Traditional flow measurement technique survives and thrives, often updated with current technology.
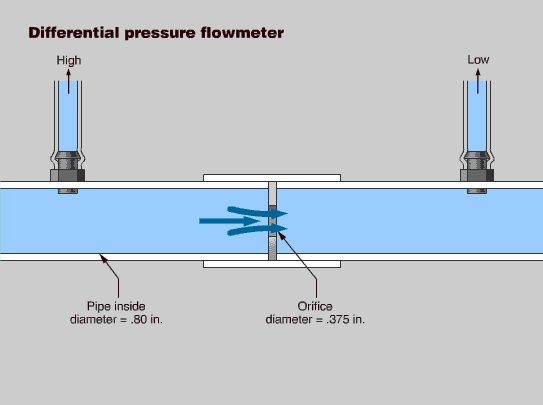
When a flow measurement technique that has been around since the automation dark ages continues to show among the top performing technologies, it indicates a high level of reliability, versatility, and adaptability. Such is the case with differential pressure flowmeters. As a flow metering technique, it consistently ranks among the top five.
This is really a very large family of designs that separates into two main categories: flow obstructions and Pitot tubes. For purposes of this discussion, we’ll consider only the former. When an obstruction is placed in a pipe, there will be a difference in fluid pressure upstream and downstream from the obstruction. This difference can be measured and characterized to provide the basis for calculating flow. (An electrical parallel is calculating amperage by measuring the voltage drop across a known resistance.) While it may not be the first flow measuring technique invented, it is certainly one of the earliest, and quickly followed the first practical pressure gages.
Understanding the concepts of a magnetic or Coriolis flowmeter may stretch your thinking but differential pressure flow measurement mechanics are easy to grasp (although the actual equations can get pretty complicated). This familiarity, combined with its simplicity, helps the technology survive. The most basic implementation involves placing a disk or other type of orifice in a pipe with an opening smaller than the pipe’s inner diameter, and then taking a differential pressure measurement comparing the up- and down-stream sides of the orifice. There are many practical advantages to this approach:
• The technology is simple and easy to understand;
• There are no moving parts;
• The sensor is very compact;
• Works equally well for gas or liquid;
• Can be configured to measure bi-directional flow;
• Usable over a very wide range of sizes;
• Devices can be mechanical or electronic;
• Relatively inexpensive; and,
• You can even build one yourself. (Watch a video demonstration.)
Since this approach uses a pressure sensor, suppliers have included all the technological advances of those product families as part of the package. There are some very sophisticated units available, and those improvements carry over to the flowmeter application. These can provide diagnostic information and multiple variables.
On the other hand, there are some drawbacks:
• It’s not the most accurate flow measurement technology. If high precision or wide turn-down ability is a key objective, there are better choices.
• Devices cause a pressure drop and reduce the pipe’s free passage. The extent of this depends on the design.
• Accuracy and turn-down are related to pressure drop. The more accuracy and range you need, the greater pressure drop you will have to tolerate.
• While there are no moving parts, the orifice itself is often a wear-prone point. If it gradually enlarges, the flow measurement will read proportionally lower. On the other hand, if it becomes partly obstructed with debris, the measurement will read higher.
• The same application and installation guidelines for pressure sensors apply here. Anything that interferes with the pressure readings (clogged impulse lines, etc.) will interfere with a true flow calculation.
• Changes in liquid characteristics (viscosity, multiphase flow, etc.) can affect readings. This varies by design.
• These are generalities, so discuss your specific application needs with any prospective suppliers.
Differential pressure flowmeters are available from a variety of suppliers. A search on “differential pressure flowmeter” at www.controleng.com turned up more than 350 results.
Peter Welander, [email protected]