Motor selection: When deciding on the use of permanent magnet (PM) servomotors or induction motor systems, consider dynamic performance, torque density, inertia matching, and control schemes.
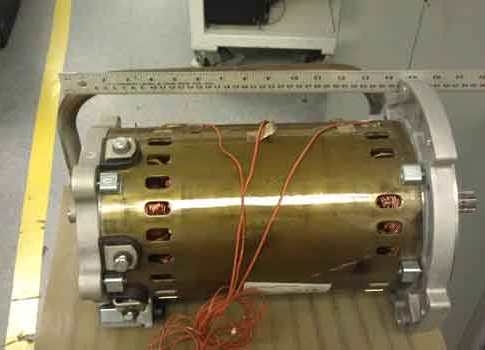
Long considered a mainstay of induction motors, encroachment in the area of 50 hp and greater by permanent magnet (PM) servomotors has been seen recently for some applications. These applications usually have dynamic considerations that require position-time closed loop and high accelerations. When accelerating large loads, permanent magnet servomotors can work with very high load to inertia ratios and still maintain performance requirements. Having a lower inertia typically will allow for less energy wasted within the motor. Torque (τ) is the product of inertia (j) and rotary acceleration (α). If you require inertia matching, half the energy is wasted accelerating the motor. If the inertia ratio from motor to load is large, then control schemes must be dynamic enough to prevent the larger load from driving the motor as opposed to the motor controlling the load.
Trade-offs, negotiation
Permanent magnet servo and induction motors have long had performance areas that overlap but are not a replacement for one another. Advancements in drives and technology for the induction motors have given them dynamic performance that was once the mainstay of permanent magnet servo systems, but this doesn’t mean that the induction motor is a replacement for the servo; it just allows for more options.
Although two motors may appear to be able to do the job related to torque, speed, and thermal considerations, choosing one technology over the other should be approached with intrinsic knowledge of each. A permanent magnet servomotor is a synchronous motor with feedback for commutation, velocity, and position information. A vector-driven induction motor also will require the same feedback control to compete in this performance arena but is powered completely by electromagnetic, not permanent magnetic fields.
Cost may limit size
With the current state of rare earth magnets, it may appear impractical to have a permanent magnet servomotor in an application requiring greater than 20 hp or 30 hp. Should requirements like size and dynamic performance be outside the reach of induction motors, these must be addressed with a PM servomotor in most cases. In general, the constant flux source of a permanent magnet motor can result in a greater torque density than an equivalent induction system. If size matters, then perhaps a system should use one technology over another. Speaking of size, the inertia ratio can be an important figure of merit should dynamic needs arise. If there are high accelerations and decelerations, the size of the rotor will significantly increase inertia and decrease useable torque. In one example, a glass manufacturer combined these technologies and chose four permanent magnet servos rated at 72 hp due to the high dynamic loading and higher performance requirements for the new application.
The size of the equipment and the dynamic needs of this are challenging. A buried magnet rotor design offers a significantly lower inertia than induction motors of similar ratings. With a lower inertia, dynamic performance can exceed other motor technologies.
When considering the technology, the induction motor generates a magnetic field by the stator and armature windings and a laminated rotor structure. The stator is similar to the permanent magnet motor’s armature, which is stationary.
Similarities stop there. While there is a constant state of magnetic flux in a permanent magnet motor supplied by the rare earth magnets, the generated magnetic field will pull on the generated magnetic field of the rotor that has the current induced (hence the term “induction”) on a secondary winding wrapped around rotor armature laminations.
The importance of the word “pull” here has to be noted. There is an interesting but often overlooked phenomenon that you can’t push with an electromagnet. Repulsion forces do not work that way. The attractive force between the two currents will work, but when you generate two like poles, they cancel like a mutual inductor rather than repel when using synchronous control. This is part of the reason that a synchronous induction motor will slightly lag the field rotations. While this makes the control scheme different, it’s still useable. To make the magnetic field rotate around the armature and have the rotor synchronize, you have to change the magnetic fields or essentially collapse all of the energy stored quickly, and this is done by this cancelling current. It makes the controls a little more complicated but well within capabilities of microprocessors and field programmable gate array (FPGA) controllers available today.
Dynamic load advantages
When looking at the PM servomotor, advantages when working with highly dynamic loads are apparent. Rotor size is typically smaller than that of the similar power induction counterpart. That will affect the inertia component, lowering it due to the smaller diameter. Like the induction motor, the magnetic fields around the motor must change to create rotation. The motor will be exactly synchronous to the field since both push and pull of the constant flux from the magnet can be obtained. It will be less sensitive to the air gap of the rotor to armature as well. This is due to the magnets having a mµ equal to air, and as such is considered part of the air gap. This helps improve the motor’s torque density.
Magnetic field changes in the armature can allow for a higher pole count only at the same speed and reduced torque ripple. The rotor isn’t constrained with the buildup of magnetic polarity charge time. These advantages correlate to a smaller physical size when operating less than a few horsepower.
Most servo systems can also handle large loads that are not dynamic providing that the design fits the performance. Directly coupled loads in the packaging and printing industries are typically very large. In many cases, there is a mix of induction and permanent magnet technologies.
There are large direct drive rotary motors that encroach on the domain of induction motors. Applications are numerous. For timing and multiple axis coordination, these permanent magnet motors more precisely control the position-time closed loop requirements than do comparable induction motors and related mechanics.
Rare earth prices
Rare earth availability and price are often brought up when discussing these two motor-control technologies. Rare earth materials and processing have caused uproar in the markets in recent months. The current state of the market indicates that this will not be a permanent issue. Some motors can be modified in design to obtain the same torque using different magnet materials. This hedge of one material’s availability over another allows some more control over the volatility issues that can affect delivery and availability over long periods.
Performance, torque, inertia
When deciding on the use of PM servomotors or induction motor systems, dynamic performance, torque density, inertia matching, and control schemes must be taken in consideration. If you need to maintain a constant velocity with a large load and very high power (>50 hp), the induction motor would likely be a better choice. Should the mass of the motor, dynamic performance, or torque density be important decision factors, then the choice favors the PM servo. Understanding the gray areas helps in discerning one technology over the other. You may have to think beyond the conventional wisdom that permanent magnet servomotors are only for applications below a few horsepower.
– Lee Stephens is senior motion control engineer, Kollmorgen, Radford, Va. Edited by Mark T. Hoske, content manager, CFE Media, Control Engineering and Plant Engineering, [email protected].