Do today's new hires have what it takes? Over the past 10 years machine safety has experienced probably the greatest transformation since the advent of machine control technology, which sets the stage for an organizational skills gap discussion. Are the skilled trades persons entering industry over the past ten years equipped to evaluate and trouble shoot 40-year-old control systems without any connection for plugging in a lap top computer?
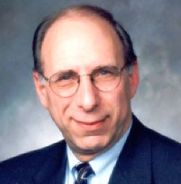
As I stated last October, “Over the past ten years machine safety has experienced probably the greatest transformation since the advent of machine control technology.” In my opinion, this sets the stage for an organizational skills gap discussion. Specifically, are the skilled trades persons entering industry over the past ten years equipped to evaluate and trouble shoot 40-year-old control systems without any connection for plugging in a lap top computer?
Clearly, 1970s technology pre-dated microprocessors, software, diagnostics, and more. Almost everything in an architecture involved hard wired components and machine control was relay based. As technology rapidly hit the floor with PLCs, application software, and diagnostics through the 70s, 80s, and 90s so did the training for skilled trades persons. These folks grew with the technology curve plus they still had the skill sets to maintain and troubleshoot the older systems. They could also maintain and troubleshoot the safety layer of the architecture which was required to stay hard wired by industry standards.
Now, fast forward to 2012 where the safety layer can now be re-integrated with the rest of the machine control system. This re-integration began in 2002 when NFPA 79, Electrical Standard for Industrial Machinery, allowed Safety PLCs and safety communication busses to be used for safety functions. Since 2002 industry has seen skilled trades personnel leave the work force and new skilled trades personnel enter. These young employees have gone through school with electronic text books, high tech systems in their labs, the internet as a basis for communication, and iPads for daily use. What happens when these newly hired skilled trades personnel are faced with a forty year old machine with a control system of 300 relays with one welded point? There’s no place to plug in their lap top or IPad to diagnose the fault.
Is training the answer for new personnel? For the latest technology – training classes abound. Does anyone know of one place to get training for forty year old control systems?
Don’t chain me to the floor on 40-year-old control systems – that’s not the point!
The point is – do we have a skills gap in our trades personnel? We still have a ton of old machine control systems (including machine safety) and a shrinking pool of skilled trades personnel with “know how” to maintain and trouble shoot these systems. People tell me it’s hard to find qualified personnel capable to revert to old schematics, analog meters, or even a primary understanding of engineering basics. Our ears used to be a primary diagnostic tool.
What experiences have you had along this changing landscape of evolution?
Your comments or suggestion are always welcome so please let us know your thoughts. Submit your ideas, experiences, and challenges on this subject in the comments section below.
Click on the following text if you don’t see a comments box, then scroll down: Machine Guarding – trouble shooting old systems is doomed with iPad skills.
Related articles:
Cost Savings Opportunities in Machine Safety
Machine Safety Pays
Risk assessment – A best practice for sustainable performance
Machine safety pays off
Contact: www.jbtitus.com for “Solutions for Machine Safety”.