Time-sensitive networking (TSN) enhances standard Ethernet by providing deterministic communication, synchronized clocks, traffic shaping and more.
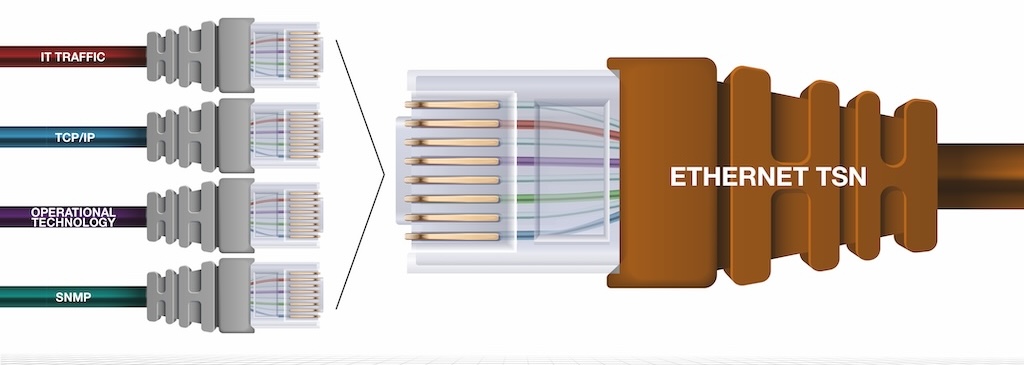
Learning Objectives
- Understand the value of Ethernet.
- Understand the benefit of time-sensitive networking (TSN) architecture.
- Understand where this technology fits in a manufacturing facility.
Time-sensitive networking (TSN) insights
Industrial networks are crucial for control system performance and reliability, impacting quality through efficient communication between sensors, valves, motors, and other elements.
Ethernet with TSN provides deterministic real-time communication with low latency and data loss, making it ideal for industrial automation and other applications requiring precise timing.
Industrial networks enable communication between elements of a control system. These include sensors, valves, motors, pumps, drives and much more. Control communications can have impacts on performance, quality, and reliability. In addition, control devices or the controller itself play an important role in information gathering to support layered analytics. Selecting an industrial network is pivotal to creating the most competitive machine, production line, or process.
Ethernet with time-sensitive networking (TSN) is an advanced networking technology that enhances standard Ethernet with features required for deterministic communication and precise time synchronization in industrial and automation applications. TSN is an IEEE 802.1 standard that adds mechanisms to Ethernet to enable deterministic real-time communication with bounded latency, low packet delay variation and extremely low data loss. This makes it suitable for applications with stringent timing requirements such as industrial automation, automotive, aerospace and professional audio/video.
Nine criteria for choosing an industrial network
When it comes to choosing an industrial, there are nine things engineers and companies should prioritize in the selection process:
-
Performance – Both in speed and determinism
-
Reliability – Supports redundant or ring architectures
-
Medium – Optical, wired, wireless
-
Connections – Ethernet is the most pervasive connection and cable
-
Convergence – Able to coexist with multiple protocols
-
Open – Supported by third-party vendors
-
Proven – Globally registered standard with history of adoption and use
-
Embracing – Able to integrate devices with other protocols through converter use
-
Supports standard IT tools – SNMP for device management and troubleshooting.
Performance – The need to consider performance in an industrial network will vary with the size of and character of the application. Small applications will have fewer devices and can tolerate lower communication bandwidths. Motion control applications may need higher performance communications and even deterministic communications. Bandwidths are now less of a consideration as in the past, and gigabit Ethernet is becoming more common. In addition, new technologies such as Ethernet with TSN can improve performance and can give machine vendors a competitive advantage.
Reliability – Supports redundant or ring architectures. The proper architecture can deliver tolerance to communication failures, either using redundant communication paths, or ring architectures that can deliver continued control in the event of a break in a communications link. Star architectures are also important, in their ability to isolate communication segments from one another. These are common architectures for Ethernet and are supported by the latest Ethernet with TSN.
Medium – The choice of medium—optical, wired or wireless — will largely depend on the operating environment. High electrical noise environments or applications that require electrical isolation will benefit from optical fiber communications. Applications with mobility requirements such as autonomous mobile robots (AMRs) or crane systems can benefit from wireless communications. Wired applications are still the default and likely the most cost-effective solution.
Connections – In industrial networks, the Ethernet connection RJ-45 standard is the most dominant connection type. However, environment requirements for water or dust protection may define other connection types, like the use of circular connectors, M12 and M8 being two of the most common for industrial settings for your Ethernet cables.
Convergence – In the world of Ethernet communications, it is common to find many types of communications and conversations coexisting on the same cable. Modern Ethernet switches can streamline traffic on networks and help to improve communications speed, but Ethernet is a “best effort” form of communications and is non-deterministic. Efforts have been made by some vendors with token passing or other techniques, to manage Ethernet communications for use in applications that require determinism, however when other, unknown traffic is present, determinism becomes more challenging. Increasing bandwidth, going from 10 to 100 MB or 1 GB connections can help, but selecting communications that leverage TSN will let you prioritize critical communications and ensure they will not be impacted by general purpose communications. You can then enjoy the benefits of a converged network – simpler architecture, easier troubleshooting, and reduced costs.
Open – Some industrial networks are closed and limited to only devices from a single vendor. Ideal architectures will leverage open networks with support by many industrial automation product vendors.
Proven – Globally registered standard with history of adoption and use. The most widely-used networks have been made open, to be widely adopted and also have been registered as IEC (International Electrotechnical Commission) Standard (IEC61158: CC-Link IE TSN). These standards are proven and well adopted in industry.
Embracing – No single company can offer all products an application or market may need, and no one protocol is supported by all devices. Protocol converters exist to bridge devices with one protocol to a network with another protocol. Be sure the Industrial Network selected is also supported by protocol converters, providing the broadest potential set of devices with which to build applications.
Supports standard IT tools – If an Ethernet backbone has been selected, then the devices you are using may also support standards common to the information technology (IT) market. Simple network management protocol (SNMP) is the most common IT resource for monitoring and managing devices on a network. SNMP is becoming more commonplace in industrial networks and is a common attribute of some industrial network protocols.
Selecting an industrial network is a crucial decision that can impact the performance, quality and reliability of a control system. By considering various criteria highlighted above, users can create a competitive and efficient system. The choice of medium and connections will depend on the operating environment, while embracing other protocols and supporting standard IT tools will ensure a more comprehensive and versatile system.
Selecting the right industrial network will enable the effective coordination of various elements in a control system, leading to better performance and overall success. Ethernet with TSN is becoming more prevalent in higher performance applications and will only become more mainstream as its benefits of simplified architectures and network convergence become better known.
Thomas Burke is the Global Strategic Advisor for CC-Link Partner Association (CLPA), a content partner. Edited by Chris Vavra, senior editor, Control Engineering, WTWH Media, [email protected].