Baby boomers from manufacturing automation industries are taking knowledge gathered through years of experience into retirement. Scrambling to find qualified workers to fill that void has begun. System integration and related technologies are helping.
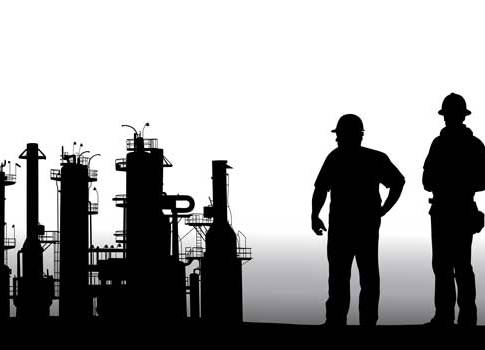
When Bruce Gibbens walks through one of his client’s tomato processing plants, he knows things are running right just by listening to the hum of the machinery. The process tells all.
"By the noise you hear in the plant, you can tell if the plant is speeding up or slowing down," said Gibbens, president of the Temecula, Calif.-based Tactical Controls LLC.
"As an integrator," Gibbens said, "I can feel the pulse of the plant just by being there. I don’t have the knowledge of whether that is a good sound or a bad sound. The guys that work there all the time, they can say, ‘We are going too fast; we have got to slow the process down.’"
What Gibbens knows—and what the rest of the industry is trying to come to grips with—is that the knowledge gathered through years of experience by veteran baby boomers is leaving the manufacturing automation industries; people are scrambling to find qualified workers to fill that void.
The unknown part is with a scarcity of engineers to fill the openings throughout the industry, and with manufacturing driving the U.S. and global economic recovery, just who and what will fill that expertise walking out the door?
That gap is where systems integrators will be able to provide human and technical knowledge to a manufacturing enterprise.
"A lot of [boomers] are going to be leaving," Gibbens said. "It can go two ways. The people that are going to take over are going to be less knowledgeable and have less experience-and they may have to lean on external resources more than relying on the people that are leaving. They may have to reach out to systems integrators and seek advice for their control system and outdated control systems for upgrades and the knowledge for helping them in what they need in their plan. Or, a lot of these plants are trying to be lean and mean, and they may try to do some of that stuff in-house."
Engineering shortage
President Grover Cleveland instituted Labor Day as a federal holiday in 1894. Back then, the need for skilled manufacturing workers in America was on an upswing. While the manufacturing sector has changed considerably, one thing is certain: there is a skills shortage that needs filling today, according to a survey of industry senior executives commissioned by Advanced Technology Services, Inc. (ATS) and conducted by The Nielsen Company. Among the top findings of the survey of 100 vice president and C-level executives:
- 55% of the largest U.S. manufacturers polled (those with $1 billion or more in revenue) will be the hardest hit by the skills shortage-costing each $100 million or more over the next 5 years.
- 45% of the companies surveyed are encouraging their older workers to stay on the job.
- 50% of respondents said they currently have 11 or more open positions for skilled workers, with 31% having over 20 open slots.
Another report released by the National Research Council urges new partnerships to tackle the problem of retiring boomers. They include a retooling of higher education to produce more young people competent in science, technology, engineering, and math (STEM).
The report said there was a "bright present and future" for energy and mining jobs, with continuing demand for workers and good pay for those hired. But it also said some industries already face labor shortages-and others soon will-because the nation’s colleges and universities aren’t cranking out graduates with the skills needed by growing companies.
The electric power industry alone will have to replace nearly 100,000 skilled workers (more than 25,000 of them in the nuclear industry) by 2015.
Federal Mine Safety and Health Administration data show 46% of the workforce will be eligible to retire within 5 years, but there are too few younger workers in the pipeline to replace them.
Meanwhile, the oil and gas industry has a workforce that’s currently concentrated at the older and younger ends of the spectrum. The National Research Council report said this creates "a gap in experience and maturity," making it difficult to replace retiring leadership.
While 47% of respondents in the ATS/Nielsen survey said they would like to fill their open slots with full-time workers, 53% said they are more likely to outsource the positions.
The report recommends several wide-ranging solutions, including outreach efforts to improve the public’s understanding and perception of energy-producing industries like oil and gas.
If the stars align, those solutions may work in future years, but what about now? What happens in the next year or so, when the boomers decide to cash in? A manufacturing plant can’t wait for a marketing campaign that will entice college-age students to become engineers and join the company in 4 or 5 years.
This is truly where systems integrators plying their skills with automation technology will help fill that skills gap to provide a productive, safe, and secure environment for manufacturers.
Documenting tacit knowledge
"A lot of what we do is talk to senior management people and document everything they know: documenting the processes, documenting the information they use, going out and finding the trends for things that they have done, and understanding why they made the decisions they made," said Emmett Moore, product manager at the systems integrator Cimation in Houston, Texas.
"With that type of knowledge-and us in the field working with these guys-we have learned the experience, but we are trying to use more of an analytical and engineering approach to really find out why these guys have done the things they have done. Why does an operator at a control station push this button at a certain time? Let’s build that into the product itself."
That all means systems and tools will need to be more intelligent. It also means technology will take a higher share of the workload so the new generation coming in dealing with the new manufacturing paradigm will feel more at ease with proper training.
Having software-driven systems in place that already have the intelligence to measure and assess the situation and take corrective actions automatically will ease the generational shift. But this change doesn’t happen automatically. Companies need to recognize it and understand it is an opportunity to allow for change.
"If vendors and systems integrators are doing their jobs right, then we are building solutions that can let people know when something is running normally; or, if there is an abnormal condition, what is the reason for the abnormal condition?" said Tony Paine, president and CEO at communications software developer Kepware Technologies.
"There is the younger generation coming into the workforce," Paine said, "and they don’t know everything that someone with 30 to 40 years of experience knows. What we can do is make their life easier through diagnostic tools, asset management tools, and condition-based monitoring tools. If we can create our magic such that we can team up with other companies or team up with systems integrators to put their touch on it, that problem goes away."
Plant evolution
From pneumatics and boards to PLCs, tablets, and smart devices, technology has changed the concept of how plants and people work.
Take a midstream gas plant that came on line 40 years ago. That plant developed over 40 years of data and the people working with those assets are leaving, Moore said.
"We are not losing everything," Moore explained. "We are losing the people that have worked on it from the beginning. So, instead of working with pneumatic controls [from 40 years ago], you have electronic controls and you have RTU modules and you have all the instrumentation that is collecting information. When you start analyzing it, we get more information out of these facilities than they ever knew existed. We view advanced process control as something an operator could never do by himself when he could turn valves by push button. Even when we started to give him the base control of automation, he still didn’t have the power that we do today with advanced algorithms in these plants. Moving heavier on the automation side means we can more efficiently control a facility by automating it, which means you don’t break it as often and it runs more efficiently. In things like that, you can quantify exactly what you got out of the situation. Yes, knowledge is leaving, but we have already collected it and built it into the process."
That is only part of it. As manufacturers rely more on automation and try to get along with fewer engineers, they will need more robust tools to be able to communicate with the disparate systems and protocols throughout the manufacturing enterprise.
"In the past 10 to 15 years, it was really hard to get an [Rockwell Automation] Allen-Bradley control system to talk to a Siemens control system and vice versa," Gibbens said. "Because you have the different manufacturers out there, you will need the systems to be able to communicate to one another."
That means to be able to automate to a higher level, get the most out of the system, and create more products, it will become more important to have software that allows systems to communicate to a higher degree.
"You have associations like the OPC Foundation pushing for information to share between devices or between devices and software applications," Paine said. "We have the de facto standard that everybody should implement and buy into so everybody can play with no configuration and automatically discover what is available from another data source. That will give more context to that data."
"Allowing ways to go ahead and be able to talk from different software and hardware platforms-and be able to connect them-is going to become bigger and bigger," Gibbens said. "OPC is the layer that will bring a lot of these systems together. As systems go along and you need to communicate between various things, there will be more use of that interoperable software in the future."
Automation means security
Connecting systems does create potential for a cyber security incident, however.
"Security has come to the forefront of everybody’s mind because businesses are demanding access to data at any time from anywhere," Paine said. "Anything that can have an influence on the control system, they want to monitor. So when you start thinking about mobile, big data, and the Internet of Things, you are starting to get the market to realize there has to be a shift in how we expose our control systems."
When the boomers first came on the job 30 to 40 years ago, no one had to worry about cyber security. The manufacturing floor was its own island.
"A few years ago, people adopted automation and a few of those that were more daring and adventurous started to deploying it into their environments before they knew everything-before the Internet of things even existed," Moore said. "So you have all these facilities out there that are automated and on the Internet. Now we are starting to see trends where people are saying, ‘I can attack that’ because it is on the Internet. The industry is now trying to figure out a solution on how to protect itself without degrading its investment in automation and degrading all the information they are getting from places like well pads they never had before."
That is where automation is coming together through integrators, who put end users and suppliers on the same technology page.
"We are doing vulnerability research on products that are already out there," Moore said. "We are testing these products and working with vendors to patch the vulnerabilities as soon as possible. Once we find a vulnerability, we are working with clients to create mitigation techniques that allow us to protect them until a patch comes out."
In a sense, it could be an easier and more secure transition with the new generation coming on board.
"The younger generation is basically used to the consumer technology that is available today. It is plug and play. It just works," Paine said. "There is going to be an expectation: if I have components that have physical connectors that look like they should match and they can hook together, then they better darn well work behind the scenes with little to no configuration."
Like it or not, that means there is a new playbook coming for manufacturers that requires a more intense and robust form of automation. So, maybe the days of walking through a tomato processing plant and knowing the "right" sound will not be necessary.
"What it really comes down to is you can really have those sounds and you can say something is up, but sometimes it doesn’t point you in the right direction," Moore said. "A lot of times, there is a root cause which wasn’t addressed with that sound. We are taking a more proactive approach to predictive analytics, predictive maintenance, and preventive maintenance rather than a reactive maintenance-which is what the older generation mentality was saying when they heard something going wrong and said ‘Let’s go out and fix it.’ Now, we want to find it out and put sensors in the instrumentation and sensors in the plant that can tell you, ‘Hey, the pressure is rising in the pipeline and while it is not going to cause damage today, it is going to cause damage two years from now.’"
The process tells all.
– Gregory Hale is the editor and founder of Industrial Safety and Security Source (ISSSource.com). Edited by Mark T. Hoske, content manager, CFE Media, Control Engineering, [email protected].
Key concepts
- Skilled workers are leaving faster than new engineers are arriving.
- System integrators can help fill the skills gap.
- Automation tools can help capture knowledge in automation and control systems.
Consider this
Upgrading automation and controls prior to baby boomer experts leaving will help capture valuable knowledge before they go.
ONLINE extra
Control Engineering Information Integration Study at www.controleng.com/ce-research
Information Integration newsletter at www.controleng.com/enewsletters
See below for related links including career and salary advice.