MOL Danube Refinery near Budapest, Hungary, says it is committed to the operation of a predictive maintenance system. In developing this long-term strategy the application of devices based on HART technology plays a major role. HART Communication Foundation named the refinery the 2010 HART Plant of the Year. See tables, photos, graphics, links to prior winners, and more.
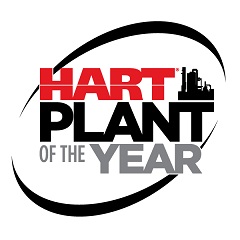
Prior to HART diagnostics at MOL Danube Refinery, about 60% of control valves were selected for repair; now it has fallen to about 5%. By avoiding the need to remove failure-free control valves, the maintenance department estimates the company saves an average of $73,843 per unit during one shutdown. Extensive use of HART communications within an operations and maintenance strategy earned the MOL Danube Refinery the 2010 HART Plant of the Year Award. (Link to articles about prior HART Plant of the Year winners below, and see photos about this plant, along with a case study example and charts and tables showing alarm management and other trends at MOL Danube Refinery.)
Beginning in 2003, the refinery’s instrumentation and electrical department made two major decisions, says Gábor Bereznei, who heads the group, near Budapest, Hungary. First, the department decided to purchase only analog field instruments that support the HART Communication Protocol.
Since most industrial field instruments manufactured today are equipped with HART electronics—and usually carry no or a very small premium price for this communications capability—this was a fairly straightforward choice. Companies in many other industries have done the same. Today there are more than 30 million HART-capable devices installed worldwide.
The second decision was more strategic: The MOL Group issued an internal directive to encourage its engineering departments to develop and use the in-depth and sophisticated communication options embedded in the HART instruments.
Overwhelmingly, the greatest number of HART instruments communicate directly with handheld devices, such as Emerson’s popular 375 HART Communicator. In fact, it’s part of the plant welcoming ceremony: when the instruments arrive at the factory and are taken out of the box, they are connected with such a device for their initial setup and calibration.
For millions of HART devices, this is the first and last time they engage their communications in a digital HART conversation. After this, the device is sent off somewhere in a manufacturing plant, never to communicate again—unless a technician takes the handheld into the field, where the instrument is installed, to do some maintenance work on it a year or two later. And then, once again for a few moments, its HART electronic circuits communicate using its protocol with the handheld interrogator. Then it goes silent again.
That’s underutilizing a valuable asset, decided Bereznei. HART electronics embedded in the instrument enable it to communicate over its 4-20 mA signal line, which is the standard pair of twisted wires that connect it with the control system. These HART digital signals contain a rich set of valuable diagnostic information that can enable engineers to monitor equipment health on the factory floor. Much like heart monitors in a hospital connected to a central nursing station allow technicians to keep an eye on dozens of patients, HART monitors in plant equipment allow factory technicians to see what is happening in the equipment on the floor of their plants.
“Let’s get connected and put these HART instruments to work,” said Bereznei, and this became the instrumentation and electrical department’s directive. Today at the Danube Refinery there are more than 30,000 HART instruments installed and engineers have connected 3,707 of them—mostly the valves and instruments in critical control loops—directly into computerized maintenance management systems (CMMS). Most (2,874) are in an Emerson asset management systems (AMS) that uses ValveLink software for diagnosis. (There are another 437 instruments in this system connected via a Foundation Fieldbus network.) Another 833 instruments are similarly connected in Yokogawa plant asset management systems.
The MOL Danube uses MTL and Pepperl+Fuchs multiplexers to connect the HART-based instruments to its control systems, which are mostly supplied by Honeywell and Yokogawa.
Beyond these 3,707 instruments, all HART instruments in the refinery are in the database of the AMS calibration support system. Where there is no electronic maintenance program, field diagnostics is performed using handheld communicators. Used daily, these instruments are used to reconfigure the field devices’ measurement range, detection of communication defects, and changing the configuration. Conveniently, the communicators can be connected to the signal wires at any point in the control loop, which means the technician only needs to go to the control cabinets. This usually saves the technicians from going into remote and possibly dangerous areas of the plant.
MOL Danube developed a two-way connection between AMS and the Enterprise Resource Planning (ERP) systems, SAP. SAP has its own preventive maintenance software, SAP-PM.
Separate homegrown systems
Maintenance systems have been used in refineries for a long time, and by the late 1990s, MOL Danube had its own homegrown version in place. Initially, there were separate computer systems for the various maintenance systems, but in 2005 a project was launched to combine and expand these systems.
During the amalgamation project, centralized systems were developed in a client/server architecture. The objective of the project was to develop a standard maintenance strategy, so systems would operate according to a strategy developed in a uniform way, rather than in isolated islands.
Plant maintenance managers set the following goals:
- Create an online analysis, transmitter, and assembly diagnostics system
- Create a laboratory and field calibration support system
- Automatically forward measurement results and diagnostics alerts to the ERP system, specifically the SAP-PM system
- Improve plants’ availability and cut maintenance costs, and
- Reinforce CAPEX (capital expenditure) project support to apply “appropriate assets to the appropriate place.”
HART Communications
Connecting 3,707 instruments into an on-line diagnostics system has changed the way the MOL maintenance department operates. On-line device diagnostics—signals coming from field instruments to the plant maintenance and control systems—makes it possible to prevent plant shutdowns and slowdowns. It does this by allowing the engineers to detect small problems that are growing over time. Plant shutdowns caused by eventual asset failures can be avoided.
The system works so well and has proved to be so beneficial the company has set up a separate unit to operate the applications and systems. The main task of three engineers involves monitoring asset defects and carrying out any necessary repairs. They are called the FIMS team, where FIMS means field instrumentation management system.
The FIMS team has learned that, using supplementary information provided by HART communication, field devices can post a large number of diagnostic reports concerning their operation. Based on this information, it is easy to determine the type of actual breakdown and the method of repair.
The team also developed a statistical application to follow up HART alerts sent by AMS to the CMMS, and CMMS work orders received by AMS. Using this application they can evaluate the mean time before failure (MTBF) and most frequent instrument failures.
“This allows the targeted repair of assets, which, in turn, enables us to save time and dispense with unnecessary parts procurement,” said Bereznei. Maintenance performed subject to an accurate technical scope and in a timely manner reduces the number of breakdown events and the duration of downtimes.
Alarm management at Danube Refinery – the dark bars above show valve position alarms; the lighter bars are transmitter alarms for January-November 2010, from the AMS to SAP systems. This is the HART Plant of the Year for 2010.
Asset types and number at Danube Refinery – each set of three bars shows online, offline, and summary of asset of that type at various areas of the plant. Most online assets, nearly 1,000, are in the Gasoil Hydrotreating 3 area. This is the HART Plant of the Year for 2010.
Percentage of connected assets at Danube Refinery – area on bottom of bars shows percentage of connected assets to the AMS and PRM systems and third bar (right) shows summary. AMS system has most connected assets, nearly 80%. This is the HART Plant of the Year for 2010.
Table of assets at Danube Refinery by asset area, showing online, offline, client, percentage connected, and related distributed control system vendor, Honeywell, Emerson, or Yokogawa. This is the HART Plant of the Year for 2010.
Online and offline assets at Danube Refinery for the asset management – 63% are online. This is the HART Plant of the Year for 2010.
The alarm management system for devices was developed for more efficient operation in this area. Staff engineers examined the various devices according to type and manufacturer, and set priorities for device alarms provided by HART communication according to severity. The objective of this system is to have only those alarms forwarded to the enterprise resources planning system (SAP), which require physical intervention at any given asset.
Priority is also the principle for grouping alarms by severity. The engineers put the alarms into two general groups: alarms associated with actual defects, and alarms serving to prevent actual defects.
This makes the implementation of preventive maintenance possible, which results in substantial cost-saving. The fundamental notion is that it is always less expensive to eliminate a defect as it develops than to purchase new assets to replace malfunctioning ones.
More stable operation
On-line diagnostics provided by the HART instruments does something more than preventive maintenance, according to József Bartók, automation engineer at MOL Danube. “It ensures the stable operation of the system and increases the precision of control.” This is an aspect of the technology that comes directly to the bottom line, increasing the profit generating capability of the unit.
The instrumentation and electrical department team learned that the loss of profit arising from inaccurate control is easily recaptured using HART technology.
“In a given unit, the inaccuracy of the loops controlling the applied separation processes—which can typically be traced back to the de-tuning of the control valves—could not be identified without the use of intelligent valve positioners supporting HART technology,” says Bartók. “With the application of this technology, valve failures can be screened out and the corresponding loss can be minimized by repeated calibration.”
Commissioning, shutdowns
HART-enabled instruments help streamline installation and commissioning of control loops, because newly installed transmitters can be checked without “driving” them with the 4-20 mA signal in the field. Engineers say that, thanks to this option, they generally spend 20% less time in commissioning. The AMS stores all results automatically.
HART-enabled diagnostics has another important role during the maintenance shutdown every four years. This is a good time to remove troublesome valves from the system and have them repaired or replaced. Obviously, such a large-scale event is very costly and requires a great deal of advance planning.
The perplexing question facing engineers at shutdown time is “which valves should be removed for additional work?” The labor is so costly that decisions must be made with high confidence.
In the past, without the benefit of HART communication and computerized maintenance systems, the only way to make these decisions was on the basis of old-fashioned operating experience. While defective valves usually got discovered and repaired, some valves were dismounted that required no repair. Before HART diagnostics, about 60% of control valves were selected for repair; now it is about 5%. By avoiding the need to remove failure-free control valves, the maintenance department estimates the company saves an average of $73,843 per unit during one shutdown.
HART technology is widely used in other areas of the plant, such as in the calibration laboratory. Calibration data are automatically recorded in an AMS computer, which generates test reports and certificates in electronic format, which are transferred to the SAP-PM system. The company has performed nearly 3,000 instrument calibrations and has acquired an extensive database on its transmitters.
Wireless next?
WirelessHART transmitters may be the next big thing. MOL has equipped two units with WirelessHART instruments (four temperature transmitters and five control valve positioners with Wireless extender [adapter], plus one gateway). These are integrated into the plant maintenance system. Easier-to-connect instruments promise to add benefits for large-scale process operations.
Predictive, proactive
“Our company is committed to the operation of a predictive and proactive maintenance system,” says Bartók, “and in view of realizing these objectives, in the refining long-term maintenance strategy the use and development of maintenance systems, and the application of devices based on HART technology play an important role.”
HART technology is widely used at MOL Danube, off-line and on-line, for carrying out daily maintenance tasks. “It provides a lot of help, making our maintenance processes faster and more efficient,” says Bartók.
“Our company is committed regarding the use of this technology. We intend to leverage the benefits it provides to the greatest degree possible. MOL Group is committed to disseminating and utilizing the benefits the HART Standard provides in the broadest possible scope, and this includes the other refineries in the MOL Group.”
Award details
The HART Plant of the Year Award is given annually by the HART Communication Foundation to recognize the people, companies, and plant sites around the world that are using the advanced capabilities of HART communication in real-time applications to improve operations, lower costs, and increase availability.
When Bartók was asked how he would describe the benefits he has seen from using HART communication, he selected the words “availability and available,” indicating that for MOL HART communication contributes to increased plant availability, the availability of critical information for field devices, and the availability of standardized information available in the system. Availability has helped MOL Danube Refinery achieve its objectives.
For more information, see
Example case study: Gas oil hydrotreater
K-803 tower KFV8017 head pressure control valve was very slow in motion, and this was causing a serious effect on the control loop. The managers of the unit assumed it was a stuck valve and ordered it removed for repair. Unfortunately for the service technicians, the bypass valve wasn’t good enough to isolate the stuck valve so they had to take a different approach.
By using on-line diagnostic tools, the technicians made further investigations into the intelligent positioner in the valve, and as a result concluded the valve was in good condition, but the current-to-pneumatic (I/P) part of the intelligent positioner was damaged. The unit operational staff put the valve in manual and, after half an hour of instrumentation work, eliminated the problematic item.
Thus, removal of the valve was avoided, which saved the company two days of unscheduled downtime (a minimum time estimate) which would have a projected cost of $861,504.
Prior HART Plant of the Year winner articles
HART 2009 Plant of the Year – Exclusive: First ethylene plant for Mitsubishi Chemical Corp. is the HART 2009 Plant of the Year. HART technology helped detect onset of a plugged impulse line and plugged manifold during startup, reducing maintenance costs and startup time. An unscheduled shutdown would have cost an estimated $3 million.
2008 HART Plant of the Year: Heavy crude upgrader in Venezuela – One of Venezuela’s major oil fields lies in its Orinoco River basin; however, crude from this field is extra-heavy and must undergo upgrading in one of several plants before refining. One of those plants, the Petropiar Mejorador (upgrader) in the José Antonio Anzoátegui industrial complex near Barcelona, Anzoátegui, Venezuela, has been named the 2008 HART Plant of the Year.
2007 HART Plant of the Year – HART Helps Keep the Heat On – When winter strikes, you need heat to beat back the cold, and it’s best when the fuel is reliable, plentiful, and relatively clean burning. This year, consumers in the U.K. have a new source for that heat, natural gas and condensate pumped across the ocean from Norway’s undersea Ormen Lange gas field.
2006 HART Plant of the Year: Digital Output – Just as all roads once led to Rome, today all pipelines lead to Fort Saskatchewan – at least those carrying hydrocarbons in the middle of Canada’s oil-rich Alberta province. The pipeline hub is the BP Canada plant located in the city.
Sasol Wins 2005 HART Plant of the Year Award – Handed the task of overseeing the implementation of communication and control systems that would serve as the automation data lifeline for two new plants, Johan Claassen, engineering manager for control systems, instrumentation, and electrical, started small but finished big. The plants, to be constructed by South Africa’s Sasol Solvents and Olefins and Surfactants, housed some 10,000 I/O points.