Petrochemical plant adds new physical-layer technology to its long-running fieldbus networks.
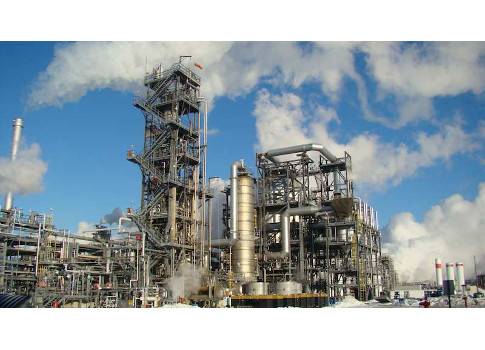
Today’s process industry operations require state-of-the-art automation technology in order to reduce raw material costs, increase yields, comply with regulatory standards, and maximize revenues. But plant managers must also ensure that control systems provide reliable operation and a low cost of ownership over the life of installed assets.
Although fieldbus-based control systems have been used in countless applications to optimize process operations, instrumentation, and control, engineers need effective solutions protecting the fieldbus physical layer from short circuits, improper termination, interference and other potential problems.
Industrial facilities can avoid many fieldbus installation issues from the beginning simply by utilizing the latest generation of device coupler technology. Current technology offerings simplify fieldbus system design and expansion, minimize capital equipment costs, and significantly reduce the time required to install and troubleshoot devices in the field.
Background
Ashland Inc. is a global leader in providing specialty chemical solutions to customers in a wide range of consumer and industrial markets. The company includes four commercial units-Ashland Specialty Ingredients, Ashland Water Technologies, Ashland Performance Materials, and Ashland Consumer Markets-serving customers in more than 100 countries.
In August 2011, Ashland purchased International Specialty Products Inc. (ISP), which had acquired BP’s world-class 1,4-butanediol (BDO) production operation in Lima, Ohio, six years earlier. The plant has an annual capacity of 65,000 metric tons of BDO, an intermediate ingredient in common industrial and commercial products. BDO is further processed to make items such as engineering plastics, polyurethane systems (e.g., golf balls, skateboard wheels, car bumpers) and carrier solvents in printing inks and cleaning agents.
The Lima plant’s integrated butane-to-butanediol production process combines catalytic oxidation of butane in air with fixed-bed fatty acid hydrogenation technology. The facility processes butane and air to maleic acid in a fluidized bed reactor, and maleic acid to BDO in a high-pressure, H2-rich, fixed-bed hydrogenation reactor. It also utilizes an off-gas boiler for steam and environmental compliance (Figure 1).
Reasons for using fieldbus networking
When deciding to build the Lima BDO production operation, plant managers sought to achieve high reliability without the complexity and redundancy of a traditional process control system. John Rezabek, process control specialist for Ashland at the site, said, "In designing the BDO plant, we wanted to avoid older analog communications. Why would we build a new plant and shackle ourselves to 1980s technology?"
Rather than employ conventional automation technology, the Lima plant called on Emerson Process Management to supply a DeltaV DCS using the Foundation fieldbus protocol. This all-digital, two-way communications system interconnects interoperable field equipment from different suppliers-such as sensors, actuators, and controllers-on a single network. The fieldbus system infrastructure is designed to reduce the amount and complexity of wiring throughout a plant (Figure 2).
Foundation fieldbus also transmits multiple variables, enabling a reduction in process variability as well as device identification information. The technology allows collection and transmission of robust instrument diagnostics, thus reducing unnecessary shutdowns and improving safety and regulatory compliance.
As part of the fieldbus-based automation architecture at the Lima facility, PID control algorithms are located in a majority of the digital valve controllers. In addition, all dual-element transmitters are equipped with on-board signal-select blocks. A total of 80 fieldbus H1 (31.25 kbit/s) segments connect approximately 600 fieldbus instruments and valves, handling 150 control loops.
The facility’s original 400 discrete I/O devices (mostly on-off valves) were wired directly to process controllers, which have since been supplemented with dozens of fieldbus-capable on-off valves. The system also includes approximately 400 emergency shutdown I/O and 200 RTD (resistance temperature detectors) sensors and motor statuses integrated through Modbus multiplexors.
With this configuration, the entire fieldbus architecture (with the exception of emergency shutdown functions) is covered by a single operating system.
According to Rezabek, one of the major advantages of Foundation technology at the Lima BDO plant is its ability to lower capital costs and operating expenses through reduced wiring and the extraordinary confidence and accuracy provided by an all-digital protocol. Speedy, robust, and deterministic process control proved to be a significant benefit as well.
Physical layer considerations
Foundation fieldbus requires some additional considerations over and above traditional 4-20 mA control systems. Careful planning and upfront engineering are key to the success of any fieldbus project, and end users must be mindful of physical layer requirements such as power conditioning and segment termination.
"Sloppy and unprofessional wiring is responsible for most of the challenges on fieldbus projects," Rezabek said. "The most frequent causes of performance and reliability problems are loose terminations and incorrect shield grounding. Over 13 years of operation, we found it was extremely efficient to integrate new devices by extending existing segments. Our original fieldbus segments reached virtually every corner of the plant, and had ample spare capacity. Just about any spur can be made to serve as an extension of the trunk, and more devices can be connected to a coupler at this point. While this strategy saves us a lot of labor, conduit, and wire (and money), it’s complicated by having to relocate the segment’s terminator. Typically, we’d have to wait months for a unit outage that would allow the terminator to be moved."
All fieldbus segments need proper termination to operate. In particular, over- or under-segment termination can be a significant issue during plant start-up and commissioning. The terminators act as both end loads to minimize reflections and to convert the current based signals to voltage so they can be read by devices. Accordingly, each segment must have exactly two terminators. In some cases, multiple terminators are placed on an individual segment, creating communication errors.
Physical inspection of junction boxes and field enclosures is often the only way to locate and correct the number of terminators (Figure 3). Short circuits are another common concern in fieldbus installations. Maintenance technicians can jostle cables, corrosion can weaken connections, and vibration from pumps and motors can loosen cables and connectors.
Since all devices are wired in parallel, plant operators must be concerned about what might happen to an entire fieldbus segment if any single instrument shorts out. Engineers designing fieldbus segments are faced with incorporating some form of spur short-circuit protection, which may be either active or passive in design. A current limiting approach restricts the amount of power short circuits can draw to between 40 to 60 mA while also holding the fault on the segment continuously. The additional current draw can cause other devices to drop off the network. Accordingly, the effect of a single current limited short circuit must be accounted for in segment design with extra power supply reserves or fewer devices per segment.
Control modernization project
In October 2012, Ashland embarked on an upgrade of the Foundation fieldbus system at the Lima BDO plant-one of the earliest installations of its kind in the process industries. The scope of work, completed during a three-week planned outage, involved enhancements to the existing DeltaV system, as well as replacement of legacy terminal blocks, instrument wiring, power suppliers, and other fieldbus physical layer components on 60 device segments throughout the facility.
At the time of the plant’s construction in 1999, device coupler technology did not exist. Control system designers had to rely on terminal wiring blocks, which didn’t offer short-circuit protection or current limiting on spurs. Although this approach was convenient for field wiring, it caused concerns about maintenance activities if a technician inadvertently shorted out the segment. When terminal wiring blocks are used in a plant, personnel also cannot perform live work on instruments located in Division 2 classified areas.
An initial solution to this problem was the use of quick-disconnect connectors, which allowed technicians to disconnect devices without unnecessary risk of shorting out conductors and shutting down segments. However, electrical code restriction authorities also called for the installation of disconnect switches to comply with hazardous area requirements (Figure 4).
Over the years, many of the disconnect switches became corrupted by corrosion and water, posing an operational liability (Figure 5). This prompted plant engineers to seek a way of replacing legacy hardware on control loops throughout the facility while still maintaining existing area classifications. The work had to be completed in two stages, with the first phase focused on eliminating the switches on the device side of the installation and the second phase devoted to rewiring junction boxes.
Rezabek noted that the choice of a device coupler technology was particularly important on the Lima upgrade project since device couplers touch every valve in the plant. He and other team members determined that a coupler design incorporating short-circuit protection and providing non-incendive spurs was necessary if the disconnect switches were removed.
As the vital link between the process control system and fieldbus devices such as valves or temperature and pressure transmitters, device couplers can be likened to the master link of a chain. Just as a chain is only as strong as its weakest link, so must device couplers excel at their appointed task of connecting and protecting device inputs onto the bus.
In general, fieldbus device couplers reduce the design efforts of system integrators and the wiring workload for field installers by enabling fast and easy connection or disconnection of fieldbus devices into the required segments. Beyond that, the individual features of the device coupler can make a significant difference in whether or not a fieldbus system starts up quickly and performs reliably over the long term.
A different coupler approach
During preparations for the control system modernization at the Lima BDO plant, project engineers evaluated a number of alternative fieldbus physical layer technologies based on price, performance, and reliability. They ultimately chose to install MooreHawke’s TRUNKGUARD Series 200 (TG200) device couplers.
MooreHawke characterizes its DIN rail-mounted TG200 as a "fourth generation" device coupler. Starting with early models intended for use with parallel bus wiring, device couplers have advanced from using fuses to safeguard fieldbus installations from failure, to current limiting technology to improve protection of the device network.
However, current-limiting places additional load on the bus that can affect other devices. Moore Industries’ fourth generation device coupler solves the common issue of segment termination and short-circuit protection by using end-of-line-sensing auto termination and "fold-back" short-circuit protection (Figure 6). Rezabek admitted some trepidation in installing this new technology, due to its perceived complexity and advanced functionality.
"On the surface, these device couplers have more features than competitive solutions," he said. "We wondered whether functions like fold-back short-circuit protection and auto-termination would create compatibility issues with power supplies, device couplers, and other equipment installed on our existing segments. To date, everything has worked as we anticipated. It’s there when you need it, and the rest of the time it goes unnoticed. We’ve been able to mix and match different suppliers’ couplers on our segments without any difficulties whatsoever."
The new breed of fieldbus device couplers are specifically designed to assist in segment commissioning by eliminating errors associated with segment termination, including failures resulting from over- and under-termination. They also address the problem of excess current (from a spur short) causing the voltage to drop below the segment threshold of 9 V.
With the auto-termination capability, local devices on a segment continue to function even if remote couplers are accidentally disconnected. This prevents costly downtime and hazardous situations. Segment termination automatically activates when the device coupler determines it is the last fieldbus junction on the segment. If it is, the segment is terminated; if it is not, the coupler doesn’t terminate the segment since the downstream unit will assume that responsibility. To terminate a segment properly, technicians are not required to take additional actions such as setting DIP switches or disconnecting terminators on one coupler and reconnecting them on another.
Earlier device couplers used short-circuit protection that limited the fault current to a fixed-and always higher-level (typically 50 to 60 mA) that can cause other devices to fail. The new short-circuit technique detects a short in less than 5 microseconds and removes the device from the segment, using a trickle current to determine when the short has been removed. A red LED indicator confirms the short-circuit condition, making the total current draw between 4 to 5 mA during a short circuit. With removal of the short, the spur is automatically reconnected to the fieldbus segment.
A large industrial process operation may have hundreds if not thousands of devices. If a safety margin is implemented, where the entire capability of fieldbus is not used, the cost of all the extra segments can become substantial.
"Thanks to an increased power budget, you can hook up test equipment without having to account for a short circuit," said Rezabek. "If I’m building a segment with other types of coupler technology, I have to add another 50 milliamps of spare power capacity-which is equivalent to two devices’ worth of current-to account for a potential short-circuit load."
The TG200 device couplers aid in the process of connecting test equipment. They come with standard handheld hookup terminals which allow for handheld testing devices to be hooked up simply by connecting the device to the device coupler through the fitted test points.
"The parts of our plant where we performed upgrades were mature, so the auto-terminator capability allowed us to extend segments on the fly as needed," Rezabek said. "We weren’t worried about adding devices because we knew the segment could be extended while running without disrupting communications."
Overall project results
Ashland has been operating with the new device couplers using auto-resetting fold-back protection for spur short-circuit protection. Segment designers in the plant now find that they are able to use the maximum available power without worrying about "headroom."
The technology also assists technicians by providing increased fieldbus status information. Green and red LEDs on each spur help determine if there was proper voltage for a device. Plus, an LED shows whether a terminator had been applied at a specific device coupler.
Rezabek has a philosophical view of the physical layer improvements in his Foundation fieldbus installation. "It (fieldbus) is like the background music in a movie: if the music is good, you don’t really notice it, you don’t pay any attention to it," he said. "That’s the way things have been since the new equipment was installed and we expect it to continue. We already had years of successful experience using a few of the fold-back-type device couplers on selected fieldbus segments, and with the recent upgrade, we’ve now got them on close to 75% of all the segments in the plant and they’re still working fine."
Thanks to a well-engineered fieldbus automation solution, which includes the implementation of advanced device coupler technology, Ashland’s Lima BDO plant has improved its overall operational reliability and readiness, and through greater system design flexibility, can take full advantage of the benefits offered by Foundation fieldbus.
Jim McConahay, PE, is a senior field application engineer for Moore Industries, concentrating on process control instruments, SCADA, SIS, fieldbus, data concentrators, and communications links.
Key concepts:
- Networking technologies are constantly evolving, so it pays to keep up with the latest developments.
- Infrastructure improvements can support better performance for the entire plant.
- Effective technology deployments often depend on human performance and care taken during installation.
ONLINE
For more information, visit:
www.fieldbus.org
Read more about fieldbus technology below.