Integrating industrial Ethernet directly into the power supply helps identify and rectify issues earlier, reducing unplanned maintenance, while uninterruptible power supply (UPS) technology keeps vital controls safe during shutdowns.
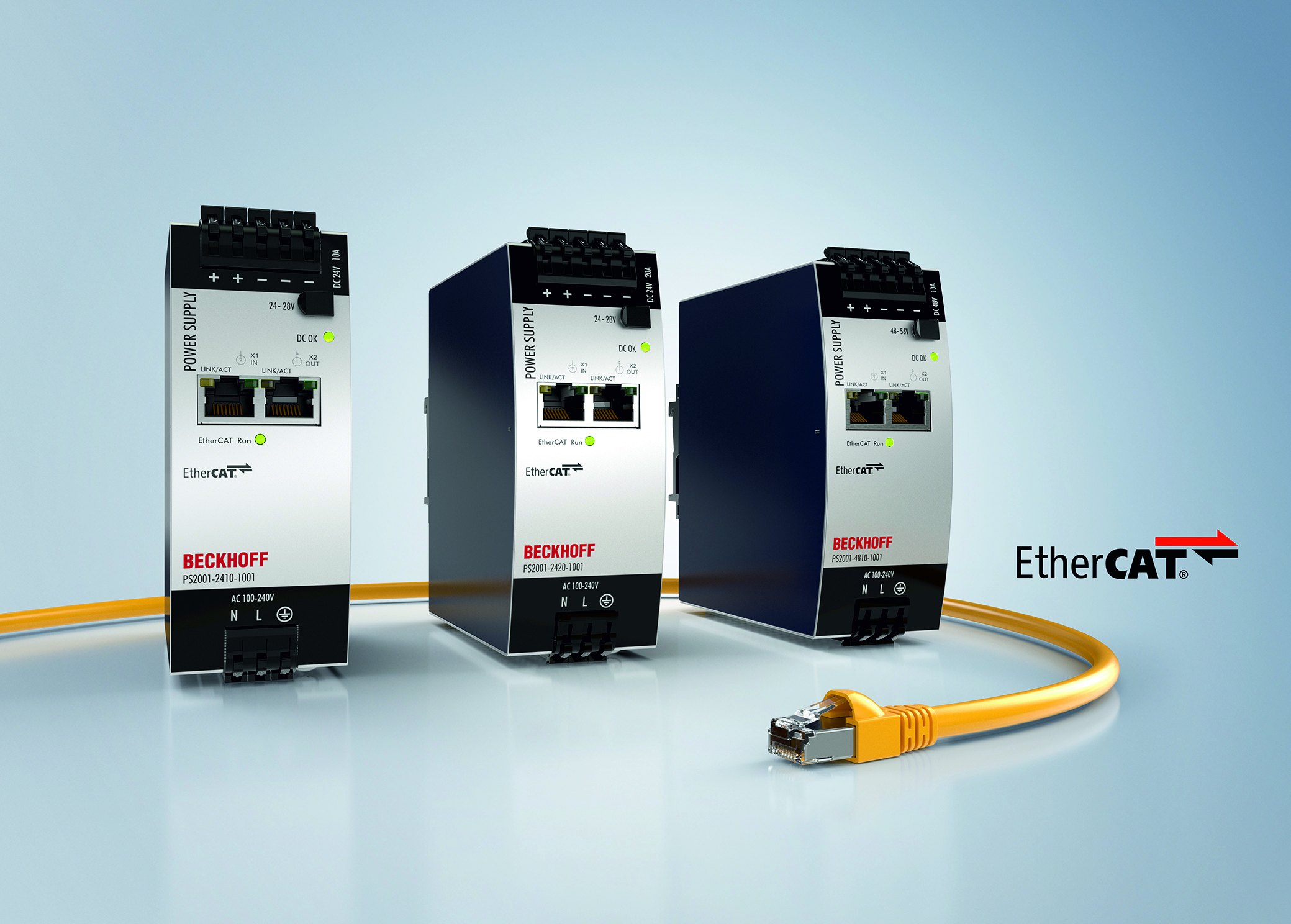
Power management insights
- Integrating advanced power supplies with EtherCAT communication enhances industrial automation by providing real-time monitoring, predictive maintenance and improved overall equipment effectiveness (OEE).
- Leveraging modular power management solutions like e-fuses and UPS systems reduces downtime, enhances reliability and optimizes energy efficiency in industrial operations, supporting continuous improvement.
In industrial automation, we see all manner of bleeding-edge solutions designed to increase system availability, throughput and uptime — not to mention energy efficiency. Huge leaps ahead in motion control performance, computing power, and IoT connectivity have opened up a wide array of possibilities. Machine builders and manufacturer end users can measure any signal, monitor potential machine or component failures, send data to the cloud, and perform changeovers instantly.
This often entails adding countless sensors or add-on “black box” devices to gather, process and send data. This approach adds expense, bloats electrical cabinets and may require engineers to learn multiple platforms to get basic data acquisition going. It begs the question of why companies are adding single-purpose devices instead of upgrading the functionality of mandatory components such as power supplies, that could do double duty?
Campaigns to eliminate downtime have overlooked many workhorse devices, including power supplies. Boosting and maintaining overall equipment effectiveness (OEE) hinges on effective power management and monitoring solutions. So much of the metrics manufacturers want to measure can be gleaned by monitoring the power supply’s status. In the past, power supplies were treated as consumable commodities with no intelligence, which couldn’t communicate to the controller like other “smart” devices. That’s changing.
New power supplies can cost effectively ensure machine uptime in many ways. The most important aspect is integration into the industrial Ethernet fieldbus to communicate with controllers and other devices. However, the benefits compound when coupled with electronic fuses, which simplify implementation while monitoring specific machine modules and uninterruptible power supply (UPS) technology for safe shutdowns. These solutions ensure manufacturers can meet productivity goals while minimizing maintenance times.
Power supplies can offer early warnings
A fundamental challenge in industrial settings is the unpredictability of the power supply. This is true whether machinery is operating in the Midwest or the Middle East. Machine faults, utility fluctuations and other issues can lead to costly downtime and maintenance. So implementing early warning systems becomes crucial. By monitoring parameters such as input voltage, output current and temperature, operators can preemptively detect anomalies that might indicate potential upcoming failures.
Early warnings ensure prompt intervention as well as enable proactive maintenance scheduling. For instance, if abnormal temperature readings suggest overheating, technicians can investigate and rectify the issue before it escalates into a critical failure. This approach not only extends the lifespan of equipment but also enhances OEE.
Power supplies equipped with an EtherCAT interface, for example, can remotely collect additional measurement and device diagnostics for comprehensive system monitoring. This allows the control system to access extensive measurement data and internal device diagnostics information and establish remote access to power supplies. Remote access via EtherCAT also makes it possible to specifically shut down sections of a plant in the event of machine downtime or a fault.
This information adds to the already robust diagnostics functionality built into EtherCAT. Users can then access the information via an automatically generated JSON file or dashboards built into their automation software. Some software options include built-in analytics packages that help to drill down and resolve power issues faster.
Who has the most to gain from implementing a more feature-filled power supply? Compelling use cases exist for equipment end users and machine builder OEMs.
-
End users: This group often prioritizes robust diagnostics and performance metrics, as these directly impact operational reliability and uptime. However, they’re rarely involved in component-level selection for machines, especially for some lower end devices like power supplies. Selecting an EtherCAT-equipped power supply could enhance their ability to increase uptime and schedule maintenance. This means fewer missed deadlines and the ability to track down power issues in production environments.
-
OEMs: While this group directly purchases the components, they’re often very cost-conscious to try to be as competitive as possible. An EtherCAT-equipped power supply may come with a marginally higher price tag, but it provides cost savings in the long run, in terms of troubleshooting functionality, enhanced performance and increased longevity. In addition, machine builders interested in pursuing machine-as-a-service (MaaS) models would benefit from the enhanced monitoring and preventive maintenance capabilities offered by these solutions.
Understanding EtherCAT-enabled power supplies
These types of advanced 24 or 48 Vdc power supply options look nearly identical to their predecessors in size, shape, etc. They have two RJ45 interfaces added to establish EtherCAT communication.
Real-time monitoring of input and output voltages and output currents allows operators to set threshold alerts, triggering immediate responses to potential issues before they impact operations. Transparent data exchange powers automatic detection of additional loads in the system. Using an interoperable fieldbus facilitates seamless integration into the machine control environment for comprehensive diagnostics and data analytics.
Similarly, temperature monitoring plays a critical role in identifying environmental conditions that degrade performance or lead to premature failures. Power supply efficiency also emerges as a critical consideration. Devices that operate at more than 96% efficiency, for example, consume less power and generate less heat than similar devices rated at 95% efficient or less. Higher efficiency extends the operational lifespan of equipment by minimizing heat-related wear and tear.
Furthermore, greater efficiency in power supply technology enables finer monitoring and control granularity. Integrating these technologies into industrial automation systems empowers operators with real-time insights into energy consumption patterns. This also enables plant managers to make informed decisions regarding energy efficiency initiatives and operational optimizations.
Boosting reliability with UPS technology
Even with the best power supplies in place, power interruptions are inevitable in industrial environments. Any power loss poses significant risks to key equipment and processes. Improper shutdowns of industrial machine controllers can lead to issues on reboot, further exacerbating the headaches and costly downtime.
In these instances, UPS systems play a pivotal role by providing a seamless transition during power loss events. There are various types of UPS systems available, each catering to specific operational needs:
-
Capacitor-based: These UPS systems offer maintenance-free operation with, for example, 0.3-0.9 Watt-hour capabilities. The associated shorter hold times make them suitable for applications where immediate shutdown is permissible.
-
Battery-based: These UPS systems provide longer hold times with, for example, 15-30 Watt-hour capabilities. They’re essential for environments requiring extended uptime during power outages. The only tradeoff is they require replacement of the NiMH battery cells every few years to ensure reliable performance.
The choice between these systems depends on factors such as the criticality of operations, power consumption requirements and maintenance preferences. Consider what type of controller the application has: Is it a large industrial server or a microcontroller? Also, evaluate how much data needs to be saved. Users also should ask whether they’d like the UPS to power the human-machine interface (HMI) hardware during shutdown so operators aren’t literally in the dark about what’s happening. For instance, industries with stringent uptime requirements may opt for a battery-based UPS despite the periodic maintenance requirements.
With UPS hardware, communication options include USB and digital input/output (I/O), among others. USB interfaces provide detailed diagnostic information, including voltage readings and operational parameters, enabling comprehensive analysis and optimization. However, digital I/O interfaces offer simplified signaling for basic operational commands. The choice depends on the specific operational requirements and compatibility with existing automation frameworks.
The next phase of power monitoring
As advanced power monitoring becomes standard in machine design, the next phase after one EtherCAT-equipped power supply for an entire machine will be individual electronic fuses for specific machine modules. Like power supplies, these e-fuses will communicate via the fieldbus to provide data on input and output voltage. By creating distinct sections within machinery or systems, these options enable distributed intelligence and targeted power management. The modular approach not only simplifies maintenance and troubleshooting but also improves operational efficiency by isolating faults and minimizing downtime.
EtherCAT’s freedom of topology and “hot connect” capabilities support modular system architectures that can be rearranged on the fly. With support for up to 65,535 nodes on one EtherCAT network, adding a few other devices will not blow up the I/O count or degrade network performance.
Whether it’s e-fuses with robust diagnostics or passive potential distribution terminals to prevent overcurrent, make sure to look for solutions that support DIN rail mounting with IP20 designs and machine-mountable IP67 options. By using e-fuses directly in the I/O segment – rather than old-school circuit breakers plus terminal blocks – machine builder OEMs significantly reduce wiring labor and material costs. Beyond that, these solutions shrink electrical cabinet footprints and save valuable floorspace in production plants where every square foot counts.
Optimizing industrial machine performance through advanced power management and monitoring solutions will become even more essential for enhancing operational reliability, minimizing downtime and maximizing efficiency. From robust UPS systems and efficient power supplies with advanced monitoring capabilities and modular solutions like e-fuses, each component plays a crucial role in safeguarding equipment integrity and ensuring uninterrupted operations without breaking the bank.
Machine builders and end users can embrace these technologies and integrate them seamlessly into existing machine designs easily, since they already require power supplies. As a result, industrial operators can proactively address operations challenges, decimate downtime and power up continuous improvement.
Azad Jafari, I/O product manager, Beckhoff Automation LLC. Edited by Chris Vavra, senior editor, Control Engineering, WTWH Media, [email protected].
MORE ANSWERS
Keywords: Uninterruptible power supply, EtherCAT
LEARNING OBJECTIVES
- Discover how power supply designs with built-in EtherCAT connectivity increase uptime through enhanced diagnostics and early warnings.
- Understand the ways that electronic fuses in standard I/O terminal form factors reduce wiring, shrink electrical cabinet footprint and free up valuable floor space in plants.
- Explore how uninterruptible power supplies reduce maintenance time and costs using capacitive and battery-based devices.
ONLINE
For more information:
www.beckhoff.com/cu81xx
www.beckhoff.com/io
CONSIDER THIS
How are you improving power supply and efficiency at your facility?