The automotive industry has made many technological and safety enhancements, which can be applied to other industries. See five advances and advice on traceability and data collection, upgrades, machine vision, robotics, and safety systems.
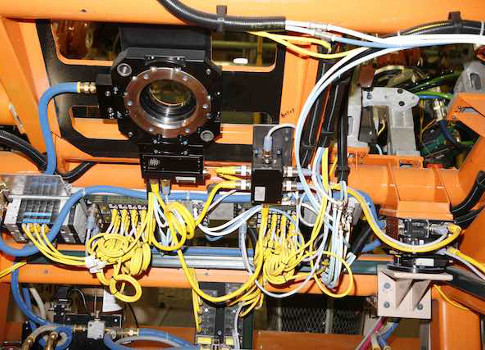
The automobile is used every day by millions of people to get them where they need to be safely. Lessons learned in the automotive industry can be applied to other industries. Five advances, in particular, should be considered if they haven’t been already, on the topics of traceability and data collection, upgrades, machine vision, robotics, and safety systems.
1. Traceability and data collection. Thousands of automotive parts are produced daily. The ability to track and collect data from a part or assembly through its process in the plant is gaining traction in the automotive industry. Parts are typically marked with a 2-D matrix barcode, and assemblies on a pallet are tracked with radio-frequency identification (RFID) tags. The data is collected by a programmable logic controller (PLC) and sent to a structured query language (SQL) database for analysis. Automotive plants can see the full history of the part or assembly from the data that is collected and can notify operators to perform maintenance, change tooling, change bearings, or other fixes to improve efficiency. This helps prevent quality issues and recalls on parts.
2. Upgrade obsolete equipment and change connectivity. The automotive industry, like any other industry, wants production systems running without any issues. Equipment and services changes have a big impact on budget and production time. Upgrading equipment such as PLCs, human-machine interfaces (HMIs), servos, and variable frequency drives (VFDs) to increase reliability and reduce downtime is becoming a larger trend in the automotive industry.
Another growing trend is the migration to Ethernet. Ethernet is designed to provide communication from the production floor to the front office; from machine to machine; original equipment effectiveness (OEE) reporting; and make data collection. Ethernet also allows workers to operate remotely, which is valuable for plant floor workers.
3. Machine vision systems. Automotive plants are using machine vision systems to check if parts are present on the line or to verify that the part was manufactured properly. Machine vision systems can inspect items faster and with more accuracy than a human, which helps keep overall quality costs down.
4. Robots. Robotic systems are known for repetitiveness and production accuracy in automotive plants. They don’t get hurt, get tired, or call in sick. They are also very useful in hazardous environments such as painting and welding. A robot can also assist with lifting heavy objects on the automotive line, which helps keep plant operators safe.
Robots are a costly investment up front for the hardware, software, programming, and integration, but in the long term they can save time and money in production.
5. Safety systems. Safety should be the number one priority in a plant. OSHA has created guidelines and ergonomic programs specifically for the automotive industry. Proper safety equipment such as light curtains, e-stops, safety mats, area scanner, and personal protective equipment (PPE) are just a few of the safety features found in an automotive plant. It has reached the point where if an employee encroaches an unsafe environment in the plant, the machine is designed to shut down to prevent any potential injuries from occurring. These safety development keep OSHA happy, but more importantly, they keep employees safe and able to continue performing their job.
Jim Sellitto is vice president of business development and Laura Mann is marketing coordinator of Martin Control Systems (MartinCSI); MartinCSI is a 2011 System Integrator of the Year. Edited by Chris Vavra, production editor, Control Engineering, CFE Media, [email protected].
MORE ADVICE
Key concepts
- The automotive industry has made several advances to improve its operations and safety.
- Upgrading obsolete equipment and improving connectivity is vital on the plant floor.
- Machine vision systems and robots can enhance safety and efficiency.
Consider this
How else can the automotive (and all manufacturing industries) improve operations and efficiency while remaining safe?