Selecting a controller for an industrial application can be increasingly difficult with all the options available. These 11 selection criteria can help when deciding among relays, timers, analog instruments, smart relays, programmable logic controllers (PLCs), and programmable automation controllers (PACs). See controller selection table.
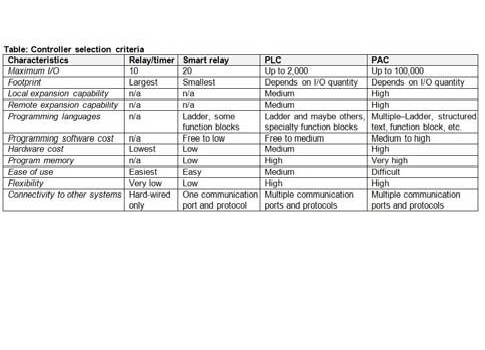
Basic choices and selection criteria follow to help in specifying a controller for an industrial application. Eleven criteria in the table can help when selecting a controller type from among relays, timers, analog instruments, smart relays, programmable logic controller (PLCs), and programmable automation controllers (PACs).
Relays, timers, and analog instruments: Despite the proliferation of inexpensive smart relays and micro PLCs, many thousands of control systems are built each year using these basic components. The big advantage of these systems is simplicity, as even the dullest technician can understand and troubleshoot them. No programming is required; thus there is no need for software licenses or PCs. When the number of relays and timers exceeds four, it’s best to upgrade to a smart relay.
Smart relays: These have grown more capable over the years, blurring the line between them and micro PLCs. Smart relays can be programmed with PC-based software, but many can also be programmed from their front panel display. Ladder logic or function block is the language of choice, and analog capabilities range from slim to none.
PLCs: These workhorses run the range from micros with about 32 built-in input/output (I/O) points to full-featured systems capable of handling thousands of I/O. PLCs are programmed with PC-based software, and any changes to the program require a PC. But, many parameters can be adjusted with a local operator interface, which is built-in with a combination of PLC and human machine interface (HMI) units, an emerging class of controllers combining a PLC with a graphical interface (Table 1).
Table 1: Controller selection criteria
Characteristics | Relay/timer | Smart relay | PLC | PAC |
---|---|---|---|---|
Maximum I/O | 10 | 20 | Up to 2,000 | Up to 100,000 |
Footprint | Largest | Smallest | Depends on I/O quantity | Depends on I/O quantity |
Local expansion capability | n/a | n/a | Medium | High |
Remote expansion capability | n/a | n/a | Medium | High |
Programming languages | n/a | Ladder, some function blocks | Ladder and maybe other specialty function blocks | Multiple-Ladder, structure text, function block, etc. |
Programming software cost | n/a | Free to low | Free to medium | Medium to High |
Hardware cost | Lowest | Low | Medium | High |
Program memory | n/a | Low | High | Very High |
Ease of use | Easiest | Easy | Medium | Difficult |
Flexibility | Very low | Low | High | High |
Connectivity to other systems | Hard-wired only | One communication port and protocol | Multiple communication ports and protocols | Multiple communication ports and protocols |
PACs: Lines are once again blurred, but this time between high-end PLCs and PACs. But PACs add more capabilities than PLCs, particularly for control of very complex systems. PACs can handle advanced motion control, incorporate vision systems, and perform advanced control of analog loops—a set of tasks that might unduly burden a PLC.
Distributed control systems (DCS) were intentionally left out of this discussion because most are now PAC-based. While exceptions abound, these criteria are a good starting point for controller selection (Table 1). Table 2 shows the current and anticipated future state of these markets.
– Don Pham is product manager at Idec; edited by Mark T. Hoske, content manager, CFE Media, Control Engineering, [email protected].
Key concepts
- Criteria can help when selecting among relays, smart relays, PLCs, and PACs.
- Considerations include I/O needs, expansion, programming, and connectivity, among others.
Consider this
Can these 11 criteria help with the selection of your next controller?
ONLINE extra
Control Engineering articles linked below look at PLCs versus PACs, PCs versus PLCs, the future of the PLC, and managing the DCS upgrade.