Companies are turning to their information technology (IT) departments to leverage and gain insights on the large amounts of data being generated.
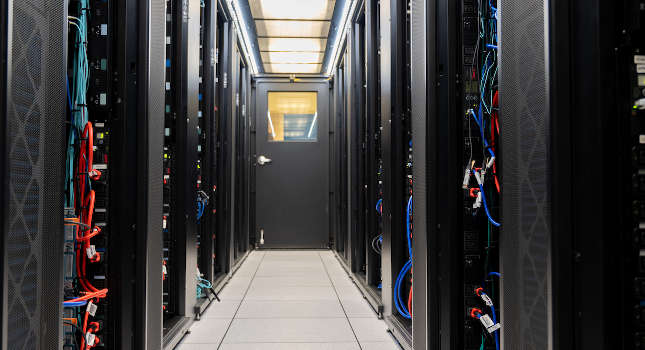
Everyone collects an exuberant amount of industrial data about their products, materials, and processes. However, manufacturers continue to struggle to leverage this data. Raw data tables and reports tend to be the most common, but they are often tied to the plant floor or use specialized software that is limited in its accessibility, which limits its potential.
Lately, we’ve seen more customers utilizing some of their in-house information technology (IT) tools to make better sense of the data that exists. Organizations are integrating their manufacturing data into their IT stack and leveraging tools stakeholders have access to across the enterprise to open communication pathways. This gives more access to more people in more departments. All of these individuals have valuable insight into their operations.
Their ability to utilize the data in new and innovative ways is uncanny. In many cases, users are able to access data on their own. By employing that sort of self-service data model, users can get useful information without needing to navigate a whole host of people and networks. By not requiring any additional touchpoints or requests to gain access to the data it lowers the hurdle for data consumption and distillation. By making the data more accessible, it also increases the likelihood and opportunity for utilizing the data in productive ways.
Leveraging and using the data effectively
One example of this is the usage and flexibility of Microsoft Teams. With more and more businesses utilizing Microsoft’s 365 platform, it makes sense to integrate manufacturing data into this pre-existing toolset. A number of customers now leverage the Teams frontend, which their employees are accustomed to, so they can easily integrate plant floor data and information in step with their planning and issues lists. This allows for team members to easily track the plan and key issues against what happens historically or in real time on the plant floor. Visualizations that are quick and simple to locate helps unlock other opportunities for better decision making.
Another way customers tap in to their existing Microsoft investment is through PowerBI. Many customers have started to use PowerBI for their data visualizations since they connect to a wide variety of data sources. Not to mention it’s easy to use to create new reports and dashboards, which help us gain additional insight from a defined set of data. Departments outside of manufacturing operations often use this tool, but it is becoming a more familiarized tool across the board at many operations. Once manufacturing data is available, they are able to apply those skills to the additional data. For the markets we serve PowerBI is the frontend visualization we leverage the most for our analytics solutions. This allows the customer to continually monitor the situation and data across a larger number of users. This flexibility creates additional views and drilldowns to better understand the nature of what’s going on in their operation.
In addition to the data visibility layer, we see a number of customers leaning more into cloud data storage and warehousing. As companies get more comfortable and feel more secure in storing data in the cloud, they are able to leverage the cost and integration benefits of scale to have more data available and correlated. By creating data warehouse views that combine related, but disparate, data sets, companies can take full advantage of a data visualization tool like PowerBI. By increasing the amount of information available and by providing relational context to allow for deeper analysis, that’s an all-around win. And by leveraging cloud-based historical data solutions, they are able to gather and store more volumes of data in an affordable manner. Both of these approaches allow for richer datasets that can yield more insights.
– This originally appeared on Avanceon’s website. Avanceon is a CFE Media and Technology content partner. Edited by Chris Vavra, web content manager, Control Engineering, CFE Media and Technology, [email protected].