Enhance industrial sustainability through advanced motor technologies. Deploy high-efficiency motors to reduce costs, achieve greater energy efficiency and cut CO2 emissions. High-efficiency motors and variable-speed drives decrease power consumption.
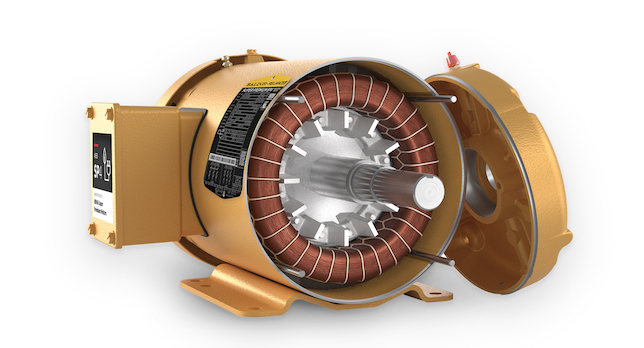
Learning Objectives
- Understand that as industrial electricity prices increase, more motor system efficiency helps.
- Learn that the global trend toward electrification includes more motor systems.
- Explore electric motor design and efficiency improvements and that electric motors can be optimized for efficiency and size.
Industrial electric motor system efficiency insights
- As industrial electricity prices increase, more motor system efficiency helps. A three-part electric motor system article looks at ways to improve industrial sustainability, reduce costs, save energy and cut carbon-dioxide emissions.
- The global trend toward electrification includes more motor systems.
- Electric motor design and efficiency can improve, electric motors can be optimized for efficiency and size.
Electric motor systems with advanced motor technologies help industrial energy efficiency, lowering costs and reducing carbon-dioxide emissions.
It is estimated that by 2050, the global population will rise to 9.7 billion, from 7.7 billion in 20191, and the global economy is expected to more than double over the same period.2 The United Nations projects that the global urban population will increase to around 68% by 20503, and this rapid urbanization, combined with automation and rising standards of living, will increase the demand for energy globally. To protect the environment without tempering economic growth, we need to reduce the consumption of energy and natural resources.
A three-part article series explores how industries can meet these challenges sustainably. This article, first in the series, focuses on the pivotal role of high-efficiency electric motors and the tangible solutions they offer in reducing energy consumption and operational expenses.
Industrial electricity prices increased; more efficiency helps
Rising demand for electric energy is leading to a corresponding increase in energy costs. The industrial sector has experienced an 18% increase in electric prices over the last four years. This surge is having wide-ranging effects as higher electricity prices directly impact operational expenses and increase production costs. Industries relying heavily on electricity, like chemicals, metals and basic materials, are reassessing their cost structures to maintain profitability. Increased electricity prices are leading to higher input costs for goods and services that are reliant on electricity-intensive manufacturing and resulting in higher prices. In response to these challenges, industrial companies are considering strategies like adopting energy-efficient technologies, diversifying energy sources and collaborating with policymakers to promote affordable energy. In the meantime, immediate and significant reductions in energy consumptions can be realized by the adoption of optimized, high-efficiency equipment – such as industrial electric motors.
Global trend toward electrification includes more motor systems
In line with these global trends toward electrification, the demand for systems powered by electric motors is expected to grow significantly. According to the International Energy Agency, industry accounts for 37% of global energy use and buildings account for around 30% of global energy consumption.5 Much of this energy is consumed by electric motors. It is estimated that roughly 70% of electricity consumed by industry is used by electric motor systems6.
Electric motors have been in use for more than 150 years. Small motors are found in the compressors used in air conditioners and refrigerators, computer printers, the cooling fans of electronic appliances and other common devices. Mid-sized motors appear in heating, ventilation and air conditioning (HVAC) systems, as well as in elevators and electric automobiles. They are used extensively in industry; for pumps, conveyors, fans, and mechanical motion of all kinds. The largest electric motors are found in railway engines, cable cars, ship propulsion systems, and heavy equipment of the sort used for compressors or material processing. While large motors represent only 0.03% of all motors in use, they account for about 23% of all electric consumption by motors globally, or 10.4% of all electric power usage. The smallest motors, with an output of less than 0.75 kW output, account for just 9% or so of electric motor power consumption.9 The trend in industrial design has been toward the use of more and smaller-sized motors, optimized for specific tasks. Matching the output of a motor to the maximum power required for a task already represents a major step toward achieving greater energy efficiency.
Electric motor design, efficiency improvements
Electric motors of all sizes have improved steadily over time. In the past 10 years, they have undergone a period of exceptionally rapid technological advancement, and with that an opportunity to reduce the energy consumed by industrial and commercial electric motors. An expanding range of advanced energy-efficient electric motors are now available on the market, and the adoption of these motors continues to increase.
Modern induction motors operate at very high levels of efficiency. Motor efficiency is rated according to scales published in the United States by the National Electrical Manufacturers Association (NEMA) and in Europe by the International Electrotechnical Commission (IEC). Almost all industrial electric motors sold in the U.S. must meet NEMA Premium efficiency, while in the EU they must meet IEC IE3 efficiency, which means motors in these markets are highly efficient. An example is a 200 kW (268 HP) AC induction motor that meets the NEMA Premium Efficiency (IE3) standard achieves roughly 96% efficiency. Compared to other types of motors, such as internal combustion engines (20-40% efficient) or hydraulic pumps (80% efficient), the electric motor by far the most efficient. Some of the very latest electric motors meet an even higher standard for efficiency, which is the NEMA Super Premium (IE4) standard. Motors that meet this standard have about 15% less energy losses than those delivered by NEMA Premium Efficiency/IE3 motors, and the more recent IE5** motor represents the highest level of efficiency that has been met by any current design.
Older electric motors can be optimized: Efficiency, size
Many electric motors in use today are of the older, less-efficient, designs and are often over-sized, which wastes even more energy. Considerable gains in efficiency may be achieved simply by deploying higher-efficiency motors that are correctly selected for the application in question. Electric motors in U.S. facilities convert more than 1,080,000,000,000 kilowatt-hour per year of electricity into motion at an operational cost of $112,300,000,000 per year to operate. Simply by switching to NEMA Super Premium Efficient (IE4) of motors, U.S. industry alone could save $1,680,000,000 per year.2,7
It’s clear that deploying high-efficiency motors represents a tremendous opportunity as the world seeks to reduce costs, achieve greater energy efficiency and cut CO2 emissions; however, there are additional steps motor operators can take to achieve even greater levels of savings, control and precision. Modern, high-efficiency motors, paired with variable speed drives, offer even greater reductions in power consumption.
Part two of this series will cover variable speed drives, exploring how these technologies further optimize energy consumption and enhance industrial efficiency, setting the stage for maximizing energy efficiency with smarter motion services in part three.
Benjamin Hinds is the vice president of product management and marketing at the NEMA Motors Division of ABB. Edited by Mark T. Hoske, editor-in-chief, Control Engineering, WTWH Media, [email protected].
MORE ANSWERS
KEYWORDS: Industrial motor system efficiency, electric motor efficiency
CONSIDER THIS
Create industrial savings and environmental benefits with greater motor system efficiencies.
Motor efficiency footnotes and references
*NEMA vs IEC efficiency ratings are not exact matches, but relative comparisons.
**NEMA has not yet designated an IE5-comparable standard.
(1) United Nations, Department of Economic and Social Affairs, Population Division, “World Population Prospects 2019: Highlights,”
(2) Guillemette, Y. and D. Turner (2018), “The Long View: Scenarios for the World Economy to 2060,” OECD Economic Policy Papers, No. 22, OECD Publishing, Paris.
(3) United Nations, Department of Economic and Social Affairs, Population Division, “World Urbanization Prospects 2018: Highlights.”
(4) IEA, “Tracking industry 2020,”
(5) U.N. Environment Programme, Global Alliance for Buildings and Construction, “Why buildings?,” 2019 (2018 IEA data),
(6) Fong, J.; F. Ferreira; A.M. Silva; and A.T. De Almeida, “IEC61800-9 System Standards as a Tool to Boost the Efficiency of Electric Motor Driven Systems Worldwide,” Inventions, 2020, 5, 20.
(7) Stoffel, B., “The role of pumps for energy consumption and energy saving,” 2015.
(8) U.S. Industrial and Commercial Motor System Market Assessment Report, Lawrence Berkley National Laboratory, January 2021