Companies are entering a new revolution that changes the way original equipment manufacturers (OEMs) approach manufacturing with the rise of artificial intelligence (AI).
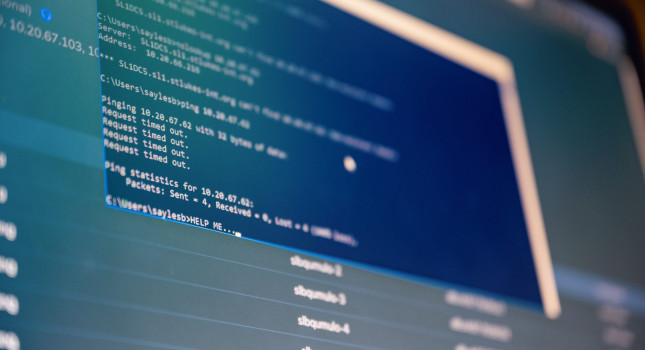
Artificial intelligence (AI) insights
- The rise of artificial intelligence (AI) has companies are entering a new revolution that changes the way original equipment manufacturers (OEMs) think about and approach manufacturing.
- While AI’s role is growing, many companies are struggling to find out what, exactly, that role is and how it can help companies. It’s been a growing challenge and will continue to be at the forefront, particularly as it becomes more mainstream in a general sense.
The industrial revolution has been a key driver of efficiency across industrial manufacturing over the last century. However, with the increasing digitalization of industrial equipment and the rise of artificial intelligence (AI) in the shop and on the factory floor, companies are entering a new revolution that changes the way original equipment manufacturers (OEMs) think about and approach manufacturing.
Siemens, for instance, uses AI to improve the operational efficiency and product quality of its machines. The savings in both time and resources has been significant.
“There’s a lot of data already available from machines without the need for additional sensors,” said Bernd Raithel, director of marketing/product management at Siemens.
Normally, this data is thrown away. However, it can be collected at a relatively low cost. “At one of our sites, we collected 11 million data sets, each with 40,000 data points for each component,” Raithel said. “With this data, we have begun to implement effective predictive maintenance. Predictive maintenance increases the lifetime of our machines by monitoring operations to assess and identify potential failures. A planned maintenance shutdown predicted by AI could prevent a breakdown of the production line at 3 am. That’s a 15-minute loss of production compared to hours.”
“Another way AI saves us time and expense while improving quality is by predicting if a particular part will meet quality requirements early in the production process. Printed circuit boards (PCBs) are so highly integrated, an X-ray is needed to assess their quality. Our X-ray machine cost $500K. We can improve throughput and eliminate the X-ray as a bottleneck by assessing which parts are at risk to fail and apply testing resources appropriately. We are able to identify good parts upfront so we can apply more thorough testing only to the parts at risk.”
For Siemens, these early fault assessments have allowed the company to perform 30% fewer X-ray tests, have a 100% quality rate, and reduce capital investment by $555,000. Where testing is a bottleneck, this also increases overall throughput of the production line. And the savings don’t stop here. “With this data,” Raithel said, “we learn not just which parts are defective but the why, the source of the defect. We then carry this information back to the product line and further improve quality. “Of course, not everyone needs 40,000 data points for one component. That said, my advice is to collect the data you can capture even before you know what to do with it. Then, when you have a problem, figure out which data points are relevant. With the data in hand, you can create an AI model to identify the problem. But if you don’t collect the data, you won’t ever know what you can do with it.”
The added value of AI in manufacturing
While Siemens is seeing great success using AI, many OEMs still have questions about AI’s value They believe they already have productive, efficient factories in place, so where does AI fit in?
Indranil Sircar, CTO, manufacturing industry at Microsoft, said, “You can’t think of AI as a standalone technology. It is not a ‘magic’ function but rather a way of working. AI scales from a single machine and extends across the entire manufacturing production line and supply chain. It revolutionizes manufacturing by extending the level of details we focus on.
“Our experience shows that implementation of agile factories typically occurs in three phases that starts with connecting the factory to gain visibility. AI plays a role in contextualizing the ingested data and creating a digital twin of the factory. In the next phase, data is used to analyze causes and impacts. This data also predicts what happens when using AI, machine learning (ML) and simulation to improve productivity. In the third phase, the shift is more toward prescriptive capabilities driving optimized operation and leading to autonomous systems.”
Here are just a few of the advanced capabilities AI enables:
-
Detect quality defects through image recognition and other parameters
-
Automatically control high speed processes for maximum output, minimum downtown and reduction in part failure
-
Automation of machine calibration and tuning to significantly accelerate manual processes with operator-level precision.
-
Automatically adapt industrial robots/collaborative robots to changing location using image recognition
-
Produce automated recommendations to help operators in highly complex, fast-paced processes
-
Dynamically optimize autonomous mobile robots (AMR) for material movements and warehouse utilization.
AI eliminates uncertainty and helps manufacturers understand risk
Irene Petrick, Sr. director of industrial innovation at Intel, is passionate about AI. “One of the shifts AI is bringing about is the scope of what we mean by efficiency. One element of efficiency is to eliminate uncertainty. For example, there is uncertainty as to whether a product meets minimum standards at the end of the production line. With AI, we can identify which products are more likely to be at risk of defect. This removes uncertainty and makes for more efficient testing. Reliability increases from an awareness of where our uncertainty is. The better we know the factory floor, the more efficient we can direct operations, from the individual machine all the way up through the supply line.”
AI provides visibility and insight into areas where an OEM might currently feel a complete lack of control. With this insight, OEMs can make better predictions in areas they previously didn’t even have visibility into. In short, AI reduces uncertainty.” Petrick said. “With the digital transformation of industrial equipment, machines produce a tremendous amount of data. Today, much of this data is ignored. However, when this data is collected and analyzed by AI, OEMs can gain deep visibility into their operations.”
The first step is to collect and gain visibility to dark data. AI can then assess and analyze the data to increase efficiency, make useful predictions and provide insights into how to further improve quality and reliability. AI also helps eliminates blind spots OEMs don’t even know they have, reducing uncertainty and providing a better understanding of the actual production risks involved.
Petrick said, “We collect data from multiple sources – including lidar, acoustic sensors and cameras – and use data fusion tools to analyze this data together. For example, we’re making huge strides around visual detection, surveillance and facial recognition. These technologies can be used in manufacturing to identify existing defects or, with AI, to identify product characteristics that tend to lead to defects further down the production line.”
This is known as a feedforward loop. In a standard production line, each part is checked and tested at the end of the line. If a painting flaw is identified, the part is failed, dropping yield. In addition, the part needs special handling to identify the flaw and fix it. Consider painting flaws caused by a weld flaw (cosmetic, not structural). If the weld flaw can be identified at the welding station, the part could be flagged to receive special handling at the painting station that accommodates the weld flaw and makes proper adjustments so the part passes testing. Instead of treating each individual stage as independent, each stage of the production line is recognized as dependent upon the others. Thus, new levels of productivity can be achieved.
AI collaboration with the workforce
John Karigiannis, technology manager, artificial intelligence and computer vision at GE Research, said, “Often the first place to introduce AI is where it can have the greatest impact, typically where you have the greatest risk,” Karigiannis said, “For many OEMs, this is the inspection and testing of parts. AI-driven inspection is more consistent than human-based inspection because the AI doesn’t get tired and can’t cut corners.”
At a high level, AI is about enhancing people’s skills and enabling them to leverage insights that might require terabytes of data to uncover. AI overcomes the limitations of human perception. By collaborating with AI, people can monitor more operations, bringing their flexible focus and capabilities to the areas that are too complex or have too much variation for AI models to capture. Collaboration optimizes the value people bring to the floor by extending their visibility and control.
Raithel said, “There’s a misconception that AI just teaches itself. Usually, you need an expert to teach an AI. With AI handling tasks on the production line, you can now focus your experts on teaching the AI what it needs to do. It’s a multiplier effect. One expert can now apply their expertise across many more parts with greater accuracy and consistency.”
People are a necessary part of an AI-based production line. “The AI process works within boundaries,” Karigiannis said. “You need a person to operate outside these boundaries. For example, there may be out of distribution features for an AI algorithm to determine whether a part is defective. However, the AI can still identify distress, corrosion or other telling factors, assuming it has had sufficient data to train with. The AI might not be able to say, ‘This is a crack’ but it can say, ‘There’s likely a problem here.’ Now, instead of a human inspector looking at 1000 parts, AI identifies the 10 parts that are most likely defective. Put another way, AI makes it possible to say, ‘I am confident there is no defect in these 990 parts.’”
AI can also enhance personnel and accelerate their learning. For example, National Oilwell Varco (NOV) has used Microsoft autonomous systems to develop an “AI coach” to grow and improve their workforce. Previously, new hires required at least six months of training to learn how to operate equipment. With the AI coach, NOV expects new hires to need less than half that amount of time. In addition, more experienced operators are freed up from training to focus on running critical machinery.
The shift back towards complexity and variation
Petrick said, “One major trend we see in the evolution of AI is a shift from consistency to variation. A common automation strategy is to remove variation from the assembly line. While this has removed uncertainty, it has given OEMs a false sense of comfort about what they think they can control. We think we can control all aspects of production. In some respects, the more a production line is simplified and made consistent, the lower its resiliency to variance. As we’ve learned from COVID, we can’t assume the past is a good predictor of the future. Instead, we must assume that we can’t control every factor and circumstance.”
In a similar way to how AI can enhance human workers, AI can enhance robots by handling variances the robot has not been programmed to address. This second layer of AI enables us to keep robots simpler and more consistent while expanding the use cases and applications in which they can be used. Handling greater complexity is where digital twins come into play. Digital twins use AI to simulate a robotic cell or even an entire factory floor. If you have enough data of the physical world, you can simulate what day-to-day operations will be like so you can optimize for them. However, you can also simulate variances and disruptions. This allows you to see the impact on your production line and assess how resilient it is. You can also begin to develop strategies to address potential disruptions to minimize their impact.
Karigiannis said, “Rather than manually program every task for a robot, robots can train in a simulated environment. Once they learn what to do, they can be transitioned to reality.” Ultimately, a robot can learn to move safely across a factory floor without colliding into other objects.
Simulation is valuable even for complex tasks such as welding where there might be a lot of variation. The simulation provides enough of a foundation to help a person complete programming of the task more quickly. “For us,” Karigiannis said, “AI removes 80 hours of manual robot programming.”
The vision Sircar paints for AI goes far beyond robots moving parts on an assembly line. Sircar’s vision includes the Metaverse where a virtual reality is used to optimize by modeling the real-world and finding ways to interact within the factory in entirely new ways. “With the foundation of a Digital Twin and AI, manufacturers are now able to visualize the factory in near real-time. In addition to tracking the past, they can analyze, predict, simulate and interact operations in a mixed reality environment,” Sircar said.
From machine to factory floor to supply line
Digital twins provide the most value at the system level. Analysis at the machine level is limited in scope and doesn’t capture system-wide effects. The more complex the overall system is, the more system effects amplify when they occur. With a digital twin, it becomes possible to simulate an entire factory. Now, rather than using AI just to optimize cutting path or robotic assembly at a single station, the entire production line and the interdependencies between each stage can be optimized.
These insights can extend outside the factory as well, so long as you have access to the relevant data. OEMs can analyze components coming in and how they move through the factory. At a simple level, AI can identify bottlenecks in component fulfillment. At a higher level, AI can make predictions about the supply line. The supply line is harder to predict because you might not have enough data about your suppliers. The time is coming, however, when your customers may ask for detailed production line information from you so they can predict deliveries on time.
Petrick said, “In just two years, we’ve seen a major shift in the scope of impact for the major challenges manufacturers face. Now there’s less focus at the individual/team level and a greater need to address issues out to a wider company/industry perspective.”
Given the supply chain challenges seen during COVID, the ability to guarantee delivery is likely to become a significant differentiating factor in the market. COVID has been one of the largest disruptions many companies have experienced. To protect their operations, it only makes sense that OEMs extend AI beyond machine-level interactions out onto the factory floor and into the supply chain itself.
The human factor: Trust
A final piece of the AI puzzle OEMs need to consider is the human factor. Petrick said, “AI is just a model that produces a recommendation. This recommendation is only useful if it drives actions. And that highlights a cornerstone of AI: Trust. Because as soon as you put a person in the loop, trust must be considered. For if the humans working with AI don’t trust its recommendations, the AI won’t necessarily improve efficiency, quality or reliability.”
To see the truth of this, consider autonomous cars. If people don’t trust that the car can safely drive them home from work, they won’t get in it. To address this, Petrick said, “The industry needs to be transparent about AI. We must be able to explain what it is, what data we are using, how the algorithm processes the data, and how it arrives at its outcomes. And, we have to do this in plain language that the people on the factory floor understand so they can have confidence and trust in the AIs they work with.”
AI’s future in manufacturing
AI is powerful technology that enhances people, skills and workflows. With AI, OEMs can improve individual machine performance as well as optimize operations across the entire factory floor and across the supply chain. AI makes it possible bring complexity and variation back into the production line without losing the benefits of automation. OEMs can increase product quality while lowering testing and production costs. AI also facilitates a higher level of collaboration between human and machine. And you don’t need to plan separately for sustainability, for when you improve efficiency and optimize operations, you automatically reduce power consumption and other waste.
It’s important to note that the trends and impact of AI on industrial manufacturing vary depending on where your operations are located. Not every part of the world is dealing with a “labor shortage” and trained workforce issues differ greatly between the US, Europe and Asia. While AI technology is evolving at an amazing pace, it also becomes more accessible each year.
Raithel said, “AI may sound complex. However, it’s being implemented at a level where you don’t need to be a data scientist to figure it out. At Siemens, we have hundreds of data scientists working to create software and tools that enable our customers to use AI without having to understand anything about tensor flows. “To this end, software and tools are going to play a greater role in AI’s future. However, the industrial world needs long-term reliability and stability of tools. We can’t keep changing how everything’s done every six months. So, it’s going to take us a little longer to bring these innovations to the factory floor.”
In time, AI will become more powerful – and easier to use. Today, a robot needs to be trained for every object it interacts with. With an AI-based camera on its arm, robots will handle a wide range of variances quickly and with less training. And more is coming.
Karigiannis said, “One of AI’s disadvantages is that it doesn’t generalize well, especially if you change domain. When we learn to drive a car, we can drive others. We can even carry some of that knowledge over to related activities like driving a remote control car or a drone. With AI, when you change domain, you must train the models all over again. “Today, AI doesn’t understand what a crack is. But imagine if it did. Then AI could identify cracks anywhere, not just where it has been trained to find them. At GE, we’re focused on developing this type of generalized training. Rather than learning from scratch, OEMs will be able to extend AI’s capabilities across different parts and domains.”
– The Association for Advancing Automation (A3) is a CFE Media and Technology content partner. Edited by Chris Vavra, web content manager, Control Engineering, CFE Media and Technology, [email protected].