Educators, researchers, and robotics companies have collaborated to develop software that enables robots to work in new applications to help shrink the industrial manufacturing skills gap. As a result, more intelligent robotics software now is enabling greater robotics capabilities for the next generation of technology and manufacturing workers. See video.
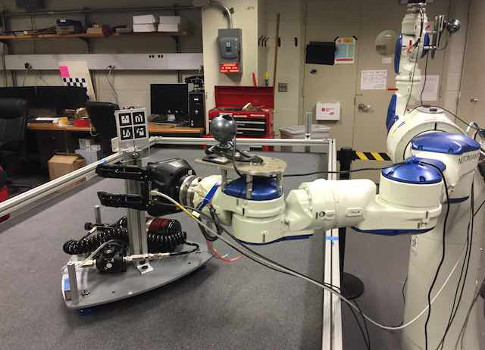
The days of robots as dim-witted devices are gone. The future is filled with smart sensors, software and end-of-arm tooling (EOAT). It’s the brain behind the brawn. The puppeteer pulling the strings. The escape from relentless monotony. Without software, however, brilliant hardware goes nowhere.
Software can’t do it alone. Those robot "brains" extend human capabilities and are a reflection of our vision for what’s possible. That vision gets keener with every generation and every technological leap. Sophisticated software and intelligent robotics depend on the evolution of those doing the research, design, specification, and implementation.
At the Tri-Rivers Career Center in Marion, Ohio, home of the Robotic Advanced Manufacturing Technical Education Collaborative (RAMTEC), students of all ages are preparing for a future populated with intelligent machines and connected systems.
"It’s important that kids start understanding the concept of robotics," said Ritch Ramey, RAMTEC engineering coordinator. "We’re going to see it expand probably tenfold in the use of robots over the next 15 to 20 years. They should at least know the basics of robotics."
According to the International Federation of Robotics (IFR), global robot deployment will more than double from 1 million robots in 2009 to 2.3 million by 2018. To keep those robots humming and evolving, a skilled workforce will be needed. This is a tall order that requires closing the skills gap in automation and bringing younger workers into the fold. RAMTEC is answering the call.
Software certification for robots
Learning to program robots, and the ins and outs of various software platforms, is an integral part of the curriculum at RAMTEC. Students learn to use robots, as well as robotic welding, programmable logic controllers (PLCs), hydraulics, pneumatics, computer-numerical controls (CNCs), computer-aided design (CAD), and 3D printing. These are the necessary building blocks for any budding engineer or robotics technician.
Ramey, a credentialed instructor at RAMTEC, said the collaborative plans to add machine vision to their robotics curriculum, as vision-guided robotics has become essential to many industrial applications. With Industrie 4.0 coming and the Industrial Internet of Things (IIoT) vital to the smart factory concept, he says RAMTEC’s students also will need to learn the Cisco platform as they enter an ever-connected industrial world.
RAMTEC instructors have credentials to teach on several industrial robotics platforms and Ramey hopes to soon add more types of collaborative robots to the program.
The nine RAMTEC sites in Ohio provide students with the software training required for the following credentials:
Fanuc HandlingTool Operation and programming certification
Yaskawa Motoman DX100 basic programming certification
Certified Solidworks associate
AutoCAD certified professional.
"Our students have to do exactly what the industry people do," Ramey said. "The same amount of time, same assignments, same e-learning, and same tests to get their credentialing."
The students are typically high school juniors and seniors, such as Christina Irvine and Brianna Pritchard (see Figure 1) who are learning to use Fanuc’s Roboguide robot simulation software. The students are comparing the software menu on the PC used in their e-learning courses to the actual robot in the Fanuc Certified Education Robot Training (CERT) Cart. This type of virtual and hands-on training prepares the students for Fanuc certification.
"We teach offline programming, because that’s a real tool," Ramey said. "You can’t just stop a production line to program a robot. A lot of the programming is done on the virtual software, either Roboguide (Fanuc offline programming package) or MotoSim (Yaskawa’s simulation software)."
Hands-on robot training
"I don’t think there’s an advantage to either robot programming language," Ramey said. "Whichever one the students learn first is a little harder because it’s a brand new concept. But once the students learn one programming language, they pick up the next one much faster."
At RAMTEC, the student-robot ratio is typically 2:1 or 3:1, which allows students to get significant hands-on time with the robot cell. The students learn welding and palletizing processes not only using the mobile education carts, but also the large payload robots.
"With a lot of schools, they will have maybe 10 of the software virtual packages and maybe one industrial robot, so they will program on the virtual robot," Ramey said. "Then they take that program on a pendant and plug it into the robot and it will run. You also can have the virtual pendant on the computer, but the real training is that (hardware) teach pendant that controls everything."
Robot programming wish list
Ramey said he hopes to see the robot teach pendants get smaller like a PlayStation controller, and much easier to use. "Down the road, I see them going to even your basic cell phone and tablet to program robots."
He also would like a feature that he saw at IMTS 2016 in Chicago to become widespread. "Where you can just drag the end effector or end of the robot around and put your position points where you want them, and then it will remember those, instead of using XYZ coordinates and all the jogging coordinates," he said. "That will make things so much simpler. You actually can go in and grab the robot, show it what you want it to do and then tweak the program. That needs to become universal in all robots. A must is being able to plug the teach pendant right into the robot," he added, versus using a flash drive to transfer a program to the robot.
"I think the next generation of software will be able to reach a younger generation of students. I think all of the industry is looking at how to get more high school and junior high students involved. Schools are also pushing robotics down to the elementary level. The next wave of students will be more robot savvy than this generation, because years of experience and terminology will help them learn faster. Industry might have to catch up with the kids at that point."
RAMTEC hosted an event to celebrate Manufacturing Day on Oct. 13, 2016, including a facility tour, a robotics competition, and an industrial robotics contest. Ramey said students are thirsting for more real-world robotics applications experience, and he hopes that it will become an international competition.
The events also allow automation and robotics end users to scout and hire new recruits, which is what Honda did at RAMTEC’s National Robotics Challenge last April.
Thanks to a third round of Straight A grants totaling $6 million by the Ohio Department of Education, the RAMTEC concept is expected to be thriving in 23 locations by this fall. A larger pool of students will have opportunities for career development in advanced manufacturing and robotics, a big push toward tightening that skills gap.
Robotics university
Along the banks of the Hudson River, students also are readying themselves for a future in advanced manufacturing. Glenn Saunders is helping prepare the next generation of engineers and roboticists for the age of the intelligent factory.
Saunders is the senior research engineer in the Center for Automation Technologies and Systems (CATS) at Rensselaer Polytechnic Institute (RPI) in Troy, New York. He conducts applied research with an industry focus in robotics, automation, and manufacturing. The research work Saunders and his undergraduate and graduate students conduct often is motivated by a company with a specific need and usually falls into two areas.
"We like to say that we do research ‘in’ robotics, and we do research ‘with’ robots," Saunders said. "The research ‘in’ robotics is generally where we’re developing robots or we’re developing very research-like applications with industrial robots. Whereas in research ‘with’ robots, we don’t mess with the native controller, and we use all the tools that are available to the industrial customer. That’s really looking at a specific application for a robot, as opposed to trying to do new and interesting things with a robot."
RPI researchers and students work with a wide range of robotics platforms. They include a small Stäubli RX40 robot, two Adept Cobra robots, a Mitsubishi arm, a Yaskawa Motoman SDA dual-arm robot, three Baxter collaborative robots, a Universal Robots UR5 cobot, and a Barrett WAM arm.
"With the Adept robots, we’re using the Adept programming software and Adept vision software pretty much right out of the box," Saunders said. "That’s a case where we’re trying to discover whether we can solve a manufacturing problem with an industrial arm, versus reaching out into a whole new area where an industrial arm may not have been used before.
"For instance with the Yaskawa dual-arm, we’re using their high-speed controller and interfacing with it at a much lower level than the typical industrial customer," Saunders said.
"But it’s still an industrial robot. So in that case we’re making the robot system more intelligent. We’re issuing commands directly to the robot controller without using the teach pendant."
Saunders noted that this requires a deeper understanding of software programming than typically is used in the industrial world.
Advanced software programming for outer space
Saunders and his students are working with NASA’s Goddard Space Flight Center to explore the use of an industrial robot arm to repair satellites in space.
"These are satellites that have been in space for years, or decades in some cases, and they’ve reached their design life," Saunders said. "The question is whether you actually can service these satellites in space, which were never designed to be serviced at all, and get some additional life out of this very expensive asset, versus launching a whole new satellite."
The Yaskawa dual-arm robot (see Figure 3) is equipped with a Robotiq 3-Finger Adaptive Gripper and an ATI Force/Torque Sensor. A webcam is mounted on the arm that is used for tracking the space object. A visual tag provides position/orientation information to the robot.
"We are doing things like force control where we put a force sensor on the arm. The motion of the robot is in response to the forces that we’re experiencing at the force torque sensor, versus just point-to-point motion," Saunders said. "That’s both in the realm of research and industry, specifically force control. But we do it a little differently, because we need to simulate a zero-gravity condition (as in space)."
Simulation software on campus
Saunders said in many cases they just use the native programming that comes with the robot. That’s the case with their latest acquisition, an ABB Robotics IRB 6640 robot, which uses ABB’s RAPID programming language.
ABB also provided Rensselaer with 100 seats of its RobotStudio simulation and offline programming software (see figure 4), making it available to all the students on campus.
"That was a big part of our decision to make a purchase through ABB," Saunders said. "All of our students will have access to it (RobotStudio) and we’re very grateful for that."
Advanced offline programming and simulation software has been put to some unique tasks. Saunders said he’s very impressed with the software capabilities available within the industrial space. He cited one example where Rensselaer helped a company source an industrial robot.
"We have an external device, a press, and it will be ejecting a part along a certain vector, and so the robot needs to be able to access that load along that vector. We got quotes from four suppliers and every single one said, ‘Yep, we have a solution for that, it’s readily available.’ That surprised us. We thought it was going to be difficult, but everybody already had a solution. We were impressed with the sophistication of the industrial software."
Open-source software
On the more "researchy" side, as Saunders referred to it, a lot of what Rensselaer does is in robot operating software (ROS), which is an open-source robot operating system that recently celebrated its eight-year anniversary.
"We use ROS and we contribute to the open-source community within ROS," Saunders said. "The learning curve is quite steep. There are powerful capabilities, but it’s certainly not easy to use. Young people who are comfortable around a computer and the Linux operating system pick it up more easily.
"ROS has a lot of different software capabilities and one of them is visualization," he added. "It includes software that does things like path planning. The software will come up with a way to move the arm from point A to point B without crashing into things in the work envelope. It also includes software for mobile bases, which is beyond most of the industrial robots."
Rethink’s Baxter robot comes in an industrial version and a research version. Saunders said the difference is entirely in the software. "The Baxter Research Robot basically gives you access to a lot of the lower level functions that you would not normally have access to as an industrial customer," he said.
RPI researchers accessed those ROS-based lower level functions to develop a mobile in-home assistance robot. Most of the university’s applications for ROS open-source software have been on the purely research side. Rensselaer is looking to the future with membership in the ROS-Industrial Consortium, which extends the advanced capabilities of ROS to manufacturing automation and robotics.
"We operate in the industrial space. That’s why it was important for us to be members of the ROS-I Consortium," Saunders said. "We’re full members and have been for three years. Part of our mission is to help industry, and in particular New York state industry, to be more competitive. For us to do our jobs, we need to be in a position where we can advise our industrial clients on what’s coming down the road. We see ROS-I as having a pretty big impact on the capabilities of industrial robots and therefore the capabilities of our industrial partners. It’s really us looking forward."
Saunders said membership in the consortium provides insight into how the open-source software is used in research and various applications around the industrial world. Big names such as 3M, BMW, Boeing, Caterpillar, Ford, John Deere, and Siemens are members.
Other consortium members in the educational and research community such as the University of Texas at Austin Nuclear and Applied Robotics Group are exploring novel teleoperation applications that could be used for remote hazardous sites.
"We go to the meetings and we see the work that’s being done within the consortium at the other industrial facilities or industrial partners and that gives us a way to bring that information back to the companies we work with," Saunders said. "The primary benefit is being connected to the community."
Keeping the industry connected with the educational community will help bridge the skills gap. Preparing our current and future workforce for automation and robotics will span that divide.
Tanya M. Anandan is contributing editor for the Robotic Industries Association (RIA) and Robotics Online. RIA is a not-for-profit trade association dedicated to improving the regional, national and global competitiveness of the North American manufacturing and service sectors through robotics and related automation. This article originally appeared on the RIA website. The RIA is a part of the Association for Advancing Automation (A3). A3 is a CFE Media content partner. Edited by Chris Vavra, production editor, Control Engineering, CFE Media, [email protected].
MORE ADVICE
Key Concepts
Students are getting plenty of hands-on training and instruction from universities and using the latest developments to give them an edge as they graduate.
Universities are using open-source robot software to help students learn and gain additional knowledge from other companies.
Consider this
What other developments do you see happening in robotics regarding software development?
ONLINE extra
See additional stories about ROS and other robotics developments linked below.
For more information about upcoming A3 events including A3 Business Forum and Automate, visit: www.robotics.org.
See a related article about robotic telepresence linked below.