Intuitive modern distributed control system pilot was implemented, easing system design, integration and training.
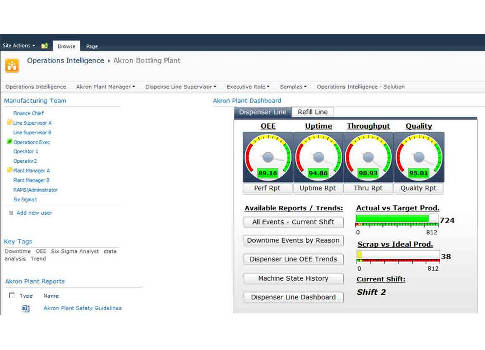
One frozen potato-product supplier operates 15 potato-processing plants globally. The automated French fry production process begins with the delivery of raw potatoes to the plants. The potatoes are then machine peeled, washed, cut, dipped in batter, fried, frozen and finally packaged for distribution. This continuous process takes approximately 1.5 to 2 hours with no bottlenecks or process upsets.
When the supplier decided to build a new continuous process plant for frozen French fries in eastern Oregon, it wanted to establish a new control standard for its frozen potato plants globally. The company decided on a standardized approach in response to challenges encountered with an automated process control system at a similar facility in Louisiana.
Hungry for potatoes
The world’s appetite for French fries is enormous. People consume more than 7 million tons of factory-processed French fries globally each year.
In fact, the use of processed potatoes-including French fries-surpassed the use of fresh potatoes in the United States in 1970. Today, most potatoes grown in the U.S. are sold to a variety of food processors for French fries, chips, dehydrated potatoes and other potato products.
Unsustainable controls
At the Louisiana plant, the company had coded the process control system internally, making it difficult to duplicate at other facilities and challenging to train new operators.
"In the past, the company’s plants had superstar process control engineers. They designed the various systems themselves, writing their own process objects and codes. They knew their system like the back of their hand," said Ed Diehl, president, Concept Systems. "This model was not sustainable. The engineers would retire or move on, and it was difficult to train new operators. The company needed a new process model that was intuitive, supportable and sustainable in the long term."
The company wanted a control platform built on a core set of tools and objects, and easily supported by a third party.
Meeting the needs, building a system
In June 2013, the potato product supplier collaborated with a consultant to design and implement a continuous-process automation system for its frozen French fry production facility in eastern Oregon.
The company selected a process automation system that is scalable, flexible DCS for plant-wide control. Concept Systems worked with process designers to design, implement and commission the new system.
Using a library of process objects—a pre-defined library of controller code, display elements and faceplates—programming and integration time were lessened.
"The system is designed with the operator in mind," said Jim Ford, regional engineering manager at Concept Systems. "The platform is easy to operate and makes it easy to train new operators."
Simulation tools allowed engineers to program and test the system early, helping ease operator onboarding and training. "The simulation tools allowed managers to pretest the system before full implementation, and helped us finalize the system on time and within budget," said Ford.
In addition, integrated historian software gathers valuable data related to system cleaning, production and downtime, archiving the data for electronic reporting and troubleshooting. Production-intelligence software allows system operators to see data in real time through comprehensive reports.
Simulation, design time
"A traditional DCS is very expensive. It takes a lot of knowledge and expertise to configure devices correctly, and operate the system smoothly," said Ford. "The configuration tools, offered with the system, make it easier to design, implement and roll out. The tools saved us design, implementation and training time."
Project detailed design and development began in June 2013, and the facility was up to full production by June 2014. "Without the library of process objects, the company would not have met the timeline for project completion," said Diehl. "We saved hundreds of engineering hours with standard code and tools."
With the new system, operators have insight into real-time process data to predict issues that might occur. Production intelligence allows operators to perform predictive maintenance procedures rather than be reactive. Operators have a direct view into system granularities, helping to manage bottlenecks and make better decisions.
"Using simulation, we tested the full system in motion during the factory acceptance and testing phase," said Diehl. "We performed extensive simulation and testing with the plant operators and team leaders.
– Dan McCarthy is OEM account manager, Rockwell Automation. Edited by Eric R. Eissler, editor-in-chief, Oil & Gas Engineering, [email protected].
Key concepts
- Real-time process data can be used to predict issues that might occur on the production line.
- Engineers can become creative with designing systems, but the systems need to be coded and written down.
Consider this
While employees can come up with their own systems and are allowed to be creative, this needs to be documented so it can be used enterprise wide.
ONLINE extra
– See related stories linked below.
Rockwell Automation is a CSIA partner as of 11/30/2015