Cartesian robots offer space and cost savings, wide dynamic range, and are simpler compared to other industrial robots.
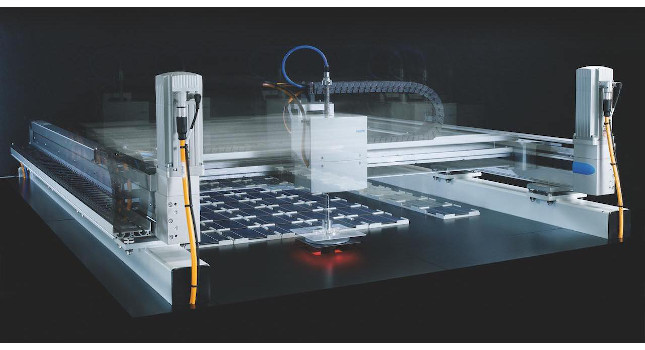
Cartesian robots might not fit anyone’s image of an industrial robot. However cantilevered and gantry Cartesian robots offer several advantages in many applications compared to six-axis, selective compliance assembly robot arm (SCARA) and parallel robots. The most important of these advantages include greater workspace utilization, high dynamic range, simplicity and low cost.
Ask most plant engineers what they highly value in new automation systems and the answer will likely be its small footprint. In today’s plants, space is at a premium, making workspace utilization crucial.
Figure 2: Festo Handling Guide Online enables the design of a Cartesian robot with a quote and a CAD file in as little as 30 minutes. Courtesy: Festo[/caption]
Also, consider the workspace when planning for a robotic application. Does the workspace most closely resemble a plane, box, or sphere? Answering this question will help plan for the smallest footprint.
Dynamic range in the workspace
Cartesian robots are customized, scaled to the size of the workspace and the dynamic range required by the application. For example, a large workspace with light payload will have lighter drives with less torque, which decreases expense. Six-axis, SCARA, and parallel robots are off-the-shelf products. The engineer has to find one closest to the need, which means a robot may not be optimum in cost or performance.
In the example above of a large workspace and light payload, the only other robot other than a Cartesian may be a much larger and heavier unit than the payload requires because it is the only unit with the necessary reach. Cartesians deliver high accuracy across the workspace; a six-axis robot loses accuracy at the farthest extent of its reach.
Custom solutions may not require long lead times or extra cost
The words “custom solutions” can bring up images of long lead times and expense. However, Cartesian robots are simple mechanisms consisting of various combinations of relatively low-cost axis.
Some Cartesian vendors have developed online design tools that can lead to a completed design, a computer-aided design (CAD) file ready for delivery, and a quote within 30 minutes. Delivering an assembled robot or a kit may take only weeks.
Of the major classes of industrial robots, Cartesians are at the low end in terms of cost, although each is custom-assembled from off-the-shelf products. Using off-the-shelf components, lowers repair and maintenance cost, as well. For customers purchasing kits rather than fully-assembled Cartesians, vendors offer off-the-shelf drives and axes designed for fast assembly without adding mounting plates. Design tools help ensure plug-and-play functionality.
For X, Y, and Z motion, a standalone control panel may not be necessary, which lowers cost and reduces footprint. For advanced motion applications, such as curvilinear motion required for laying adhesive, a standalone control panel with motion controller may be required, incrementally adding to the unit cost and footprint. Cartesian robots are simple kinematic solutions that are easy to maintain and repair.
A few concerns about Cartesians
Cartesians are not perfect for all applications, however. The upper limit in degrees of freedom for a Cartesian is generally three axes plus rotation. If the workspace and application require greater degrees of freedom, then Cartesians are simply not the right answer. Cartesian robots cannot be used in washdown environments, and they require precise alignment and a flat mounting surface.
Cartesian movement in the X, Y, and Z axes can be programmed directly from the PLC or industrial computer and isn’t difficult, but it is still programming. For complex curvilinear patterns, a motion controller is required. To speed programming of more complex movements, some Cartesian robots are programmed using function blocks provided by the suppliers.
Example applications
Cartesian robots can be configured as one-, two-, or three-dimensional handling systems plus rotation. Cartesian robots accommodate electric and pneumatic grippers, including gripper fingers, vacuum grippers, vacuum-driven grippers, rotary and swivel, and functional combinations. Drives, axes, and cylinders can be pneumatic, servo pneumatic, and/or electric. Bar code scanning and vision systems are often used with these robots. Cartesians can be included within IIoT and Industry 4.0 architectures. The chart shows sample Cartesian robot applications.
Applications for Cartesian systems
Large systems | Highly dynamic systems | Compact systems |
|
|
|
When a robot application comes up, analyze the workspace, consider the dynamic and reach required, and the cost and simplicity of operation needs. Then determine if a Cartesian robot may be the right choice.
Sandro Quintero, product manager – electric automation, Festo. Edited by Chris Vavra, associate editor, Control Engineering, CFE Media, [email protected].
MORE ANSWERS
Keywords: robotics, Cartestian robots, motion control
Cartesian robots have many advantages including greater workspace utilization, high dynamic range, simplicity and low cost.
Cartesian robots are not ideal for applications that require a great deal of freedom of movement.
Analyze the workspace and the application to determine if a Cartesian robot is the right choice.
Consider this
What benefits could Cartesian robots provide in your plant?