In labor-constrained industries, collaborative robots could boost productivity.
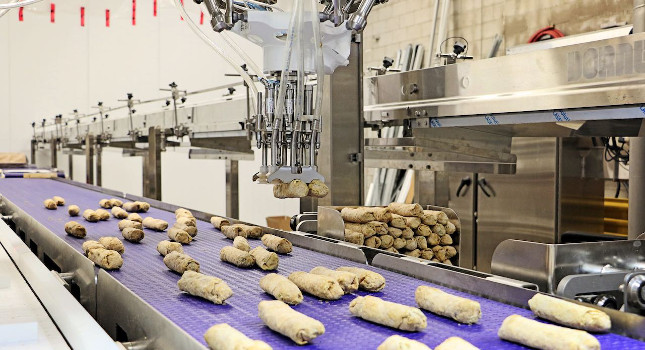
Collaborative robots are highly productive automated systems. They can unlock applications previously not possible with robots and free knowledge workers or more experienced factory personnel from repetitive and tedious tasks.
Collaborative robots are intended for use in industrial settings by “collaborating” with human workers. Ideally, they combine the dexterity, flexibility and problem-solving skills of a person with the strength, endurance and precision of a machine. These robots can safely work on tasks whether a human is working nearby or not.
A key driver for many manufacturers looking at robotic solutions is economics. Because the unemployment rate has dropped, particularly in the area of general labor, and the minimum wage has increased, it is difficult to meet the demand for people. Robots can fill the gap – particularly if you can have them work with an operator to reinforce worker productivity.
Collaborative robot capabilities
Typically, collaborative robots have advanced sensors and computing abilities that allow them to navigate complex environments in manufacturing plants. They can be used for quality control such as detecting a defective part or product and removing them from a line. They also can manipulate materials unsafe for humans to handle; for example, in a chemical processing plant where working with chemicals can cause harm to a person.
Collaborative robots find a home in smaller manufacturing operations where they can tend to machines, handle small parts and complete tasks like warehouse order picking. They are easily programmed and handled because they are “teachable,” allowing users to set up the robot to accomplish tasks that require different paths within a plant or that require heavy lifting. They deliver return on investment quickly because of this ease of use. In operations where manufacturing processes are subject to change, collaborative robots can be reprogrammed and repositioned to keep the plant moving and products in production.
Collaborative robots can share the same workspace with people without the need for “safety fences.” They don’t have sharp corners or exposed mechanical parts, so workers are not in danger of getting hurt by contact with the machine. However, if they do encounter a worker, they stop so as not to cause any harm.
Abundant advantages
Another advantage of collaborative robots is reduced downtime. Manufacturers need to employ robotics in their plants to stay competitive. Robots can be programmed to run simultaneously with other, more complex activities that need a human worker to complete, accomplishing more with less.
Collaborative robotics will be used in multiple manufacturing industries, from food and beverage to automotive, and in various applications that include pick & place, packaging, assembly and dispensing (see Figure 1).
Of course, manufacturers, in concert with their robotics integrator, should assess all risks associated with the installation and use of a collaborative robot application. All potential hazards must be addressed before the robot is put into production operating alongside a worker. Once done, these automated solutions can be the answer for manufacturers who need to increase operational efficiency, throughput and quality, all while protecting employees, the company and maximizing process safety.