The footprint of control equipment—the number of devices, physical size, and energy consumption—is getting smaller. Three companies offer observations on where technologies are headed in the server room and individual control cabinet.
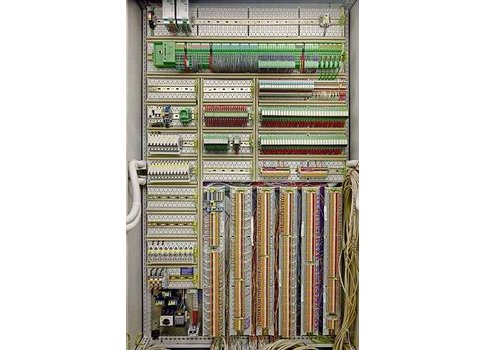
While the economic lows of 2009 and the recession that followed are behind us, that period brought about a number of changes that continue within the industrial sector. Most prevalent of them, of course, were the impacts on the larger workforce. Everyone, including plant operators, maintenance people, equipment designers and OEMs, system integrators, and panel shops is doing more with less. One way in which that has been manifest has been a re-evaluation of the control cabinet designs and looking at ways to cut overhead from the cabinet itself.
Chief among these ideas was cutting the size of the actual cabinet. Simply put, smaller cabinets equate to smaller costs. However, shrinking the size of the panel means engineers must first figure out a way to shrink the components on the panel. Luckily for engineers today, there are more high-density products on the market than ever before, making the task of shrinking the cabinet significantly easier than it would have been even 10 years ago.
To help explain, let’s look at the foundational components within nearly every control panel: power supplies, relays, and terminal blocks. While each technology is fundamentally basic, great strides have been made by a number of manufacturers to allow these components to do more with less, to borrow a phrase offered earlier, with “less” referring to size.
Let’s start with the heart of the control cabinet: the panel power supply. Power supply technology has grown by leaps and bounds in the past 10 years. Today, a variety of manufacturers offer power supplies with a list of offerings, including current boost, remote alarm features, and circuit breaker tripping technology. The most amazing part of all of this is that these features are housed in power supplies that consume an ever-shrinking footprint. For example, 10 years ago, leading power supply manufacturers such as Phoenix Contact, Sola, and Puls offered 10 A, DIN rail-mountable power supplies that were about 160 mm wide. Today, these manufacturers offer 10 A power supplies with even more features in a design that takes up only 90 mm of DIN rail space. That’s a space saving of nearly 50%.
Likewise, relays have gotten much smaller. Terminal block–style relays have been on the market since the late 1990s. However, the installed base for their much wider predecessor, the “ice-cube” relay, remains very large. The leading benefit of terminal block relays is their size. At only 6 mm wide, they consume a fraction of the space taken up by ice-cube relays. Of course, they are limited in most cases to 6 A, so direct replacement will not be possible in every situation. However, since ice-cube relays used in control cabinets use about 25 mm each, it’s easy to see how much room can be opened up by switching to terminal block relays, which are only a quarter of that width.
Terminal blocks are the foundation of every control panel, and even a product as basic as that can do more with less. Over the years, simple changes in the construction of terminal blocks from most manufacturers have resulted in vast improvements. For example, higher-quality metals allow smaller terminal blocks to carry more current so the overall footprint of the terminal block decreases. Given the number of terminal blocks in an average control cabinet, saving a few millimeters on each quickly adds up as the number is multiplied.
Additionally, leading manufacturers, including Weidmuller, Wago, and Phoenix Contact, offer terminal blocks capable of landing multiple wires. For example, Phoenix Contact offers one product line that allows users to land two wires on each side of the terminal block such that two separate signals can be passed. This essentially gives users the ability to cut in half the number of terminal blocks they need. Again, this directly leads to a significant reduction in the number of components and, consequently, the space needed in the cabinet.
Engineers looking to reduce the overall cabinet footprint have more options than ever before. In doing so, they simply need to look at the core components used in nearly every control cabinet: power supplies, relays, and terminal blocks. In most cases, upgrading to current technology can lead to a reduction of 50% over equivalent components used just a decade ago. Individually, much is to be gained by upgrading each of these components; however, users looking to make a huge impact on their bottom line, and potentially cut the overall cabinet size in half, should seriously consider upgrading all three of these component types.
Jeremy Valentine is interface product marketing manager for Phoenix Contact, USA.
Smarter, more powerful devices combine functions
There are many control innovations today that reduce the space required for control cabinets and machine footprints. Miniaturizing control devices and other industrial electronics has been a major driving force in this regard. For example, the power of embedded PCs continues to advance with powerful multi-core processors available, up to an Intel Core i7 2715QE 2.1 GHz quad-core CPU. With this kind of processor power, a small embedded PC that already serves as a machine’s PLC can also double as a motion controller, HMI processor, communication gateway, and more. This can help machine builders and manufacturers reduce the amount and variety of hardware they must equip on their machines.
When a powerful embedded PC is paired with the right software, it can easily handle complex motion control with numerous coordinated axes. It is also possible to do a great deal of multi-tasking with this kind of device by adding multi-PLC functionality, HMI, standard PC functions, and more, all in one box. This eliminates the need for several separate hardware devices that had been used in the past, shrinking machine footprint as a result.
Modern I/O technology has added capabilities that can handle digital and analog data acquisition functions while providing a range of special functions for various kinds of measurement, monitoring, safety, and even small drive technology. Amplifiers for servo motors up to 4 A are now available in DIN rail-mountable 12 mm wide enclosures. This kind of space saving is multiplied when applications require more axes of motion. For example, an application with five axes of motion within that power rating will take up only 60 mm of width in the electrical cabinet. Similar I/O solutions are available for stepper and dc motors. Taking direct signal measurements at the I/O terminal can reduce the number of transducers needed to monitor electrical data. These devices can operate with supply networks up to 500 V ac, 5 A, supplying power measurement statistics and diagnostic information to plant engineers.
Modern safety hardware also comes into play in saving space—integrated safe I/O systems can provide machine safety functionality for features such as e-stops, light curtains, protective doors, two-hand control, safety switching mats, safe drive functionality, and much more. This technology doesn’t require an isolated safety controller with its own network, software, and infrastructure—the safety I/O terminals easily can be added alongside standard I/O terminals and connected to a standard higher level controller.
Matt Lecheler is a motion specialist for Beckhoff Automation.
Virtualization: Controlling your PC population
Virtualization is a technology that allows running two or more operating systems side-by-side on just one PC or server, and it is rapidly being adopted in the industrial world. While the word “virtualization” is simply another term for abstraction, in practice it allows engineers to save cost, reduce footprint, and consolidate systems in ways that were not previously possible.
Deploying virtualization allows multiple “virtual machines,” each running its own operating system and application, to function at the same time on a single physical machine. Virtualization achieves this while guaranteeing that a given virtual machine gets exactly the amount of resources required to do its job, and ensuring any issues with one virtual machine won’t impact another. This type of consolidation reduces the need for multiple machines and maximizes the use of hardware resources.
By improving hardware utilization, plants are able to cut down on the number of physical computers they require, which has a direct correlation with the footprint of a control system.
When it comes to a discussion of virtualization as it relates to an industrial control system, it is important to understand the true meaning of the term “footprint.” In addition to the physical space occupied by servers, workstations, and ancillary components, factors such as power consumption, cooling requirements, equipment weight, and operating noise all contribute to the system footprint. In greenfield plant projects, companies must find the best way to reduce their control system footprint without negatively impacting project results. For companies with existing installations, reducing footprint improves the working environment for operators while reducing operational cost.
How virtualization can help
In the server room, virtualization solutions reduce the physical footprint of hardware components in the plant server room. Facility savings are both direct (consumed by the hardware) and indirect (ancillary service reductions). Running these virtualization solutions on blade hardware then provides the ultimate synergy of resource utilization provided by virtualization with the hardware density provided by blade technology.
For a typical-sized DCS cluster, using traditional methods of deployment might take 50 U (rack units) of space for the server and workstation equipment. Virtualization with blade technology could enable the same functionality in approximately 7 U of space. With the reduction in space, there is a corresponding reduction in weight, power consumption, and cooling. Not only is the system footprint reduced in size, but also the space it does consume is more predictable. This is particularly advantageous with packaged solutions where there is a desire to have a standardized layout, with the flexibility to accommodate the individual needs of customers.
When power requirements are reduced, there is also a subsequent reduction in the amount of uninterruptible power supply (UPS) capacity required by the equipment. Given that the equipment runs cooler, there is a corresponding power reduction due to minimized cooling needs. Both the UPS and cooling equipment are lighter as well.
The above footprint benefits for server rooms are particularly important for industries such as oil and gas, where offshore facilities have inherent space constraints and other physical and operational considerations.
In the control room, virtualization and thin client visualization are two powerful technologies that are complementary and even more effective when implemented together. In industrial environments, these technologies intersect when thin clients are connected to virtualized systems to provide visualization and operator interface.
A thin client is a stateless, fan-less appliance that has no hard drive, consisting only of simplified hardware and software. In contrast with a regular deployment, applications, sensitive data, memory, and so forth, are stored back in the data center when using a thin client.
Virtualized servers with a thin client operator interface are the best option for many applications commonly found in the plant control room. Like the server room example, users can optimize the same footprint vectors—equipment space, cooling, and noise. This is achieved through the thin client’s compact form and lower power usage, and lack of rotating parts such as hard drives and fans. It is not even a requirement that thin clients are co-located in the same facility or geographical region as the servers, as the link to the server is made via a network connection, and all the core software and performance reside in the host.
Paul Hodge is Experion infrastructure and HMI product manager for Honeywell Process Solutions.
ONLINE
www.phoenixcontact.com
Key concepts:
- Growing sophistication of control equipment is reducing the collective amount and size of equipment, permitting more efficient use of plant space.
- Energy use has also reduced direct and ancillary costs as more efficient equipment requires less cooling, etc.