Information flow and control on the factory floor can improve automation and help manufacturers make better decisions.
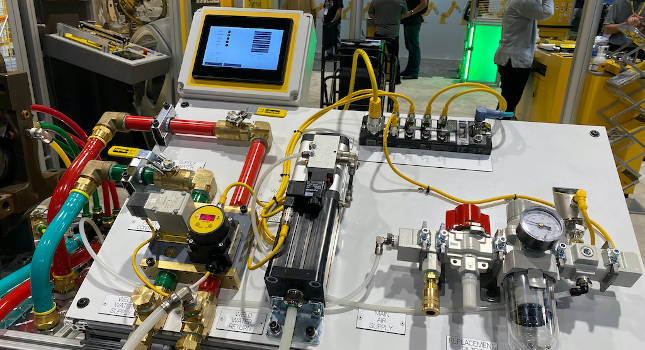
Learning Objectives
- Strong information control can improve automation and help manufacturers make better decisions.
- Infusing the automation process with artificial intelligence (AI) and machine learning (ML) to develop closed-loop control can unlock more value.
- Machine vision also helps manufacturers find flaws or defects in the production process.
Industrial automation and information flow are growing at a rapid pace. Whether its cobots, autonomous mobile robots (AMRs) high-speed lines or more, factories across the globe are looking to improve efficiency, optimize workflows, increase safety and bolster productivity.
However, there is an often-overlooked benefit of automation on the factory floor: information. When appropriately used, the data obtained during the creation of a product can help engineers make thoughtful, better-informed decisions.
The problem is many factories aren’t set up with the proper automation or control mechanisms that take products from step A to step Z. This often diminishes the information collected during the product lifecycle.
Better automation means better processes, more manufacturing information
Without automation on the factory line, the collected data is only as good as the current manual processes. Gathering information on a step-by-step basis means losing visibility into the real-time evolution of the product during its journey. It becomes difficult and nearly impossible for teams to understand potential challenges or shortcomings because they solely focus on customer specifications.
This legacy process, or total quality management, ensures teams get basic answers to questions like:
- What did you do during this step?
- How did the product meet the specifications?
- Did we adhere to the requirements?
While meeting customer requirements is a priority, without automation, teams miss the opportunistic deluge of data that can help increase throughput, cut unnecessary work and reduce downtime and waste.
The data deluge in manufacturing applications
Data that helps uncover insights on the line comes in different packets, sizes and shapes. The first group of data collected is aligned to quality and product performance during the building stage. The other information goes beyond the product attributes, helping answer important questions like:
- How long did it take to make the product?
- How many hours were spent on this particular project?
- Were the right tools used?
- What about the right components and bill of materials to make the product?
This layer of information is derived from the entire control line. It helps teams adhere to the standard operating procedures and ensures products are made per specifications based on cycle time and other leading standards.
Fully automated lines also enable engineers to receive more performance feedback than they would from a manual or semi-automated line. That’s because information control, through automated tools, delivers data as the product progresses through the line, which can be captured and visualized on monitors. For example, teams can see steps like torque value on a product fastening, ensuring requirements are being met during assembly – not after.
Fully automated lines also make it easier to relay critical information to customers. For instance, with medical devices, automated data collection allows teams to record and deliver customers with information for waterproofing, testing, hermetic sealing and other critical factors in a precise, timely and efficient manner. The same goes for other industries with stringent requirements like the automotive sector.
Getting factory lines to reach this level of automation and data collection takes time, planning and expertise.
Setting up the production line for automation success
There are two options to automate the controlling of machines and equipment.
The first is programmable logic controllers (PLCs). PLCs can be instrumental in synchronizing line controls, including speeds, interactions between material flowing in and out, and other areas. With a PLC, an operator can be sitting in front of a conveyor with a machine vision camera. When the product is placed on the conveyor, it sees it’s on the conveyor and goes through the next cycle. Although the PLC performs control feedback correctly, there is no data collection during this process – just passive, semi-automated control.
To take full advantage of the benefits of automation and the associated data, factories should consider industrial PCs (IPCs) combined with high-speed automation and sensors. These systems provide the logical programing of a PLC with advanced computing power and information control. This setup also can be supported by edge gateways to help manage the data flow.
Three steps for data acquisition for real-time analytics
The steps organizations need to take leading up to final data acquisition for real-time analytics include:
- Obtaining a better understanding of the input-output mechanism
- Using the proper sensors to collect the data
- Enabling a close loop-control program through low code/no-code application.
This smart system helps collect data throughout the entire product life cycle, unlocking many of the previously mentioned benefits. The data also can be transferred to the cloud for big data analytics or at the edge where it can process close to the machine in real-time. From here, even more value can be unlocked by infusing the automation process with artificial intelligence (AI) and machine learning (ML) to develop closed-loop control.
Five ways to unlock value with AI and ML
ML can take the vast amount of data from closed-loop control and synthesize it into actionable information that drives even better processes and more informed decision making. ML helps teams use the information for controls that can adjust parameters on a line in real-time without stopping it. ML also can be used to identify and eliminate non-value-added aspects of work such as testing a product after a certain duration of the journey.
The other driver of AI and ML value is vision. For instance, taking the data from the industrial PC-enabled closed-loop system, machines can detect blemishes or other defects like scratches on products. This anomaly detection capability allows the system to map hot spots causing these issues and flags potential problem areas to be checked out.
To get the most out of these solutions, however, it’s important to consider:
- Will you build the AI/ML or will it be a third-party purchase?
- How scalable will it be across lines?
- Who will create the algorithms and teaching models?
- Are there enough data scientists to support the project?
- Are the correct systems and employees in place to understand and interpret the data?
When automation is used to its maximum capacity, it can force strategic discipline in processes. Automation is a controlled mechanism that lets machine-to-machine (M2M) interfaces drive the product in the right sequence of steps from raw material to a transformed finished product. Information flow for product performance, quality, cycle time and managing material flow in and out of stations is also done in a synchronized manner with automation. When automation is infused with AI/ML, the possibilities are endless.
Murad Kurwa is vice president of the advanced manufacturing engineering group at Flex. Edited by Chris Vavra, web content manager, Control Engineering, CFE Media and Technology, [email protected].
MORE ANSWERS
Keywords: advanced manufacturing, information control
CONSIDER THIS
How are you using information control to improve automation at your facility?