2023 System integrator of the Year, Eosys, excelled in digital transformation, batch control, and other control and automation system project integration, with emphasis on mentoring and continuing education.
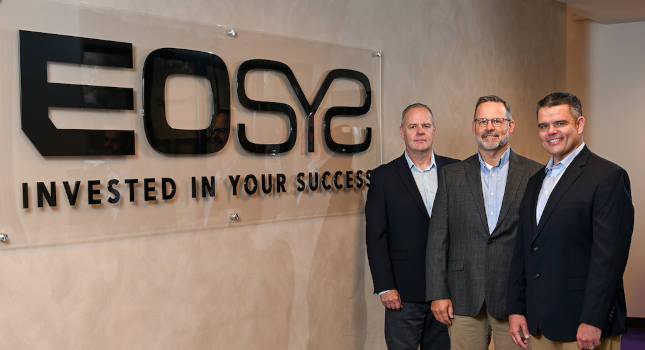
Learning Objectives
- System Integrator of the Year for 2023, Eosys, discusses automation projects at Gibson guitars, chemical manufacturing and food and beverage customers.
- Mentoring and cooperative engineering programs help advance Eosys system integration goals.
- Eosys helps drive excellence with continuing education and company ownership.
System Integrator of the Year, Eosys integration insights
- Recent system integration project success at Eosys (formerly Premier System Integrators) included digital transformation at Gibson guitars, chemical and food and beverage automation projects.
- Mentoring and continuing education are two areas of progress for Eosys, Control Engineering and Plant Engineering (CFE Media and Technology) System Integrator of the Year for 2023.
Gibson needed a digital transformation to keep up with COVID-19 guitar demand. Chemical manufacturing needed a distributed control system (DCS) integration. Food and beverage customer needed automation upgrades. These are among successes achieved at Eosys (formerly Premier System Integrators*), leading to its selection at 2023 System Integrator of the Year in the over $30 million in system integration revenue category.
David Lax, president of Eosys, answered questions from Control Engineering and Plant Engineering (CFE Media and Technology) about these and other topics.
Recent Eosys system integration achievements, history
Question: Congratulations on receiving the 2023 System Integrator of the Year award: Talk about what this recognition means for Eosys.
It’s an honor to be selected as a 2023 System Integrator of the Year. This recognition is an important validation that we are building a best-in-class company. At Eosys, our desire is to be the preferred integrator of choice for talented employees and customers looking for long-term partnerships, and this honor reinforces that vision.
Question: Describe recent projects that you’re most proud of. What has made them a success for your company, in your opinion?
As a market leader in automation and information solutions for more than 30 years, Eosys has staked our reputation on a commitment to each customer’s success, taking their processes and integrating automation and controls that fit.
Digital transformation for Gibson guitars
During the pandemic, Gibson Brands Inc., the world’s most iconic guitar brand, saw a massive increase in consumer demand for guitars. Existing systems and paper processes were insufficient, and Gibson needed a digital transformation partner to guide them through this process as efficiently as possible. An Eosys team quickly got to work on a solution design and implementation roadmap. In less than six months, the first phase of the digital transformation was fully implemented at the pilot site. The pilot was a rapid success, enabling Gibson to meet increased production goals while improving traceability and visibility of manufacturing operations. Over the next several months, the team enhanced and rolled out digital transformation to two other facilities. As Gibson continues to address market demand, collaboration and planning for future phases of digital transformation are underway.
Chemical manufacturing, food and beverage automation integration
In addition, Eosys completed a $1.2 million automation project for a large chemical manufacturer in the Southeast. We implemented a Foxboro distributed control system (DCS) platform with intrinsically safe controls that included the integration of a redundant Wonderware InBatch batch manager. Eosys successfully executed the project, adapting the design in progress to address supply chain challenges.
We simultaneously completed two multi-million-dollar projects for a well-established consumer brand food and beverage company. The Eosys team’s ability to coordinate and collaborate with engineers across multiple offices was critical to system integration project success.
System integration project managementÂ
Question: What are some methodologies and philosophies applied to projects? How have they evolved over the years, particularly considering COVID-19?
Our central project philosophy is to truly become a partner with our customers, not just a supplier. That starts on day one by truly listening to our customers and seeking to understand their problems. We want to provide solutions that fulfill what they actually need, rather than just what they asked for.
Over the years, we have evolved our standard project methodology to include progressive customer design reviews, simulation, and acceptance testing to meet customers’ expectations. We design code with an eye toward maintainability so customers can support their systems. Early investments in IT security and secure software development lifecycle management eased compliance with maturing customer requirements.
COVID-19 demonstrated that our internal systems and process were robust, and our remote workforce was able to support our customers in essential businesses seamlessly.
System integration customer relations: More digital transformation, remote work
Question: How have customer expectations for projects changed due to the COVID-19 pandemic?
During the pandemic, we saw a sharp rise in the demand for digital transformation projects across multiple industry segments. Customer purchasing decisions were made quickly, and implementation was rapid. One major factor was a deep need to make production metrics visible from remote locations.
We experienced great success as our workforce moved to working remotely throughout the pandemic, which led to a culture shift at Eosys, creating greater flexibility about where work is completed. This openness to remote work has even extended to how we engage with some of our customers. We are experiencing greater willingness and more requests for remote support, leading to more efficient responses as well as cost savings.
Question: How important is it to develop long-term relationships with customers during projects and why?
In a typical year, more than 80% of Eosys business is derived from customers with whom we have multi-year relationships. Long-term partnerships are mutually beneficial, creating greater efficiencies because we understand customers’ business needs and future direction and reducing project lead times and deployment. The deep knowledge gained over time allows us to provide value beyond the services explicitly outlined in the proposal as we evolve to engage the customer with the same-team mindset.
Question: Have the supply chain issues affected current and future projects in a significant way? If so, how?
No industry is immune to the effects of the current supply chain disruption. For Eosys, supply chain issues have created additional costs or unintended schedule delays. In some situations, we have had to redesign solutions with alternative hardware. Due to the uncertainty, some customers have postponed projects. We’ve also noticed that project cycles are often intentionally extended to create a time delay between design and commissioning, adding ample time to hedge the risk of delivery delays.
System integration mentoring, future investments
Question: What do you do to help guide younger engineers along in projects so they gain valuable experience?
We instill a culture that everyone has a mentor. We discourage accepting one-person projects that do not allow for a less-experienced engineer to be mentored by a more senior engineer. Our more experienced engineers are expected to treat every project task as an opportunity to build the next generation of Eosys engineers. To reach the Eosys senior engineering ranks, engineers must demonstrate effective mentoring. This is demonstrated through successful project execution that’s measured partly by full utilization of less experienced engineers. More senior engineers also produce one-hour technical lunch and learns. For each project assigned, less experienced engineers have formal, written learning or continuous improvement goals, and mentors have complementary mentoring goals. Eosys monitors goal achievement regularly through performance evaluations. This evaluation process is designed to encourage engineers to seek a wide breadth of experience early in their careers and then pursue depth as they progress towards mid-career levels. Eosys encourages engineers to complete industry certifications in technologies aligned with core company competencies.
Co-op program engineers undergo human-machine interface (HMI) and programmable logic controller (PLC) training, assist with building industrial control panels, participate in the design of an industrial control system and assist in field operations and system integration.
Question: If there is one long-term goal you have for the company, what is it?
The long-term goal is to grow the value and esteem of the Eosys brand through the pursuit of excellence, investing in our customers success, and leveraging our shared ownership culture. Ultimately, we want to provide long-term, enriching careers with the bonus feature of experiencing the benefits of retiring as an owner.
(*On Dec. 6, 2021, Premier System Integrators announced rebranding to better reflect its employee ownership, recent growth and expanded services. Eosys has more than 200 employee-owners working across four offices in Nashville, Atlanta, Cincinnati and Huntsville. Eosys offers control system integration, automation solutions, digital transformation, panel fabrication, field installation services, and industrial IT.)
David Lax is the president of Eosys. Also contributing to this article from Eosys were: Shaun Guy, vice president of business development; Tyler Graham, director of business development – digital transformation; Steve Orth, director of project management; and Tony Valasek, director of engineering. Edited by Mark T. Hoske, content manager, Control Engineering, CFE Media, [email protected]. Chris Vavra, web content manager, CFE Media and Technology, collaborated on questions. Amanda McLeman, director of research and awards programs, administers the System Integrator of the Year program. www.controleng.com/SIY
KEYWORDS: System Integrator of the Year, Eosys, project management
LEARNING OBJECTIVES
System Integrator of the Year for 2023, Eosys, discusses automation projects at Gibson guitars, chemical manufacturing and food and beverage customers.
Mentoring and cooperative engineering programs help advance Eosys system integration goals.
Eosys helps drive excellence with continuing education and company ownership.
CONSIDER THIS
How are you encouraging development of younger engineers?
ONLINE
Learn more about Eosys in the Control Engineering and Plant Engineering Global System Integrator Database. https://gspplatform.cfemedia.com/si/integratorProfile/5399d11fe4b025bf87df470f
4 system integration metrics that matter
Each System Integrator of the Year firm for 2023 was asked to quantify progress over the past year using a few metrics. According to Eosys:
-
The corporate team has grown nearly 20%. This investment addresses our future needs to recruit and develop talent, to secure our IT systems, and to expand our business development influence.
-
The team of engineers in cooperative education programs (Co-op) and entry level engineers has grown more than 33%. Our ability to develop highly capable and dedicated employees has been a hallmark of our success over the last 30 years. Over 25% of our 200-plus employees began as a Co-op or entry level engineer with EOSYS.
-
The digital transformation business grew over 20% in our most recently completed fiscal year. Providing digital transformation services broadens our ability to meet our customers growing needs and distinguishes us from our competition.
-
The number of completed continuous improvement (CI) projects has increased nearly 40%. Eosys has a long history of investing in and building a culture of continuous improvement, with a five-person team dedicated to building and evolving internal processes and systems, meeting the needs of stakeholders throughout the organization.