Too many companies have lost their capacity to train inexperienced engineers. How can we hope to replace the practical knowledge lost to retirement?
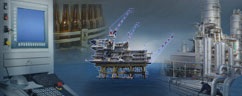
A lot has been written lately about the shortage of candidates for positions in the process control field and how we’re going to grow the next generation of process control engineers and technicians. As with a lot of other careers, companies have grown accustomed to being able to pick and choose between candidates in recent years. That is coming to an end as more and more of my contemporaries finally decide to retire and as more and more of the installed base of control systems become terminally obsolete. Corporations have also gotten used to doing more with fewer people. The problem is that those they kept have their hands full just keeping things running. There’s no time to teach new people how to do the work.
We’d like to believe that if we just hire from the right engineering disciplines that we won’t have to train, but the reality is that the curricula in our universities do not teach much of what’s needed in the practical application of process control to a single discipline. Chemical engineering grads have been exposed to process design, so they have the tools to do some of the work, but if they’ve been exposed to process control, it is generally a theoretical approach. If the ChEs have been exposed to the electrical engineering curriculum, it amounts to just that, exposure. Electrical engineering grads are to some degree even more disadvantaged because if they’ve taken a controls course, it has focused on servo control and again the theoretical approach of Laplace transforms and Bode plots. The EE grads often have the added disadvantage of very little exposure to industrial processes. They may or may not get exposed to high voltage devices, thermodynamics, and fluid mechanics, though they may take survey courses of these topics. Mechanical engineers are in a similar boat as EEs since they may or may not get any process engineering along with their courses in fluids and thermodynamics and will have only taken an EE survey course and a freshman chemistry course.
Being a mechanical engineer, I had to learn how to design control circuits properly including motor control circuits. That included understanding issues around proper grounding techniques, which became even more problematic with the early DDC and DCSs because of their sensitivity to noise. I also had to learn proper methodology for installing instrument impulse lines, something no conventional curriculum teaches, nor do they teach how to select measuring devices. Which curriculum teaches you why you should always start large fans against a closed damper? Which teaches you why the pressure and flow measurements in the boiler’s main steam line should always come off the side of the pipe? Which teaches the advantage of a thermocouple over an RTD that has nothing to do with accuracy or range? (Hint: which one can be “fixed” with a hammer at 2:00 am?) Which teaches the design of failsafe circuits? These are the kinds of things that I mean when I speak of the practical application of process control. Such things can only be taught effectively on the job and, in some cases, through direct experience of what happens when you do it wrong.
So, what are your arcane bits practical process controls that you’ve learned over the years? What do you think is the best way to impart those gems of knowledge to the next generation? How can you convince your company that they have to train new grads on more than the company culture and HR policies?
This post was written by Bruce Brandt, PE. Bruce is the DeltaV technology leader at MAVERICK Technologies, a leading system integrator providing industrial automation, operational support, and control systems engineering services in the manufacturing and process industries. MAVERICK delivers expertise and consulting in a wide variety of areas including industrial automation controls, distributed control systems, manufacturing execution systems, operational strategy, and business process optimization. The company provides a full range of automation and controls services – ranging from PID controller tuning and HMI programming to serving as a main automation contractor. Additionally MAVERICK offers industrial and technical staffing services, placing on-site automation, instrumentation and controls engineers.