Linden Duncan did some experimenting with some thermal-enhanced oil recovery techniques using a monopole antenna and microwaves. Applications for this hybrid system include heavy oil, bitumen, and kerogen extraction. The results of this test are sufficiently convincing to require a larger-scale test.
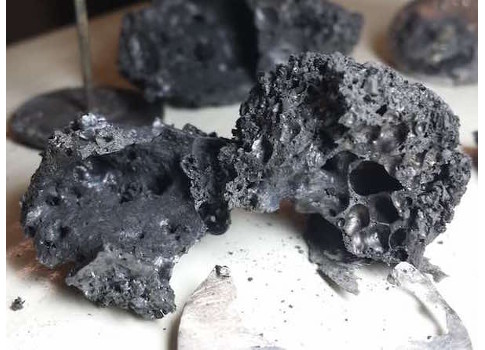
Setup, controlled heating
Heating or melting metals with microwaves typically involves a block of metal contained in a susceptor ceramic crucible. This crucible, which is lossy (meaning it absorbs microwaves), is surrounded by a thermal insulator that is transparent to microwave energy. The crucible absorbs the microwave energy and converts it into heat. The temperature inside the crucible increases until the conduction and radiant heat losses balance with the available power from the microwave source. There are refractory ceramics and alloys with melting points of 4,215 C. This technology is capable of melting tungsten at 3,400 C, stainless steel at 1,510 C, carbon steel at 1,425 to 1,540 C, and certainly wrought iron at 1,482 to 1,593 C.
However, introducing a lossy material into an oilfield and bombarding it with microwave radiation requires a massive amount of energy. For example, oil shale is a poor microwave absorbing material. Therefore, microwave absorbents must be added to reach extraction temperatures, and require a 1,700-kW microwave generator to heat each well. The most difficult problem of extracting hydrocarbons with radio frequency (RF) is power consumption. A 1,700-kW transmitter is powered for 60 days to produce hydrocarbons.
As stated by Yi Pan in Development of Radio Frequency Heating Technology for Shale Oil Extraction, March 2012: "Oil and gas can be extracted in only a few months, it is quicker than the other in-situ technology, which may need many years." Also, "Oil and gas will be extracted through producing wells after 60 days of pyrolysis of oil shale formation."
Siemens states in a commercial video of hydrocarbon extraction using the conductive sleeve that the time to produce can be 24 months. Other RF applications, such as Siemen’s RF technology, use a conductive sleeve to heat hydrocarbons susceptible to RF heating. This technology is not only limited to certain hydrocarbon formations but takes two years to produce a particularly susceptible hydrocarbon. Particular hydrocarbons react to specific frequencies. The molecules of a particular hydrocarbon may oscillate with greater amplitude in relation to certain frequencies of light; these oscillations create heat via the friction between molecules. It is like rubbing two pieces of wood to start a fire. The electromagnetic logging of boreholes is used to determine electrical parameters such as impedance matching, absorbance, resonance, and reflection between a hydrocarbon bearing formation and overbearing structure. Different geologic formations require a specific frequency using this approach. Core samples are analyzed and electromagnetic properties determined. This set of data becomes part of a computer model that will predict the change in these properties as the formation is heated. An optimal frequency is calculated for that particular formation of hydrocarbons.
Plasmonic monopole antenna
An ideal extraction technology would be a hybrid system combining radio frequency heating with the conductive heating of a plasmonic monopole antenna.
This plasmonic monopole antenna design is capable of focusing electromagnetic energy. It creates a hot spot via the thermal runaway process. This hot spot is created where the aerial meets the base of the antenna. The localized heating effect drives arc plasma from the bottom of the base. This was observed while submerging the antenna in water. The localized heating effect is similar that of a microwave drill. A gradual increase in temperature was measured at the column head outside of the microwave field, before the water was instantaneously turned to steam.
While submerging the antenna in a solid medium, a much higher temperature range was observed. Three antennae were placed in a boiler flask surrounded by crushed kerogen ore. The ore came from an old mine in Colorado. The oil shale contains an estimated 113.6 L of kerogen per ton, or 11% of kerogen by weight.
Tighter measurement, controls needed
The boiler flask was placed in a modified microwave oven. A terminator was installed opposite the magnetron to absorb excess radiation, thereby reducing the standing wave. This allowed the metallic antenna to be heated without damaging the microwave oven’s magnetron or power supply. The wall of the boiler flask and 900 g of crushed shale sitting on a glass pedestal provided the necessary thermal insulation between the antenna and oven cavity. The antenna and shale were exposed to a continuous 1,000 W of microwave energy for 15 minutes. At this time, a bright orange liquid was collected from a condenser attached to the column head emerging from the top of the modified oven.
The heat generated by the antenna could not be controlled with this setup. The temperature reached by the antenna was deduced by inspecting the remains of the boiler flask. The aluminum (which melts at 660 C) and silver (which melts at 961 C) components of the base were melted. The zinc (which melts at 420 C) coating of the fenner washer and antenna aerial were vaporized. Zinc vaporizes at 906 C. This vapor cooled, forming a vug or shell surrounding what was left of the antenna. Closer examination of the shell revealed a sintered and cratered carbon steel, base component, which indicates the materials possibly reached 1,200 C.
Assessment and adjustments
Possible modifications to this application would include antenna components with a higher melting point. The temperature must be controlled, avoiding the destruction of the antenna, while creating pyrolysis temperatures for kerogen extraction. The next experiment should test a larger antenna in the field. The location of the microwave generator and antenna should be determined to get the longest effective distance and most efficient energy use. Also, pulsing the microwave source could be part of the improvement to energy consumption.
– Linden Duncan has more than 20 years of experience with industrial automated controls covering most physical measurements. He currently works in the pharmaceutical industry. He acquired a patent for this antenna design in January 2015. Edited by Eric R. Eissler, editor-in-chief, Oil & Gas Engineering, [email protected]
– See related articles from Oil & Gas Engineering on thermal heating and heavy oil below.