How to train the next-generation automation workforce: Employers need to provide advanced training; educators need to keep their training programs up-to-date to help next-generation automation professionals.
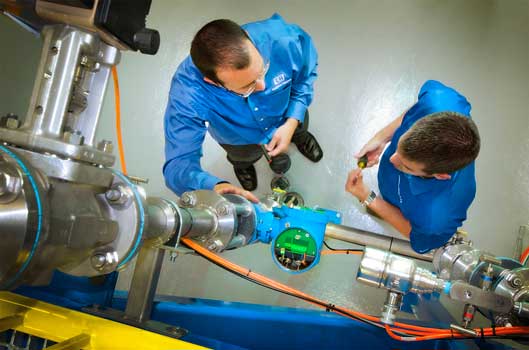
To close the skills gap, employers need to provide advanced training to keep the workforce competitive. Educators need to keep their training programs up-to-date to help next-generation automation and process control professionals. According to the U.S. Bureau of Labor Statistics, talent needed for process-focused automation in the manufacturing industry is expected to grow 6% from 2010 to 2020. At the same time, the manufacturing industry is projected to grow its output from $4.4 trillion to $5.7 trillion, a 2.8% annual increase, by 2020. Many other countries across the globe are experiencing the same trends.
What does this mean for U.S. manufacturing? According to the U.S. Census Bureau, the aging of the Baby Boomer generation is likely to have a greater impact on the overall manufacturing sector than on other sectors of the economy, as workers in this area tend to be older than in other areas. The percent of workers aged 55-64 who were in the labor force increased significantly from 2000 to 2007 as did the proportion of workers over age 65.
This presents all manufacturing employers with the prospect of a large-scale exodus from their workforces, creating skill deficits and knowledge gaps.
Higher productivity, worker shortage
The demand for higher productivity in the process control industries will continue unabated, with manufacturers also facing the retirement of an experienced workforce of operators and technicians in the coming years. This leaves U.S. process industry manufacturers with the dual problem of accommodating the expected 2.8% annual growth in output while seeing many of their best and most experienced workers retire.
What does this mean for next-generation automation and process control workforce? With the shortage of skilled automation professionals and the expected growth in the process manufacturing industry, the United States is the land of opportunity for those interested in automation, controls, and instrumentation. Similar conditions exist in many other nations, particularly in Europe and Japan.
At the same time, the overall unemployment rate in the U.S. and in Europe is quite high, particularly among younger potential workers. It would thus seem that a solution is at hand, with younger workers filling the process automation demand. But there’s a major issue: A skills gap with inadequate training available to develop the talent needed for the automation workforce to grow successfully.
Coping with the skills gap
As the next generation of automation professionals enters the workforce, and as current workers move from analog 4-20 mA field devices to digital solutions, field technicians will need to be trained—or retrained—in new technologies like fieldbus, smart instruments, asset management, advanced diagnostics, and similar technologies that didn’t exist 20 years ago.
Automation professionals need training programs that focus on specific automation topics, as opposed to the general technical education available from traditional sources like local community colleges.
Humans are visual learners. According to a study done by neuroscientist Gordon M. Shepherd, “Vision utilizes nearly half the human brain and approximately 70% of its sensory capacity is dedicated to processing visual information.”
Images are the easiest thing for the brain to remember and are central to the brain’s learning process, which allows humans to switch to “brain video.” The second and third easiest ways for the human brain to remember are through hearing and touch. The more senses stimulated during learning, the more efficiently and quickly a person will retain knowledge—in fact, six times faster than lecture-type learning. Hands-on training allows students to use these three important senses, and is thus of particularly high value.
With the next generation of automation talent growing up as smartphone users and engulfed in the Internet and digital media, it’s easy to see how they can benefit from real-life hands-on simulation training and online web-based learning.
Not only can simulation training help to prevent accidents that cause lower product quality or production waste, it also results in improved process control, greater output, and less downtime—resulting in overall improved operations for manufacturers’ plant processes. Providing flexible training to our next-generation workforce is a key to their success and the success of the manufacturing industry. Hands-on training programs are a good option for companies and individuals seeking a complete and comprehensive training experience.
Training pays off
One often thinks of productivity improvements as simply being able to do a task more quickly. Although that is part of it, many people underestimate the time wasted in things that could have been avoided altogether, such as errors that require rework, or completing proactive tasks that prevent highly inefficient reactive work.
To highlight the advantages imparted by training, not only should higher individual worker productivity be measured, but also higher productivity of the entire manufacturing process.
A more productive worker and a smoother running process plant will pay for money invested in training several times over—not to mention the huge cost savings from prevention of accidents.
Because technology is always changing, existing workforces need to be continually retrained. No longer can operators use simple trial and error to implement 4-20 mA field devices; workers instead need to be trained to navigate complex applications and communication pathways as new technologies become more and more intelligent.
Hands-on training helps new and experienced maintenance and engineering professionals stay up-to-date with the latest trends and technology, allowing them to quickly and efficiently deal with process automation issues as they arise. When the hands-on training is designed to meet regulatory standards, it also helps workers to ensure environmental safety and governmental compliance, and lessen the impact of incidents.
Employers and educators can help
The importance of investing in their skilled workers is often overlooked by employers, so companies need to realize the value that simulation and hands-on training can provide. This value can be measured in a number of ways, including increased employee satisfaction and retention, higher productivity, and fewer process upsets and incidents.
Once the value of training is realized, budget and time must be allocated for ongoing training and continued learning to develop the talent needed to run a successful process plant.
To keep up with today’s challenges, manufacturers can partner with suppliers to ensure that their employees are getting the most out of their training experiences. Creating an awareness of the training programs that are available is also essential, as this can create internal demand and a thirst for learning.
Employers looking to offset their training costs can apply for government assistance and grants geared toward training the unskilled workforce in today’s U.S. manufacturing industry. Government can help bridge the gap in our next generation of unskilled workforce by continuing to provide assistance through programs and funding. Similar programs existing in many other countries, particularly in advanced industrial nations.
Today’s workers or those interested in entering the field of automation can enroll in classroom, instructor-based, or online training courses. These courses may be offered by an automation supplier or by a local community college doing workforce development training. In some cases, these colleges work closely with automation suppliers.
As long as employers are paying process manufacturing workers competitive wages while providing ample advanced training, and educators continue to keep their training programs up-to-date, the future looks bright for the next generation of automation professionals.
– Jerry Spindler is customer training manager, Endress+Hauser. Edited by Mark T. Hoske, content manager, CFE Media, Control Engineering and Plant Engineering, [email protected].
Go Online
Endress+Hauser provides a training video. See also, more details, below.