Industrial Internet of Things (IIoT) technologies have the potential to improve user benefits through diagnostics, prognostics and predictive maintenance.
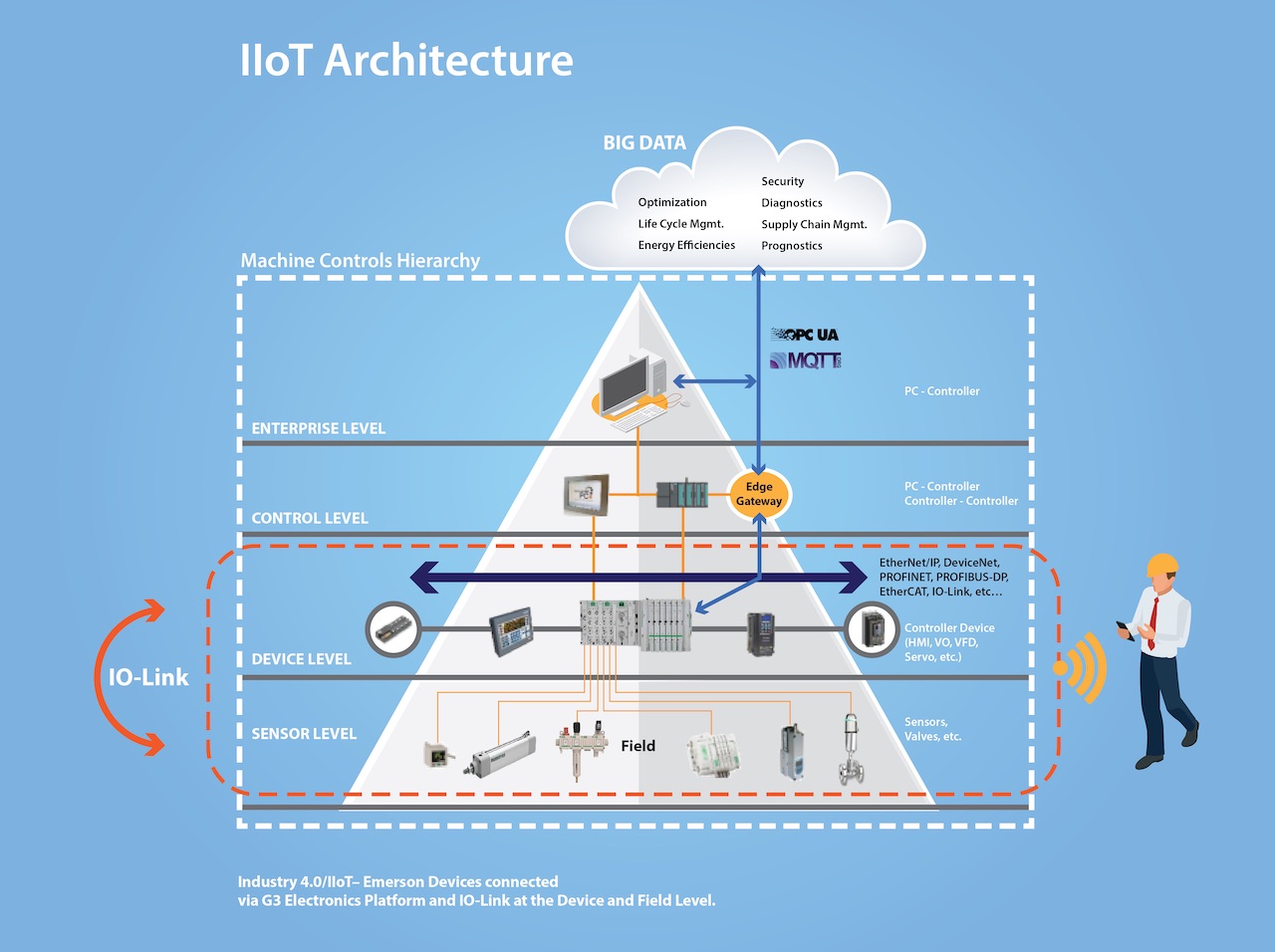
Consider this scenario: An operator on a beer bottling line experiences a sudden equipment shutdown. The operator has no need to access the programmable logic controller (PLC) program or disrupt the network. Instead, the operator pulls out a smartphone, connects to the machine’s pneumatic valve system, and pulls up a web page showing diagnostic data on the equipment’s pneumatic system performance. It’s apparent a solenoid coil has burned out in a directional control valve that controls one of the machine’s actuators. Within minutes, a maintenance technician plugs in a new control valve and the bottling line is running again with little lost productivity or major control system intervention.
This hypothetical example illustrates one of the many advantages new Industrial Internet of Things (IIoT)-ready technologies can bring as they enter the machine control market. These technologies promise to improve user benefits with better diagnostics, prognostics and predictive maintenance. As a result, users will experience increased productivity, decreased downtime and reduced maintenance costs at unprecedented levels.
IIoT technologies are still in their infancy and currently are implemented in the machine control environment on an ad hoc or opportunistic basis. In these experimental and pilot applications, manufacturers are identifying small, focused production problems, and then employ IIoT solutions at the foundation level to solve them. Gateways export data from the machine’s control system for analysis and storage on-site or in the cloud. Analytics are run remotely to better understand the problem and indicate a resolution.
For example, a production supervisor might be concerned about a machine’s peak energy usage. The equipment’s energy usage data is correlated with other operating data pulled from smart sensors installed on the machine. With this analysis, the supervisor can identify the time and operating factors when the spikes in power consumption occur.
Connected devices, machine backbone
The pilot projects of today will lead to the plant-wide projects of tomorrow as new IIoT-enabled machines and networks reach the market. The new architectures will combine smart devices (such as sensors, input/output (I/O) modules, servo drives, robots, motor starters, etc.) with smart pneumatic valve systems incorporating industrial network interfaces, integrated I/O and local analytics capability. These smarter connected devices will form the backbone of the machines’ controls and have IIoT connectivity.
While industrial networking has been used in higher-level devices for decades, it’s been too expensive to integrate into small field-level sensors. Adding a point-to-point communications technology that uses existing cabling infrastructure, such as IO-Link communications, allows data extraction from smart sensors and devices.
The combination of wireless connectivity, mobile devices and wireless diagnostics and prognostics provides smart pneumatic manifolds with the analytical capabilities required for IIoT applications. The technologies deliver data from the field devices (smart sensors) through pneumatic manifolds into a machine control system.
This diagnostic and prognostic data also can be routed through a separate gateway and channel that isn’t a part of the control network. This allows external devices to collect, analyze and act upon relevant process data efficiently without loading the control network with diagnostic data. It also allows users to analyze this data without affecting the machine’s process or production schedules. This IIoT-driven data analysis also can be retrofitted on existing machines.
Role of IO-Link
IO-Link (IEC 61131-9, a standard for sensor and actuator communications) allows even the smallest field devices and smart sensors to communicate their diagnostic data for analysis to understand functional and system status. IO-Link technology was conceived for setting and changing functional parameters on smart sensors using the same existing connecting media. Today, it has developed into a communication technology that allows control of non-sensor devices such as proportional pressure regulators and valve systems.
IO-Link typically is used in conjunction with a communication gateway to higher-level industrial networks such as EtherNet/IP, Profinet, EtherCAT, etc., to allow network communication to reach the lowest layer of the control system. Through these IO-Link master gateways, smart devices can send diagnostic and prognostic data digitally to high-level processors for analysis, which can take place in a local, on-site or cloud environment.
New modular fieldbus valve manifolds will have the added benefit of hosting multiple IO-Link masters and act as a gateway to one Ethernet communication node. This eliminates the requirement to have a communication node for each IO-Link master, which reduces cost and complexity.
Due to the modular nature of today’s fieldbus manifolds, IO-Link master modules designed to integrate to a modular fieldbus valve manifold also can be distributed up to 30 meters from the fieldbus communications node, allowing convenient placement of sensors and devices on the machine. The IO-Link master modules can incorporate auxiliary power connectors for each individual IO-Link channel to provide machine designers with increased flexibility, efficiency and additional safety options.
Local Wi-Fi communication will be integrated on the pneumatic valve system to simplify machine maintenance and commissioning. The user has easy data accessibility via any Wi-Fi-enabled mobile devices without needing to download any apps. The operator or maintenance technician connects the mobile device to the Wi-Fi network and an HTML web page with the machine’s analytical data is served up to the device in the appropriate format.
Plant-wide IIoT implementation
After local experimentation, IIoT technologies will be implemented more readily on a plant-wide, operational level, and substantial benefits will be generated in machine uptime, operator safety, commissioning and product quality.
IIoT technology reduces machine downtime by allowing predictive maintenance, which enables operators to identify and resolve problems in a planned and orderly fashion without disrupting the production process. Prognostics allows real-time analysis with the capability to continuously monitor the machine’s performance without adding overhead to the control system. Directional control valves can be monitored for time, distance and the extent of their lifecycles. The user is alerted when there are deviations from normal operating parameters. Prognostics are a major step beyond preventive maintenance and facilitates the adjustment, repair or replacement of a component before it creates an impact on machine performance.
IO-Link communication technology allows low-level devices to communicate to high-level networks in a simple, but economic way. This also brings industrial communication to even the smallest device, enabling the promise of IIoT.
Wireless connectivity also permits maintenance personnel to monitor pneumatic valve systems and their connected devices in hard-to-reach locations deep inside the machine. They can diagnose a wire break, an inoperable communications module or a failed valve coil without shutting down the system or climbing around the equipment.
An IO-Link sensor’s status also can be checked with a mobile device. The new smart sensors alert the user if they are broken and why they failed, which makes them much easier to fix. Sensor commissioning and replacement is simplified since the parameters already will be set with an .iodd file.
The data generated from IIoT-enabled machines also can help diagnose problems that impact product quality. For example, the data from a machine’s sensors might indicate one of its pneumatic cylinders is not fully extending. That erosion in movement potentially could cause deterioration in the manufactured product’s quality over time. The ability to understand a component is drifting out of specification before it affects product quality will be an important advantage.
Better information for engineers
As these technologies begin appearing in machine control systems over the next few years, they will produce improved diagnostics, simplified commissioning, better safety and more consistent asset availability than before. These benefits will have important ramifications for machine builders and end-user customers in the automotive, pharmaceutical manufacturing and food and beverage industries.
Users will soon apply these technologies to solve the big problems in their manufacturing systems. For the first time, these solutions will be based on data from lower-level sensors measuring machine performance — and the data collected will automatically or systematically improve overall operations. Analyzing this new data will create relevant information that allows machines to operate more efficiently and effectively with less downtime.
Steven Fales, product marketing manager, fieldbus electronics and valve systems, Emerson Automation Solutions. Edited by Chris Vavra, production editor, Control Engineering, CFE Media, [email protected].
MORE ANSWERS
Keywords: Industrial Internet of Things, IIoT, IO-Link
Easier communications help create the Industrial Internet of Things (IIoT)
Less downtime and greater reliability will result.
Consider this
What specific benefits can IIoT and IO-Link communications bring to your plant?
ONLINE extra
Learn more about Asco and IO-Link.