Machine control needs to evolve to handle ever more complex processes as operational technology (OT) and information technology (IT) systems converge.
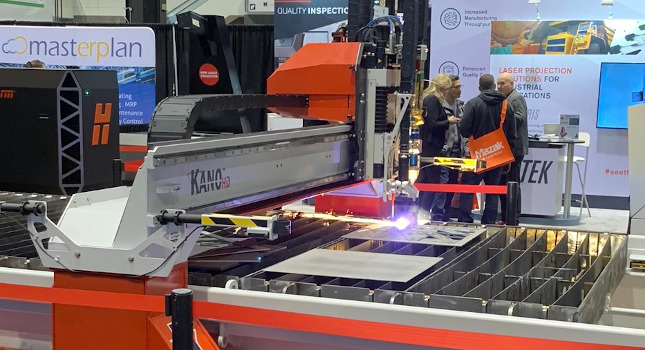
The manufacturing industry has been hard hit by the challenges relating to the ongoing pandemic. With customer demands and costs continuing to rise, manufacturers need to prepare themselves for the long-term impact of Covid-19.
There is a need to become more flexible to meet evolving customer needs, while also increasing efficiency and remaining competitive. The key component to achieve these goals has not changed – digital transformation is still the main enabler.
Employing the latest digital technology on the factory floor will help drive the convergence of operational technology (OT) technology with information technology (IT) systems, enabling businesses to create the platform to improve productivity exponentially. This is where automation and robotics come into play.
Regardless of the fact that very few greenfield factories are being built – businesses need to consider digitizing their existing plants. This can take the form of employing additional sensing technology on existing machines/lines and/or integrating modern automation and robotic systems within existing facilities and then linking these to information systems for analysis and decision making. Providing real time data from across an enterprise – especially when combined with historic information and third-party data – can provide the input for artificial intelligence (AI) system or humans, to make valuable and informed decisions.
The quality and reliability of power is critical to any production facility and as we move into a world where will have to closely manage demand against a variable supply, the connection of energy and automation systems and the integrated management of them will become critical for highly optimizing productivity.
Production is always at risk from human error, which can result in downtime, reduced product quality or product waste. The more the process can be automated – including the introduction of robotics and “cobots” – compact, easy-to-use and collaborative robots to work alongside humans – the more the risk can be reduced.
During the last few years, the programmable logic controller (PLC) has been a fundamental tool in materials handling and packaging solutions. The benefits of using a singular range of equipment has ensured that end users have reduced downtime and improved long-term efficiency. Yet, as a result of the increased demands of flexibility and pace of packaging lines, traditional PLCs have become outdated.
PLC substitution
With increased demand for automation, PLC-based control is being substituted by the latest generation of high-performance integrated motion and robotic controllers which have intertwined PLC sequence capabilities. This enables more complex applications to be handled, with higher production speeds and in smaller spaces, with faster payback and better return-on-investment.
We are getting ever closer to the ‘lights out’ manufacturing plant. While many factories today are still made up of a series of unconnected systems and processes, as we become more digital and connect them there will be a marked contrast in efficiency levels compared to those before new technology implementation. Adopting new technology will provide greater visibility into production, and the actionable data needed to be more agile in response to market demands – at a much lower cost.
To ensure organizations continue to be profitable and competitive, there is a need to adopt new and improved technologies. Plants and machines need to become smarter and more efficient to guarantee success.
This article originally appeared on Control Engineering Europe’s website.