Industrial Ethernet networks have changed the manufacturing landscape in the past several years and will continue to do so, but companies should also be prepared for when the network fails and have safeguards in place.
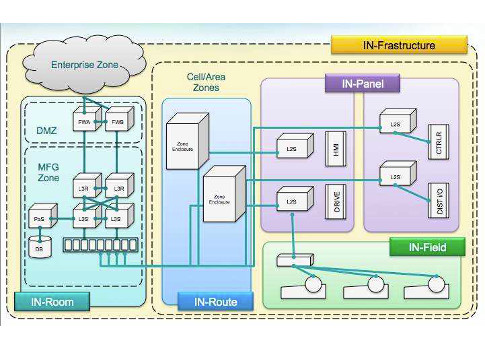
Industrial Ethernet networks have changed the manufacturing landscape in the past several years and will continue to do so as everything becomes more interconnected, from the plant floor to operations to information technology (IT) resources. Ensuring reliable power for networked resources lowers risk of outages for critical assets.
"There is evidence all around us that industrial networking and Industrial Ethernet is becoming more pervasive," said Paul Schildhouse, senior product manager for Panduit Corp. "There are estimates that 100% of plant floor devices will be providing data as soon as 2018. Devices that previously used simple connections to provide a single function are migrating to intelligent communications with richer data capabilities."
Convergence, IoT market trends
Three technology trends have been used by manufacturing companies to become more interconnected and to improve operational efficiency:
- Converged plantwide Ethernet (CPwE)
- Internet of things (IoT)
- Commercial off-the-shelf technology (COTS)
CPwE can reduce the number of different networks and can be used to seamlessly share information throughout the plantwide architecture. Its common network design and troubleshooting tools also simplify maintenance, Schildhouse suggested. The IoT is the network of physical objects that contained embedded technology by 2022. This embedded technology can communicate and sense or interact with its internal states or the external environment.
CoTS technology provides better availability with standards-compliant devices and suppliers, and easier access to new technology that doesn’t require the current system to be taken down and built from scratch, Schildhouse said.
Ethernet customer concerns, best practices
Industrial Ethernet networks certainly have the capability to improve a manufacturer’s operational efficiency. As companies look to "lean" manufacturing as a way to remain profitable, this puts an added burden on resources.
"It shouldn’t be a surprise that in today’s ‘lean’ organizations resources are scarce and organizations are looking for systems that reduce both support expenses and labor," Schildhouse said, especially true as business and manufacturing systems are converging for some companies. This raises the question of whether someone in operations or information technology is responsible for the network. For end users, this raises concerns about accountability and network support, as well as maintenance and support costs.
A reference architecture is:
– A solution that brings together operations and IT and allows them to focus on one solution
– The fundamental organization of a system, the relationships between its components and the environment, and the principles governing its design and evolution.
– A way to allow IT and operations to outline a solution that incorporates their collected knowledge and experiences.
Network power problems
Even if a company is prepared and has taken the necessary steps to streamline its operations so everyone is in sync, the network can still fail. When the network fails, particularly as Ethernet and wireless technologies become the dominant force on the plant floor, this can cause serious headaches, operationally and financially, Schildhouse said. The biggest power issues companies face are:
- Interruptions
- Downtime costs
- Centralized backup
- Uninterruptible power system (UPS) battery life
- UPS battery maintenance
- UPS device management.
Power interruptions, while mostly short-term, are a nuisance because they interrupt operations and halt productivity. They also cost companies money. Even a short-term power interruption can cost a company several thousand dollars per minute in downtime costs. An operable UPS is useful in this circumstance, but even a UPS needs a backup or a buffer for major power failures. Maintaining the UPS, particularly its battery, can be difficult on a manufacturing floor that is well above room temperature.
Network power solutions
A better solution, Schildhouse said, is to provide backup power to your industrial Ethernet network to "right-size" the UPS to the application need. An ultracapacitor UPS is particularly useful because it is maintenance-free and can last up to 20 years if properly maintained.
"It can mitigate the risk of network downtime, eliminate maintenance and reduce overall cost of ownership, and greatly simplify device management for increased peace-of-mind," Schildhouse said.
As an added benefit, the ultracapacitor UPS can be connected to the network. This allows maintenance engineers and technical support to manage it remotely.
Network power reliability
Industrial Ethernet networks are becoming more common on the manufacturing floor. Companies need to be aware that there will be power failures and challenges from time to time. If they’re prepared, a good industrial network power backup strategy can prevent unnecessary downtime, reduce maintenance costs, and allow the user to manage the UPS remotely.
– Edited by Chris Vavra, content specialist, CFE Media, Control Engineering, [email protected].
Learn more about how to improve your industrial network in the Control Engineering webcast Power-Up Your Industrial Network: Improve Availability and Decrease Maintenance on July 17, 2014. Ask your questions in the Q&A at the end of the presentation; if you’re watching the archived version after that date, questions from others and their answers also will be included.
www.controleng.com/webcasts area includes multiple industrial networking topics.