No matter how long someone has been a part of the process automation industry; there is always something new to learn and new strategies to employ.
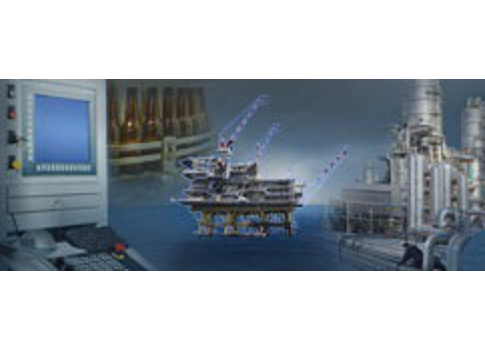
Earlier this year a colleague surprised me by complaining about needing to learn a new control system: “I’m 48 years old. I thought by this time in my life I would know all I needed to know about my profession.” What an amazing idea! That may be possible for some fields, but it’s not the case for process automation.
In process automation, something changes every day – maybe every second. OEM’s develop new platforms. New communications protocols come into vogue. New tools for creating and documenting control logic appear. New insights into potential safety hazards emerge. New, and probably undocumented, “features” of a system appear.
Working in process automation is rarely boring. It can be daunting, though, to be on a perpetual learning curve. Along with the plethora of control systems currently in use, process automation itself is a broad field. Many factors can impact how well or how poorly a control strategy works.
Having an understanding of field instrumentation, and its limitations, can be useful, especially since the manufacturers keep coming out with new versions of classic sensors, and completely new designs. End users may also need to do some historical research. It’s not unusual for a plant to have vintage 1970’s instruments still in service alongside the transmitter that was made last week. Even older equipment is not unheard of, pneumatics for example.
Aside from air powered instrumentation and controls, wiring issues will affect the control strategy. Awareness of common causes of electrical problems comes in handy.
Piping and vessel design and installation can also make or break a control strategy. A control valve that is installed backwards will not function as expected. Neither will a flow meter. Without a sufficient upstream straight line run of pipe, some flow meters will give unreliable readings. And there are other considerations. Is the vessel size appropriate for its throughput, or are we trying to control the level in a very small tank with a very large flow into it?
Then there’s the material in the pipes and vessels. Are we dealing with clean liquid service or corrosive slurry service? Will the liquid freeze, and plug everything, at temperatures below 60 F? Every different process is challenging in its own way. Understanding the process is crucial to creating good control strategies.
It can be frustrating and humbling to recognize how much there is to know, and how impossible it is to know it all. Experience, however, is cumulative.
Having a good understanding of one platform is a great springboard to learning another one. It’s like learning another language. Whether DCS or PLC, similar programming structures are used for similar operations. Having experience with several platforms improves your ability to “guess right” when unsure of the approach to use.
What you’ve learned, particularly if you’ve struggled to learn it, is retained. The knowledge may be stored in some obscure little box in your brain. But once you need to use it again, it’s amazing how quickly it comes back out.
Here’s a good quote for the ever changing world of process automation: “If you’re resting on your laurels, you’re wearing them in the wrong place.” Where are you wearing your process automation laurels?
This post was written by Mayann Stroup. Mayann is a senior engineer at MAVERICK Technologies, a leading automation solutions provider offering industrial automation, strategic manufacturing, and enterprise integration services for the process industries. MAVERICK delivers expertise and consulting in a wide variety of areas including industrial automation controls, distributed control systems, manufacturing execution systems, operational strategy, business process optimization and more.
MAVERICK Technologies is a CSIA member as of 3/20/2015