Electronic control components have evolved on a massive scale over the last 20 years, but many systems are much older than that and are classified as obsolete, which leaves the company with a challenge for future options.
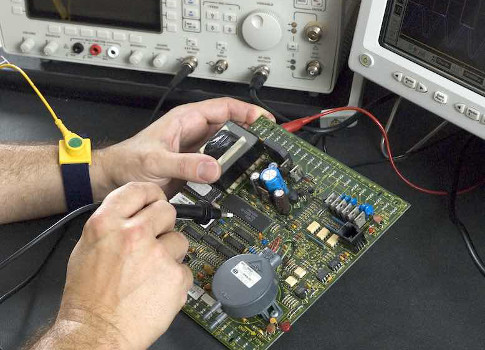
Industrial processes have relied on electronic controls for decades and as the technology has advanced, these controls have also become more complex and usually more compact. As competition in this sector has increased, some of the original equipment manufacturers (OEMs) have gone out of business leaving end users with some considerable challenges in the event of a failure.
Keeping proven systems operational
For many businesses, the easiest option is to replace the control equipment with a more modern equivalent that also offers new features, improved efficiency and takes up considerably less space. Although this may not always be the most cost efficient solution, the long term benefits and the improved availability of spares will reduce the total cost of ownership.
However, some industrial sectors, such as nuclear, military and oil and gas have very strict protocols regarding the replacement of components, meaning that retaining proven systems and keeping them operational is essential. In such situations, it is necessary to replicate existing components, ideally from existing drawings, but often with no reference material, which can prove to be quite a challenge.
Since programmable logic controllers (PLCs) took on the mainstream role of process control in the 1980s, the complexity, size and general design have changed immeasurably. However, some of this pioneering equipment is still in service and the end users need to have spare parts available in order to minimize any downtime. One failed card could potentially prevent a million pound machine from operating, so creating more spare parts is a proactive method of maintenance management.
Re-manufacturing often the best solution
This can be illustrated by a recent example from the oil and gas industry where the control system for a reciprocating compressor had failed and needed to be repaired at the earliest opportunity. The initial inspection showed that a multiple card failure had rendered the sequence control inoperative, the power supply card was missing and the components, such as the semiconductors dated back to the 1990s.
The scale of the challenge was increased by the fact that the OEM was no longer in business, leaving no spares and no replacement products, while the client needed the control panel back in service as soon as possible. In many applications a new controller could be created from modern components, offering more functionality, reliability and all from a more compact enclosure. However, as specifying new equipment for the oil & gas industry can be a very drawn out process, this meant the best solution would be to re-manufacture the electronic circuits, down to component level and to the original specification.
The repair process itself can be used to generate design drawings if they are unavailable, source obsolete semi-conductors and create test procedures for final testing. The complete reverse engineering procedure can replicate printed circuit boards (PCBs) and if necessary, hand drawing the complete circuit diagram for both design and future use.
In this case, once the new cards had been tested and installed the client requested additional spare cards to be manufactured as well as other cards to be remanufactured to ensure future availability of spare parts. In this way, any similar failures that occur can be resolved by the on-site maintenance engineers with a minimum of down time.
Similar situations arise in the nuclear industry as well as military applications where there is a requirement to prove functionality at the beginning, document the whole process and witness functionality at the end, before the new components are signed off and accepted.
In this way, applications that require obsolete electronics to be repaired or replaced can be effectively maintained using a preventative servicing regime. In addition, for those industries that allow, it is possible to incorporate more modern technology and software into existing control packages, increasing productivity and flexibility.
Brian Park, regional sales manager for Scotland, Sulzer. Edited by Chris Vavra, production editor, Control Engineering, CFE Media, [email protected].