Xaba will use the new capital from Hitachi Ventures to accelerate its 'Open AI for Industrial Automation' platform.
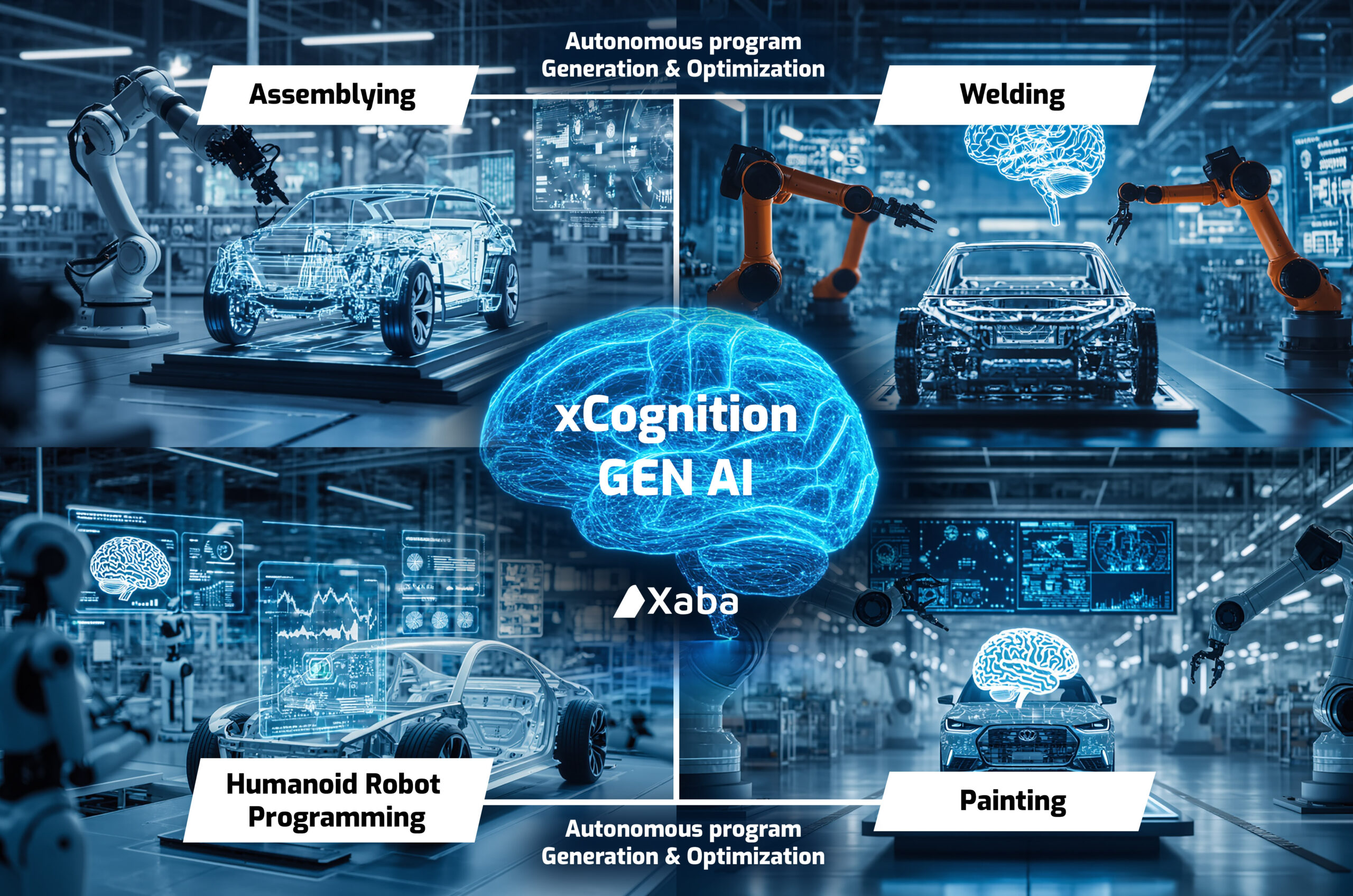
Xaba has secured a $6 million seed extension to support the continued development and deployment of AI-powered robotics and industrial control technologies. The round was led by Hitachi Ventures with participation from Hazelview Ventures, BDC Capital, Exposition Ventures, and Impact Venture Capital.
Many industrial automation systems continue to rely on traditional controllers and programming approaches, which often require manual configuration. Programming and deploying industrial robots costs the industry an estimated $7 billion annually, with a significant portion of automation expenses related to manually developing logic for industrial controllers.
Xaba’s Generative Industrial AI platform is designed to reduce the need for manual programming in industrial automation. Its core system, Xaba xCognition, automates elements of robot programming and machine logic development for a variety of predefined tasks. The platform generates part-programs and all the programmable logic controller (PLC) code required to operate compatible machines. This approach enables users to convert basic instructions into executable machine operations, streamlining deployment and reducing engineering time.
“Traditional robotics systems require extensive programming, constant human supervision, and struggle with real-world variability, in geometry, process parameters, materials, and actual production KPIs,” said Massimiliano Moruzzi, CEO of Xaba. “We’re redefining automation by enabling robots and machines to self-optimize and execute complex tasks with minimal programming.”
Meet Xaba: the first truly autonomous AI control system for industrial automation
Using Xaba, manufacturers can input automation goals, production KPIs, or operational tasks in plain text or functional specifications. The system’s tools, xCognition and Xaba PLCfy, then generate the necessary code to operate robots and production lines. This supports quicker setup, reduced downtime, and improved adaptability in industrial automation through:
- Physics-informed machine learning model: It models real-world environments using machine learning and can adjust to various machines and motion platforms to support real-time system tuning.
- Robotics and PLC AI code generation: The AI models generate robotic programs and PLC code based on operational workflows and machine logic, helping reduce deployment time and manual coding efforts.
- Real-time process learning module: Using data ontology and graph neural networks (GNNs), the module identifies and maps relationships between machines, sensors, and processes to support system adjustments and ongoing performance improvements.
- Cognitive control framework: An AI platform designed to integrate with various robotic systems, CNC machines, or PLC controllers, including legacy and modern equipment.
“Industry 4.0 promised intelligent, autonomous factories—but it’s often been stuck in pilot purgatory, held back by rigid, code-heavy systems and legacy infrastructure,” said Gayathri Radhakrishnan, partner at Hitachi Ventures. “By giving industrial machines the ability to self-learn and self-program through generative AI, Xaba is turning the vision of smart manufacturing into a scalable, reality today.”
Xaba’s AI is being used in aerospace, automotive, and precision manufacturing to help reduce rework and manual adjustments:
- Automotive manufacturing: Xaba’s AI is used in aluminum casting and forging to help robots machine metallic castings more accurately while accounting for machining tolerances, contributing to lower assembly costs, less rework, and reduced production time.
- Large-scale robotic drilling: Some manufacturers have reported increased production rates and reduced capital expenditures. Unlike traditional systems that depend on fixed programming and manual adjustments, Xaba’s AI helps robots adapt to different parts and processes with less downtime.
- Robotic welding: Xaba’s AI supports the automation of MIG (Metal Inert Gas) and TIG (Tungsten Inert Gas) welding, as well as laser welding, helping maintain consistent output across production lines and contributing to shorter production timelines.
- Large-scale 3D printing: Xaba’s xTrude system supports fused deposition modeling (FDM) by helping prevent issues such as delamination, collapse, and distortion. It enables manufacturers to adjust print parameters in real-time, improving consistency and reducing material waste.
Edited by Puja Mitra, WTWH Media, for Control Engineering, from a Xaba news release.