door open for future enterprise connectivity improvements, while at the same time providing powerful, yet cost-effective solutions for the needs of today.
Doug Schuchart is a regional sales manager at Beckhoff Automation LLC. Edited by Emily Guenther, associate content manager, CFE Media, Control Engineering, [email protected].
MORE ADVICE
Key Concepts
- PC-based control systems are more compatible with advanced technologies.
- PC-based control systems allow for high levels of encryption technology, increasing security levels.
- Upgrades or changes are a more simple process with PC-based control systems in comparison to PLCs.
Consider this
Will PC-based control systems become more of a requirement as more advanced technologies are used for industrial applications?
ONLINE extraÂ
See Control Engineering pages on PC-based control and cybersecurity.
See related topics from Beckhoff Automation. https://www.beckhoffautomation.com/