Compressed air is very common in all industrial facilities and there has been a major push to identify machine and plant air leaks in an attempt to reduce power costs.
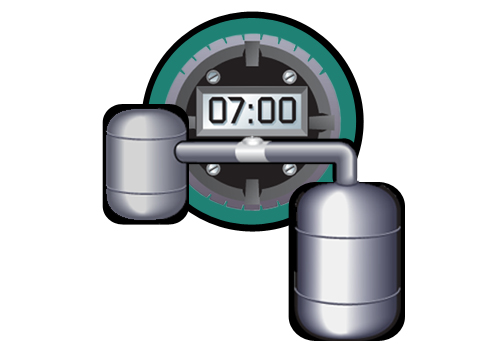
Compressed air flow applications are by far the most popular request I receive, followed by natural gas measurement. Compressed air is very common in all industrial facilities and there has been a major push to identify machine and plant air leaks in an attempt to reduce power costs. There is a rule of thumb that most engineers are familiar with that goes something like "a 1/4" leak at 100 psig costs approximately $10,000 per year."
Whether that number is completely accurate or not, it is true that centrifugal air compressors are high energy consumers and are constantly in operation. As a result, knowing your compressed air flow usage throughout the plant is a good start in identifying whether you have a leak or if your compressors are in need of maintenance.
Thermal mass meters can be your detectives
When I am approached by engineers or facility personnel for flow measurement suggestions, they generally have a very good feel for the duct work and branches of the compressed air system. The usual approach for many of them is to place metering after the compressor air dryers and use that as their base production number (call it the main compressor manifold meter). Then, they add various other meters throughout the duct network and subtract those readings from the main compressor manifold meter. Ideally, the net result should be very near to zero which would indicate a complete accounting of air produced and air consumed.
If the numbers don’t agree, then you can start your detective work and find out which branch is misbehaving and take corrective action.
Aging machinery and characterization
Another popular use of thermal mass meters in compressed air is the characterization or baselining of rotary equipment during installation or at repair intervals. If you have thermal mass meters in place on a set of compressors, you can establish normal baseline behavior of these via data acquisition. One powerful use of thermal mass meter data is that you can take today’s behavior of a compressor system and compare it to its behavior last month, last year, or the last time you repaired the unit. Once you have a good steady set of data, you can tell at a glance if air consumption is out of normal operating range in your plant.
Applying thermal mass meters in challenging piping layouts
Once you have made the decision to install thermal mass meters, you will want to select the best location to insure good accuracy from your readings. Sadly, many existing pipe installations do not provide ideal locations for the successful installation of a thermal mass meter. We generally recommend 15 upstream pipe diameters and 5 downstream pipe diameters for normal straight run requirements. However, any elbows, reducers, valves, etc. will require a longer straight run up to 40 pipe diameters in extreme cases. Thankfully, there is a solution to this problem called flow conditioning. To address the fluid dynamics behind flow conditioning, you need to visualize the boundary layer and flow profile of air inside a pipe.
Thermal mass meters are designed to read gas velocity at the point of fully developed flow which is located in the center of the pipe. Some people mistakenly suggest that thermal mass meters don’t like turbulence, but the opposite is actually true. Thermal mass meters need turbulence, but it has to be fully developed or else the velocity profile of the gas stream will be uneven and the meter will not register the correct mass flow. Going around corners and elbows creates flow disturbances that break up the bullet shape required for fully developed flow. Now that we understand the velocity profile requirements of the thermal mass meter, how do we fix the profile if we don’t have the recommended straight run? The answer is flow conditioning.
Installation considerations of flow conditioners
Now that we have a good grasp as to why we need fully developed flow, let’s say you have a site where you want to install a thermal mass meter that doesn’t meet the recommended straight run requirements.
The solution for such a situation is an inline flow conditioner that looks like two mesh plates separated by three standoffs. Despite its somewhat simple appearance, there is a good deal of engineering that goes into the design of flow conditioners. But, the truth is that you don’t really need to know any of that to successfully apply them in your piping. Since flow conditioners require you to insert them into a pipe spool piece, you will be required to cut the existing pipe section upstream of the meter. The good news is that you can now have as few as three pipe diameters upstream of the meter and still achieve factory rated accuracy.
Jim Bowser is a mechanical engineer out of Georgia Tech and has been with Cross Company Integrated Systems Group since 2008. Jim has over 20 years of experience in the motion control and process control industries in both sales and integration roles. He has successfully implemented projects in the pharmaceutical, specialty chemical, power, automotive, and water/wastewater industries.
Cross Company Integrated Systems Group is a CSIA member as of 3/5/2015