How right-sizing a batch management solution paves the pathway for advanced technology solutions and helps companies realize Industry 4.0 automation.
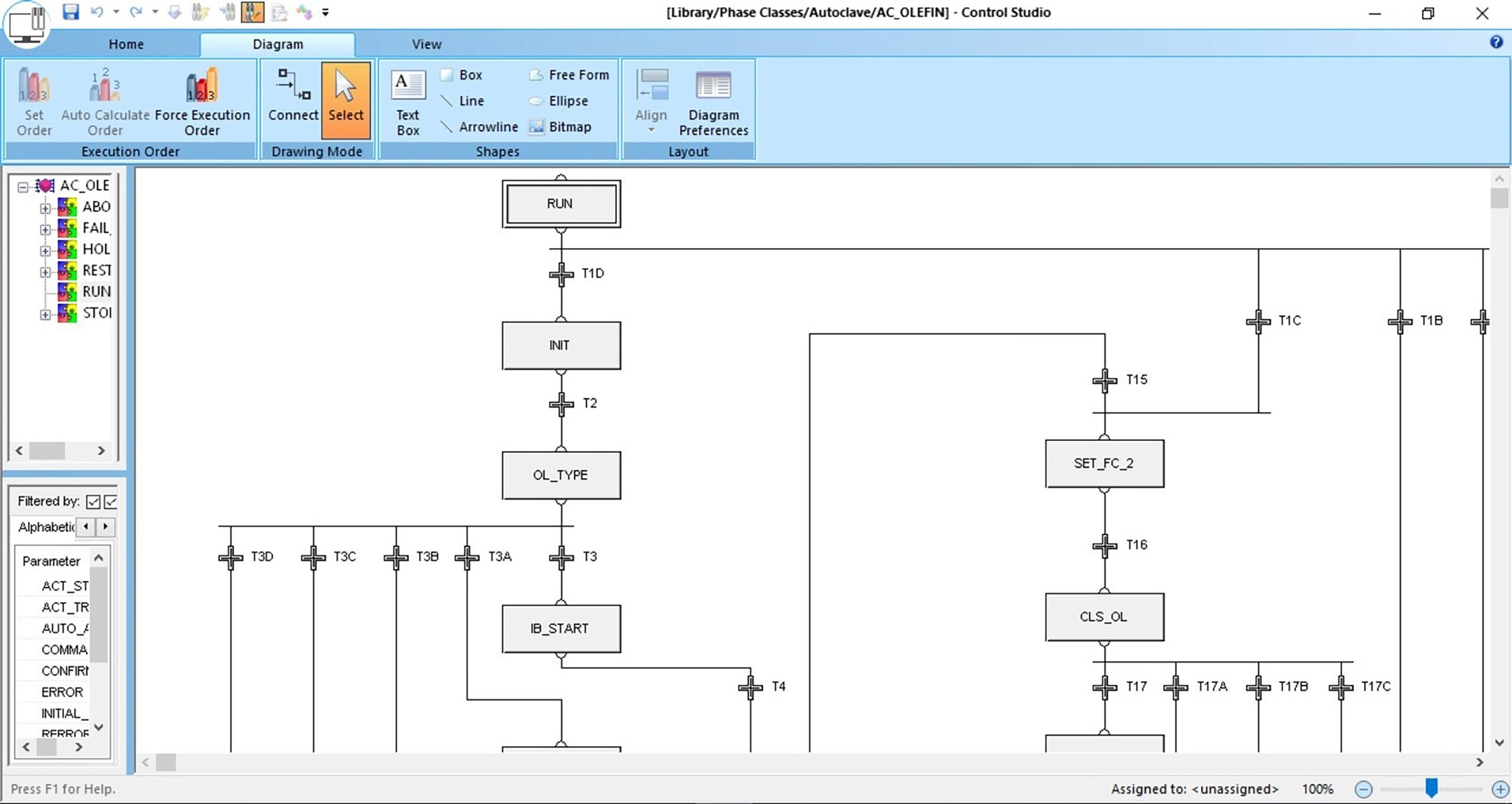
Learning Objectives
- Understand how batch management solutions can improve advanced technology solutions.
- Learn what’s required for choosing the right batch control solution.
- Understand what considerations are needed for a custom solution.
Batch management system insights
- Digitalization tools enhance manufacturing by bridging data from various systems, enabling better process understanding, real-time troubleshooting and AI-driven optimizations across the entire facility.
- Effective batch management, aligned with ISA-88 standards, is crucial for complex processes, ensuring consistency, scalability and compliance while facilitating integration with advanced Industry 4.0 technologies.
Many digitalization tools are focused on bridging data from multiple sources such as control systems, business management systems (ERP), laboratory and quality systems (LIMS), and computerized maintenance management systems (CMMS). From these sources, users can get a more complete picture of a facility’s processes to better understand what is happening. These aggregated “data lakes” also allow companies to better leverage artificial intelligence (AI) and big data.
With these tools, users can better troubleshoot manufacturing processes, uncover logistics issues, meet production demand in real time and better deploy maintenance personnel. Manufacturing execution systems (MES) are linking control systems to the business ERP, improving production scheduling to improve on time deliveries and reduce product inventories. Another key driver for digitalization projects is the need to make data more accessible to users throughout the organization.
By using visualization tools and communication technologies, manufacturers can deliver data to both frontline operators and back-office workers via web browser, tablets and other mobile devices. Companies with batch processes have different data analysis needs and more complex data sets, but well-implemented batch management solutions will help them reap the rewards of the Industry 4.0 revolution.
Every manufacturer can benefit from digitalization technologies. By recognizing the importance of established, proven solutions and building that foundation with the latest advancements, manufacturers are afforded opportunities for improvement, growth and efficiency.
The biggest return with digitalization advancements comes from well-designed and operating core processes. Batch management systems are an example of how manufacturers can build from foundational technologies that provide flexibility to choose the right-sized solution for them.
Benefits of batch management systems
Control of batch processes requires an additional layer of programming and control beyond their continuous process cousins. Even within a single recipe, batch control often requires coordination of several sequential operations, where each step in the process depends on the correct completion of the steps prior.
Some processes will even contain parallel diverging and converging operations. When the batch control system is used to manufacture multiple products, their distinct recipes including different raw materials, equipment needs and associated parameter settings to produce each final product all must be managed.
In addition, the requirements to meet robust traceability documentation, adherence to ISA-88 batch control standards and good manufacturing practice (GMP) standards add further complexity to management of the process.
Manufacturing facilities that run batch systems are more complex, and the metrics used to analyze these processes follow suit. Digitalization projects will depend on their raw data to be organized and accessible. Batch facilities that lack a good batch management system can still benefit from digitalization projects but must spend more time and resources to organize their data. If users are considering a control system upgrade or planning for a new production unit, careful consideration should be given to the batch management platform options (see Figure 1).
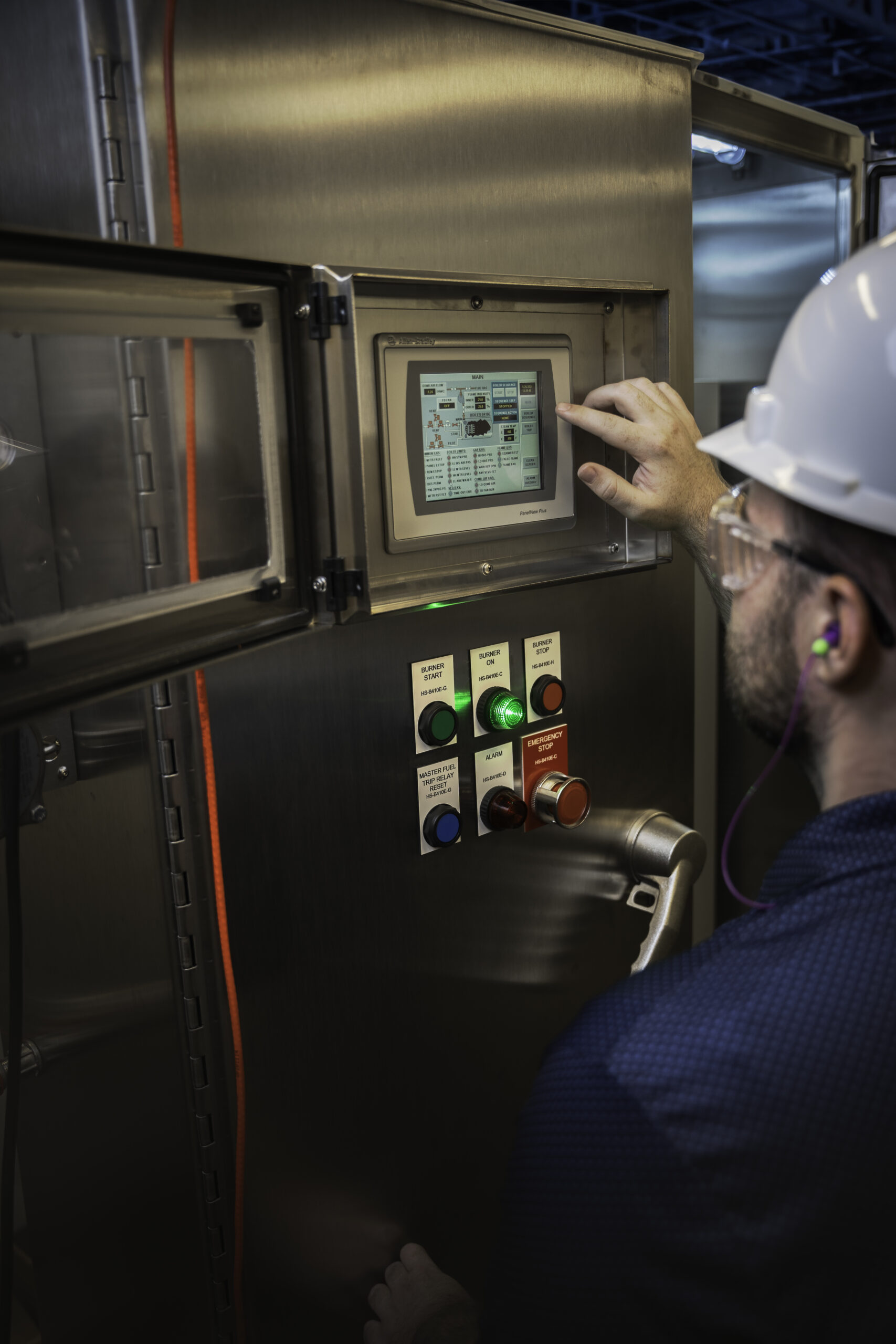
With a good batch management system in place, users will be able to calculate cycle times, track raw material conversion during a reaction phase and develop fingerprints for golden batch characteristics. Digitalization tools can help analyze performance and make AI predictions and recommendations for process improvements.
The selection of the most appropriate batch control system must consider all application-specific factors, as well as the facility’s plans for future growth, which include not only production expansion but technology advancements. While there are many advanced batch control software systems available, by completing a thoughtful review of the facility’s true system requirements, a solution that best meets their needs can be identified and implemented. The best batch software solution is not always the most advanced option.
Why following the ISA-88 standard for batch control design is a best practice
The ISA-88 standard provides a well-defined and organized approach to the design and control of batch processing systems that is considered industry best practice. ISA-88 design principles should be followed regardless of whether or not compliance will be formally met.
It lays out standardized models, terminology and methodologies that result in better repeatability of process, consistency of final product, reusability of code and overall scalability and adaptability in batch processing. Formal compliance to the standard is important for regulated industries, including those that must also meet GMP requirements such as:
- Pharmaceutical
- Food and beverage
- Biotechnology
- Chemical
Choosing the right batch control solution
With many batch control software solutions available, often including multiple add-on tiers of functionality and additional cost, it can be challenging to select the best option that addresses the needs of a particular process and facility (see Figure 2).
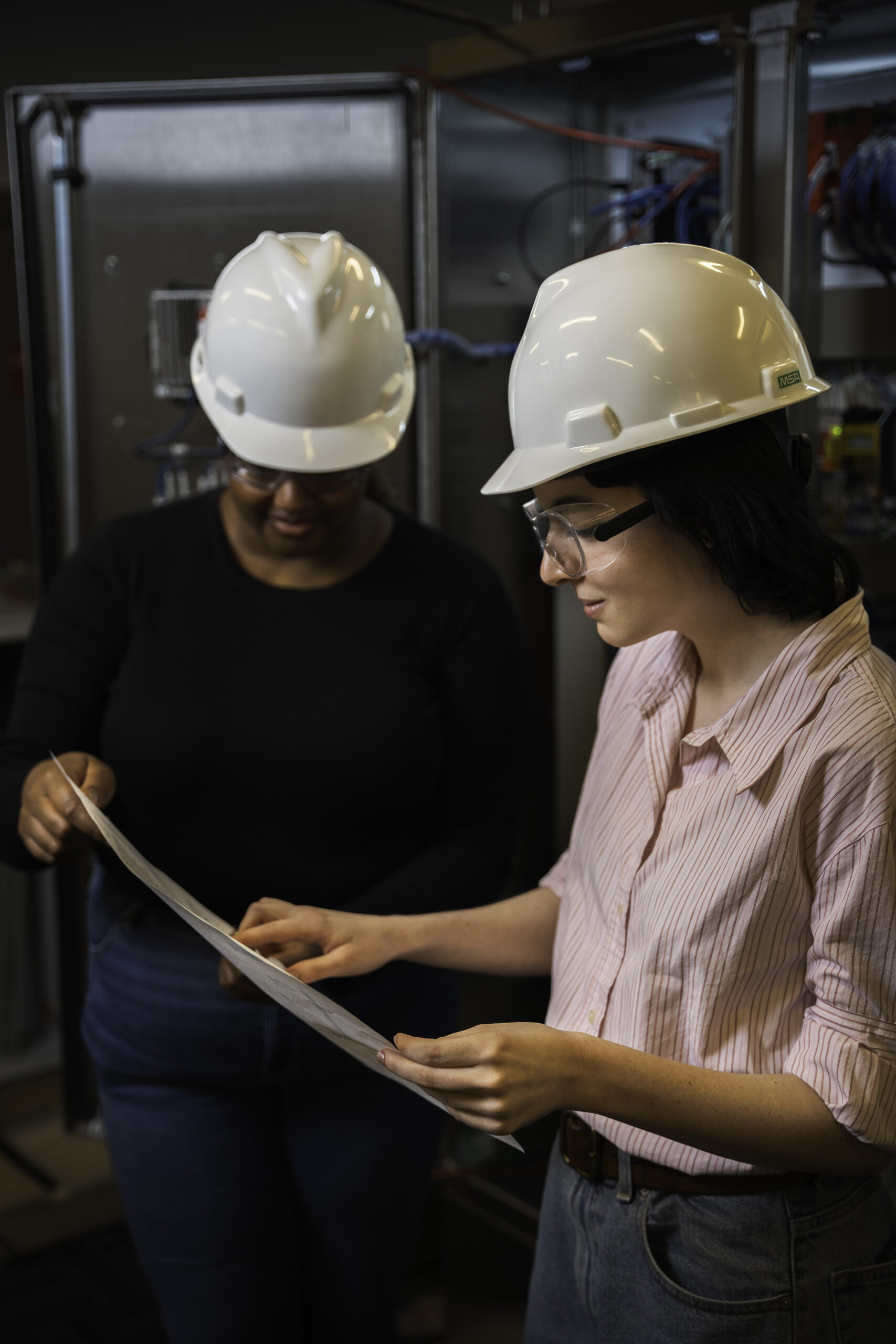
Batch implementations can be categorized into tiers of batch management functionality.
● Tier 1: Simple sequences/light batch. This level uses built-in basic process control system functionality and allows for the creation and execution of sequencing logic, which is essential for executing operations within a batch process. Depending on the control system platform, batch code may be written using a dedicated sequential function chart (SFC) language or using standard text, ladder logic or function block programming. Sequences may or may not use ISA-88 design principles. This is a good solution if only light sequencing is required as it often requires no additional licensing and minimal design effort.
● Tier 2: Batch management. This solution is often sold as an add-on product to the base control system functions, often on a sliding scale according to the number of batch units required. Modern platforms include compliance with the ISA-88 standard, incorporating structured process control and recipe management. This solution may require additional investment in a separate batch server. This solution often provides new, specialized interfaces for both operators and engineers to better schedule, track and troubleshoot batches (see Figure 3).
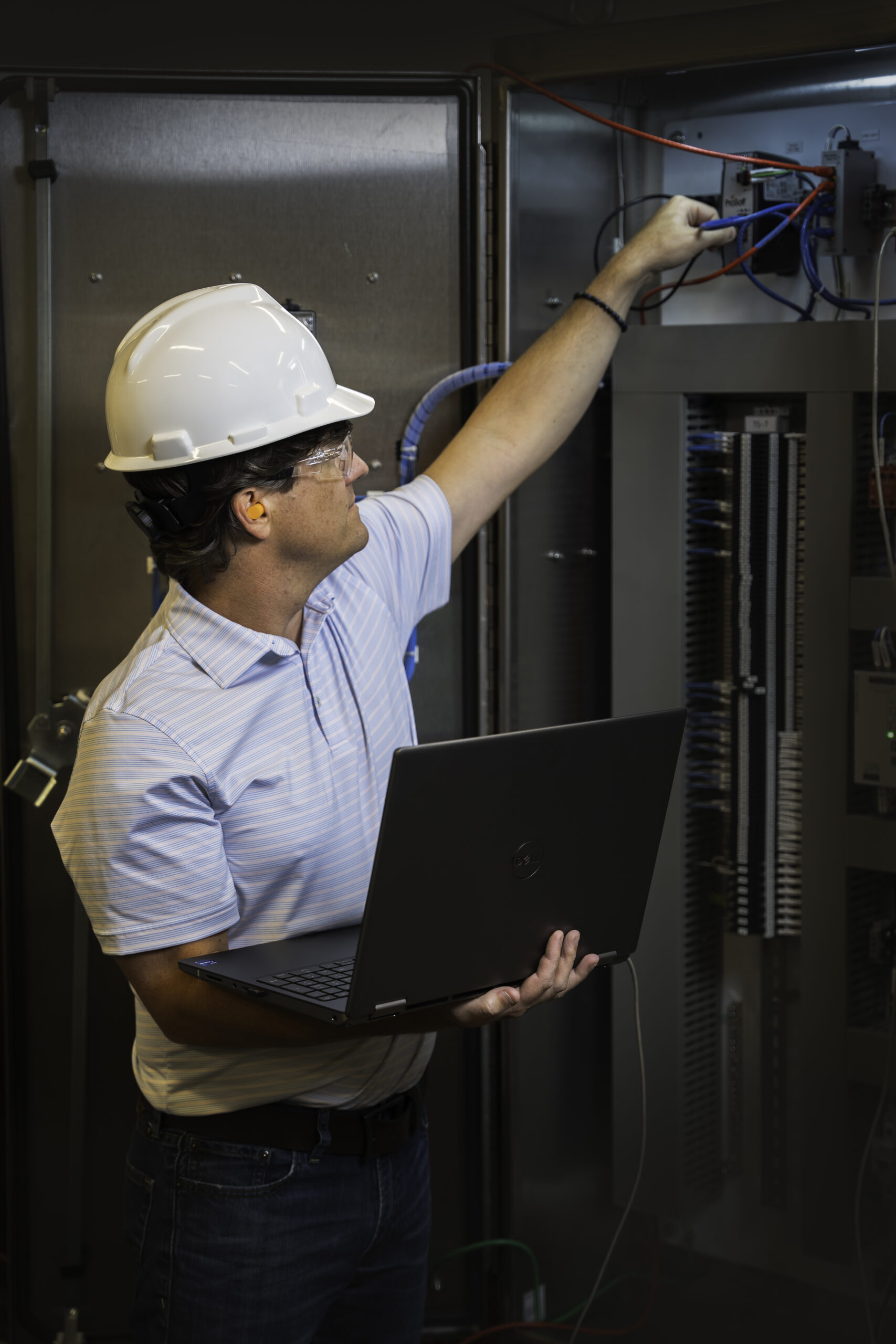
● Tier 3: Advanced batch/campaign management. Advanced batch management integrates all tier 2 capabilities and is also designed to handle multiple recipes, multiple production trains and dynamic equipment selection and reservation. This level also can handle campaign management so individual batches no longer have to be scheduled by the operator. For a complex process or production facility, this level can increase a plant’s throughput by minimizing idle equipment time and batch start delays, which reduces overall process cycle time.
Seven considerations for a custom batch management solution
Since each batch process and manufacturing facility has specific needs, the software needs will also vary. The most advanced software solution is often not required to address a system’s needs. A cost-effective custom solution may be a better overall fit. Some of the factors to consider include:
1. Level of complexity that must be addressed within a recipe. Numerous sequential steps and/or forks within a process that proceed in parallel before recombination into a single step is typically best handled with functionality integrated into ISA-88 batch software.
2. Number of recipes that must be run by the control system. A process that includes managing many recipe variations may benefit from higher-tier software. However, depending on the process, sometimes the needs can be addressed with more cost efficient and custom solutions.
3. Scale of operation. Controlling processes involving multiple trains, parallel processes and dynamic equipment allocation is best handled by higher-tier software.
4. Traceability requirements. Mid- and higher-tier software solutions often offer more comprehensive traceability features compliant with ISA-88 standards, including generation of electronic batch records showing detailed batch history information. However, alternatives to higher-tier software can also meet traceability requirements.
5. Formal ISA-88 and GMP compliance. GMP requirements demand proof of product consistency, quality and detailed batch history records. These requirements are best met with mid- or higher-tier software that supports ISA-88 compliance and documentation capabilities (see Figure 4).
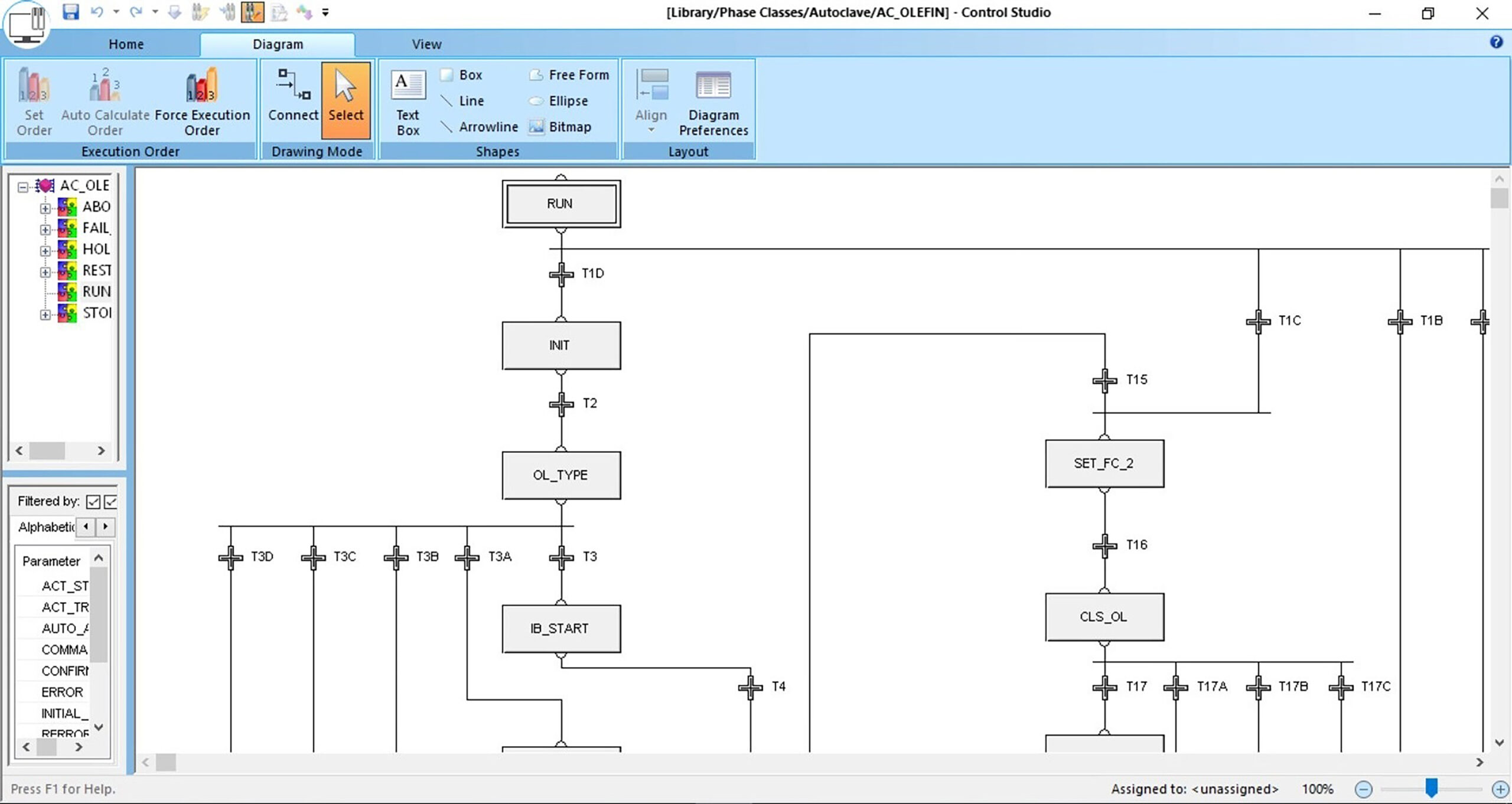
6. Future growth plans/scalability requirements. The software selected should be suitable to address future plans for more batch processing due to production increases, if appropriate.
7. Matching the existing control system vendor. When batch control software is being selected to operate on existing equipment, it is best for compatibility reasons to use the batch control software offered by the basic process control system vendor. However, there may be certain situations (legacy control system platform, a mixed control system environment, etc.) where this is not possible. Careful planning and testing will be required in these cases.
MES and batch processes
A chemical manufacturer completed a process expansion for a facility running a programmable logical controlled (PLC) batch process. As part of this, they needed to update their existing MES. They had two options: Implementing the next software tier from their programmable logic controller (PLC) vendor batch recipe management system or adapting and improving an existing custom solution. While the vendor solution offered some advantages with built-in functionality, the chemical manufacturer was concerned about some of the software limitations and the recurring annual software subscription costs.
The custom MES solution provided a better link to their ERP platform and all recipe management functionality the facility required. This provided gains in speed of the process from customer order to product shipment and alleviation of manual functions. Thanks to their well-designed batch implementation, the new MES was a success. It connected to the batch system and executed orders from the business ERP and loading recipes for dozens of products.
The batch solution foundation allowed the MES to connect the ERP with the batch process, perform as a process engineer user interface to recipe management and tie together the process and business units, resulting in a successful product expansion. With this solution, the chemical manufacturer added a new feature with dynamic parameter entry, increased maximum parameters per batch phase from 22 to 63 and developed 14 recipe management interface displays.
Visualizing and analyzing batch processes
Another manufacturer had been constrained by poor visibility and insight into their processes. Process analysis was restricted to whatever trends were available on the control system HMI and data either manually exported or written down on log sheets. Meanwhile, personnel across the company were becoming more used to obtaining other business data using Power BI and web browser interfaces.
Their digitalization efforts also focused on pulling data out of the control system and into more easily accessible data warehouses. Once there, process data could be delivered to anyone in the organization or even pushed into the cloud for further analysis. They were also able to push data out to key performance indicator (KPI) screens on the process floor so operations could better track their processes and make informed real-time decisions.
Batch manufacturing for advanced Industry 4.0 tools
The selection of the most appropriate batch control software solution relies on careful consideration of current and future application-specific requirements. AI and digitalization tools can then be implemented to further optimize performance. The combination of foundational technology and advanced solutions results in an efficient, reliable and scalable operation that meets the distinct demands of the process and unlocks the benefits of the most advanced Industry 4.0 tools.
Heath Stephens, P.E., is a digitalization leader and Sean Phillips, P.E. is a project manager for Hargrove Controls & Automation.