Transparent clean-in-place (CIP) systems can be programmed in a variety of ways, but the process is often difficult to follow. Learn more about the benefits of a transparent process and how it helped one company improve their operations.
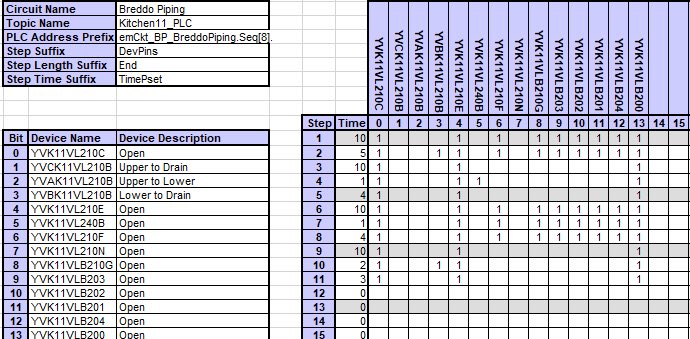
Clean-in-place (CIP) systems can be programmed in a variety of ways. While the intention, to clean stuff reliably and efficiently, is always the same, the process is often difficult, which was the case for a major dairy manufacturer. The manufacturer, which was struggling to meet production and sanitation demands, needed to modify their CIP systems to allow for better control over all aspects of the cleaning process as well as have flexibility for future process additions.
The problem was many programmers had developed their CIP systems. As a result, making a simple modification to the system had become a tedious and time-consuming endeavor. The team looked to develop a standard that could be applied to each system. They determined creating pin charts would be a quick and efficient solution, provide ease of use, and give the customer the most visibility and flexibility in their cleaning process.
Once implemented on the initial pilot phases, there was an immediate impact. The sanitation manager is now qualified and able to review and optimize each circuit cleaning sequence through a simple to use interface. Cleaning optimization takes minutes today where, historically, it required several hours to implement.
In addition, the manufacturing team can analyze the historical data of each cleaning process and identify areas where further optimization measures will have the most impact to the operations. The team can show steps to further reduce chemicals, water usage and overall costs.
It starts with lowering the veil of complexity and opening transparency to the system. Once the people that touch the process daily know what the systems are doing, they can identify and fix the issues that have been plaguing the efficiency and effectiveness. Sometimes they even discover things they were not aware of.
Eric Gruber is senior controls engineer at Avanceon, a CFE Media content partner. This article originally appeared on Avanceon’s website. Edited by Chris Vavra, production editor, Control Engineering, CFE Media, [email protected].